Early alerts let operators clear chutes and remove partial plugs and quickly restart. Blocked chutes can domino into big problems with damaged equipment, wasted material, stopped production, and even injury.
BinMaster sensors alert operators early when chutes need attention. Relays trigger alerts so operators know there’s a problem via an indication on a point level alarm panel or to a control room. Several technologies are available:
- Flow Detect uses a microwave Doppler effect to sense whether material is flowing or not.
- Capacitance probes detect the presence or absence of material.
- Rotaries and vibrating probes can be installed in y-pipes to sense blockages as well.
Chutes plug due to moisture, compaction, particle size, interlocking material, up-stream and down-stream equipment failure, buildup, foreign objects, and chute design. The German Engineering Federation found that 75% of respondents experienced chute blockages. The average downtime was six hours translating to $250,000 per incident.
EHS Today said that 25% of workplace accidents in the manufacturing industry are related to blocked or poorly-maintained machinery, including chutes. The problem can be tackled by prevention with better chute design and sensors to alert operators of a low-flow or no-flow condition.
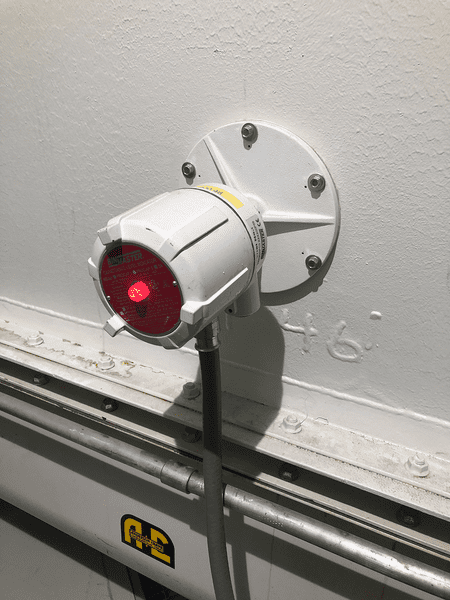
“We’re get a lot of calls about chute detection,” said Nathan Grube, BinMaster VP Central Region. “Companies are tightening processes. They forecast success, which they should. But that means they have less room for error.” No one should accept hours of downtime because of something preventable.
Grube said chute detection complements good chute design to prevent damaged material and extra dust as well. “Usually, we get a call after a plugged chute incident,” Grube said. “It’s just one of those times where they kind of mumble, ‘I wish we would have done it sooner.’ “