Regardless of the industry or type of mixer, quality and performance are crucial to attain the required product specifications while meeting inevitable changes in customer demand. In addition, with the current cost of labor and energy so high, it is vital to optimize efficiencies wherever possible for long-term profitability.
To this end, industrial processors are increasingly seeking mixers with design features and capabilities that improve performance, provide more flexibility of mixing style, limit product loss, simplify cleaning requirements, and reduce capital equipment and ongoing maintenance costs.
For guidance on these issues, we have turned to John Paul, CEO and Managing Director of PerMix Tec Co. Ltd. – North America, a subsidiary of PerMix, a global supplier of industrial mixing and processing equipment for powders, pastes, and liquids since 1954. Today, the OEM is the world’s largest mixer manufacturer in terms of the variety of types and styles offered with over 2,000 global business customers.
Easy to Clean Mixer Designs
Periodic mixer cleaning is essential to maintain sanitary conditions, ensure product quality, and facilitate production changeover. Between each batch, the mixer is turned off, opened, and cleaned thoroughly to ensure there is no material residue. In industries like food processing, an SQF practitioner also swabs the area to confirm that it is free of allergens and pathogens.
However, some mixers can be difficult to access and clean, which increases time and labor. In modern industrial mixers, two innovative design features – the stub shaft and cantilever end door – are specifically intended to simplify cleaning and minimize production downtime.
Stub Shaft Design
Although there are many types of mixers, most involve a rotating impeller to mix material. The agitator assembly must therefore be mounted securely to ensure proper mixing, yet also be removable for cleaning or maintenance.
The challenge is that conventional agitator assemblies are mounted using a flange and bolts that are located inside the mixing chamber. This arrangement leaves crevices or grooves where allergens, pathogens, or other potential hazards can accumulate that are difficult to access and clean.
In contrast, with stub shaft designed mixers, the agitator assembly is mounted on the exterior of the chamber, eliminating this concern. The design allows maintenance crews to efficiently remove the agitator assembly, replace the seals, and reassemble the components in under 30 minutes, maximizing production time.
Cantilever Design
Compared to traditional equipment, cantilever designed mixers streamline cleaning by allowing the operator to easily open the machinery and access crevices and hard-to-reach areas. Some high-volume industrial mixers can measure 40 feet long and 14 feet in diameter, large enough to qualify as a confined space, and therefore subject to safety regulations by OSHA when entry for cleaning is required.
Most conventional mixers are designed using large pneumatic or hydraulic cylinders on the top or bottom of the mixer to slide the end plate in or out for cleaning and maintenance. However, the cylinders essentially double the size of the mixer and, when opened, the extended agitator element and end plate poses a trip or “head banging” hazard to personnel, as well as a hazard to forklifts. Hydraulic and pneumatic components also significantly add to the overall cost of the equipment.
In contrast, cantilever designed mixers eliminate the need for confined space entry into a mixer, while improving access without need for pneumatic or hydraulic elements. Instead, the cantilever end plates extend out and pivot on a hinge, or arm, allowing for much greater interior access than a traditional mixer.
“We install the end plates on hinges mounted to the main mixer body or another stationary object so you can simply unlock the end plates and swing them open,” says Paul. “If a very large mixer is used, the OEM may mount an end plate on a supporting pedestal that swings open, so the hinge provides a continuous run of the entire mixer.”
When using a cantilever mixer, the end plate can be locked in a specific position or allowed to rotate. Each end plate can be further adjusted to enable opening in tight or restricted areas.
“This enables greater flexibility when cleaning since you can easily move the end plate around to access different areas,” says Paul.
Minimize Product Loss with Innovative Mixer Designs
Processors expect a certain amount of product loss and residue when using horizontal mixers. Fortunately, several design options have been developed that help minimize waste.
Offset Discharge Valve
Horizontal mixers tend to waste a considerable amount of product, particularly when the discharge valve is positioned in the center of the mixer. To minimize the product loss, PerMix utilizes a slightly offset discharge valve.
“The discharge valve is offset at a 15° angle, so it reduces the residue left in the mixer from an average of 2-3% to just 1%. With agitation style rotation, the powders create a slope inside the mixer that increases the total discharge,” explains Paul.
Bomb Bay Doors
Bomb bay door designs can further reduce product loss and residue on horizontal mixers.
Since bomb bay doors can extend the full length of the bottom of the mixer, there is essentially nowhere for product or residue to remain after gravity-fed discharge when the doors open. Additionally, the design significantly shortens the discharge time, which reduces the batch time and increases production.
Vertical Mixers
Although most mixers are horizontal in design, a vertical mixer can dramatically reduce product loss. With vertical mixers, there is 100% discharge of product, leaving no residue in the equipment as all product discharges through a single shaft, fed by gravity.
Vertical mixers also provide more surface area for heat transfer, so can be more efficient when heating or cooling product. In addition, vertical mixers require less floor space than horizontal units and offer more flexible minimum batch sizes.
Seek Flexibility in Agitation Style
According to Paul, industrial processors are increasingly seeking more flexibility in their mixing capabilities for multiple reasons. Often, they must mix ingredients of diverse densities or viscosities and mixer systems are generally not interchangeable. The requirements may also change due to customer or market demands. In any case, processors increasingly do not want to be committed to any single mixing style on the production line. Contract processors, by definition, also value flexibility of agitation style due to the variability of production needs they must fulfill with each new project.
In response, leading mixer OEMs are developing mixers that simplify changing agitation styles without having to reconfigure the production floor.
“Processors can have multiple styles of agitation and switch them according to their mixing requirements,” says Paul.
PerMix even manufactures a “four-in-one” machine that can be easily converted from a fluidized zone mixer to a plow, paddle, or ribbon mixer when needed. In addition to converting the agitation style, the mixer is segmented into two parts to allow for multiple configurations.
“When you switch from a paddle on a plow mixer, you need to also switch from a U-shaped trough design to tubular. You can do this by removing the two sides. When you switch from a plow mixer to a panel mixer, the round top is changed,” he explains.
The OEM originally developed the design for its test lab to enable a single machine to perform the work of its four most popular mixer types. After strong customer response, the company now offers the four-in-one design to various industries.
Find Ways to Reduce Capital and Operating Costs
Paying less for an industrial mixer is always preferred. Unfortunately, the component manufacturers and middlemen involved in fabricating, selling, integrating, and maintaining most industrial mixers can substantially increase the purchase price.
As a solution, some vertically organized mixer OEMs like PerMix can reduce the overall cost by a factor of 3 or even 4x by manufacturing all components in-house, in the USA. Larger mixer manufacturers can also leverage their purchasing power with distributors to receive substantial discounts based on their volume, which is then reflected in the final price.
Simplified design features can also reduce costs. While a conventional mixer with hydraulic pistons can cost from $30,000 to $60,000 depending on its size, a comparable cantilever designed mixer can cost less than $10,000.
Paul cautions processors to watch out for manufacturers that tack on extra fees after the initial quote.
Another aspect of affordability is lowering the long-term cost of maintenance and production downtime, which can escalate if replacement parts are unavailable or must be ordered with long lead times. For large, multinational operations, this can become an issue if the necessary replacement parts vary in design or manufacture from region to region due to different local sources.
Ideally, the OEM would instead provide consistent and standardized components to any location worldwide.
“Offering the same equipment design and replacement parts reduces service and training time, and ensures a more consistent mixing performance,” says Paul. “Our multinational clients order the same components on every mixer, saving money on spare parts and training.”
Although the specific types of mixers and options vary by industry and application, selecting state-of-the-art designs that allow greater diversity of mixer style, along with efficiency on the production line, is becoming a best-in-class practice among processors.

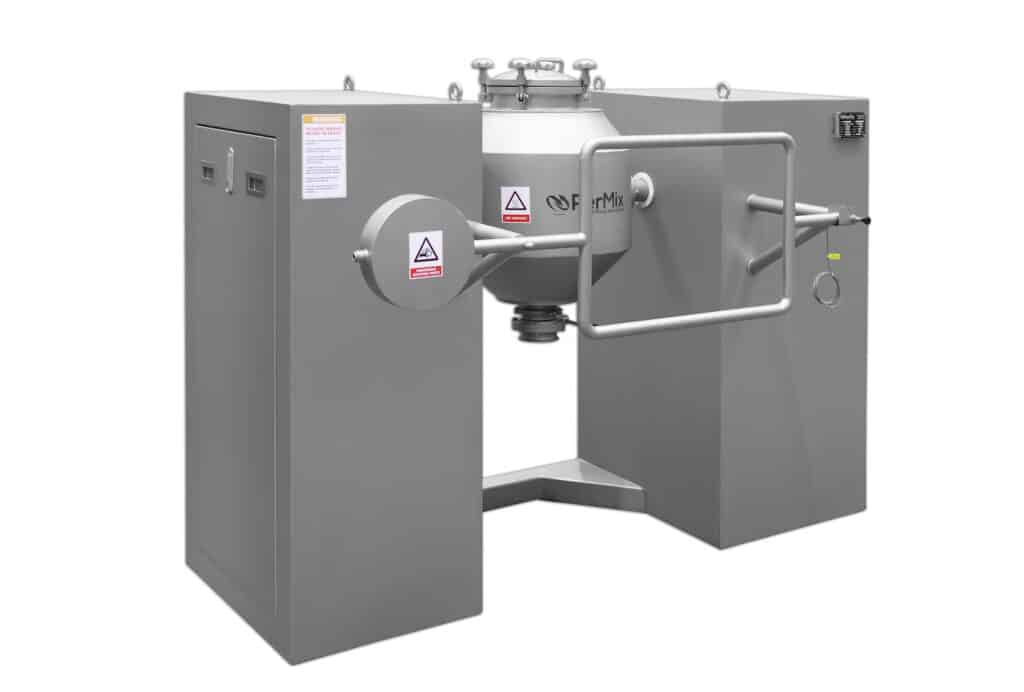
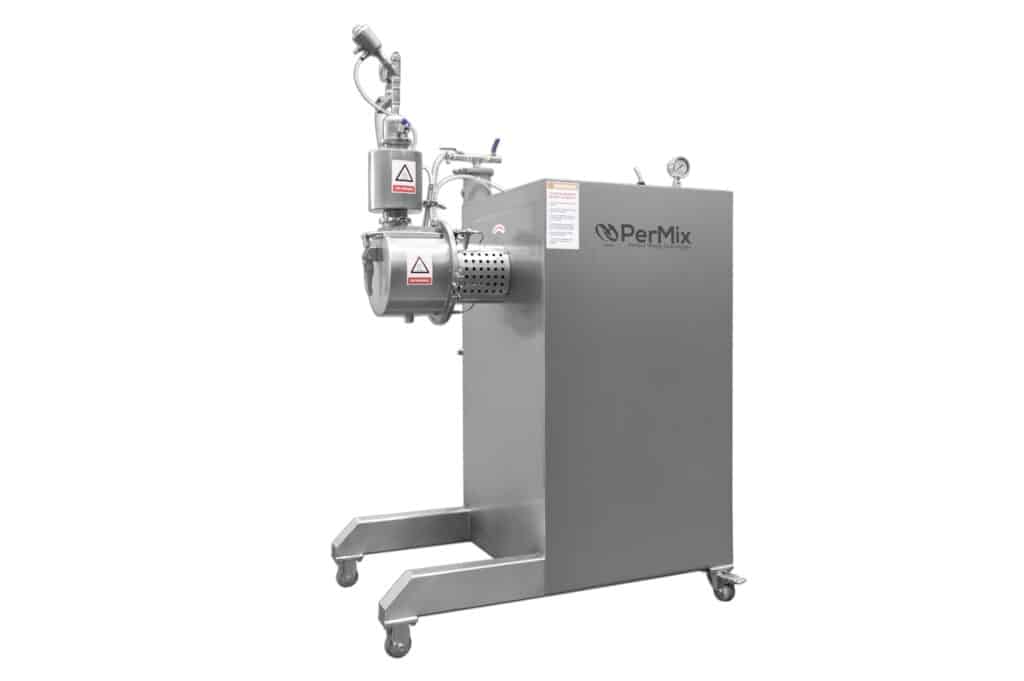