These processes are common in industries such as pharmaceuticals, food and beverage, chemicals, and more. Here are some key aspects related to thermal solids processing and the types of mixers used:
Thermal Solids Processing:
Purpose:
Thermal solids processing involves mixing or blending solid materials at high temperatures to achieve specific product characteristics or reactions.
Applications:
Common applications include mixing powders, granules, or particles to create homogenous blends.
Thermal solids processing is often used in industries where heat-sensitive materials require controlled temperature environments.
Challenges:
Controlling temperature and ensuring uniform distribution of heat throughout the mixture are critical challenges.
Avoiding degradation or unwanted reactions due to high temperatures is essential.
Types of Mixers Used in Thermal Solids Processing:
Ribbon Blenders:
Design: U-shaped trough with an agitator consisting of inner and outer helical ribbons.
Advantages: Suitable for powders and cohesive materials, provides good mixing efficiency.
Paddle Mixers:
Design: Consists of paddles or blades mounted on a horizontal shaft.
Advantages: Effective for blending cohesive materials, suitable for heat-sensitive products.
Plow Mixers:
Design: Equipped with multiple plows that move material in a fluidized state.
Advantages: Promotes fluidization and is effective for heat transfer, suitable for fragile materials.
Double-Cone Blenders:
Design: Two cone-shaped ends with a cylindrical center, rotates on its axis.
Advantages: Gentle blending suitable for fragile materials, good for small to medium batches.
Vertical Screw Mixers:
Design: Consists of a vertical screw within a cylindrical chamber.
Advantages: Suitable for continuous processing, effective for heat-sensitive materials.
Fluidized Bed Mixers:
Design: Utilizes an upward flow of air to fluidize the mixture.
Advantages: Facilitates heat transfer, suitable for delicate or heat-sensitive materials.
Rotary Drum Mixers:
Design: Rotating drum with internal fins or blades.
Advantages: Efficient mixing for large quantities, suitable for continuous processing.
Planetary Mixers:
Design: Mixing blades rotate on their own axes while orbiting the central mixing point.
Advantages: Provides thorough and high-intensity mixing, suitable for various applications.
Considerations in Mixer Selection for Thermal Solids Processing:
Heat Transfer:
Efficient heat transfer capabilities to maintain uniform temperature.
Material Characteristics:
Consider the properties of the materials being mixed, such as size, shape, and heat sensitivity.
Batch Size:
Choose a mixer size and type that aligns with the desired batch size.
Process Control:
Adequate control mechanisms for temperature, mixing speed, and duration.
Material Handling:
Consider ease of loading, unloading, and cleaning.
Safety:
Ensure safety features to handle high-temperature processing.
It’s essential to consult with process engineers and mixer manufacturers to select the most suitable mixer for specific thermal solids processing requirements. The choice of mixer depends on the characteristics of the materials, the desired outcome, and the scale of production.
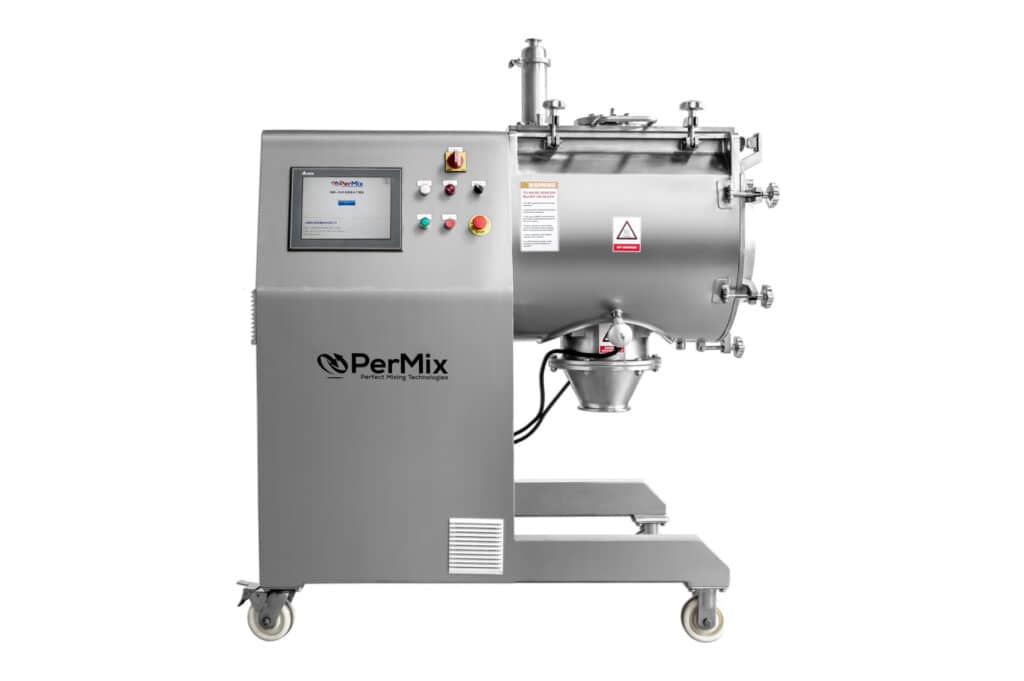
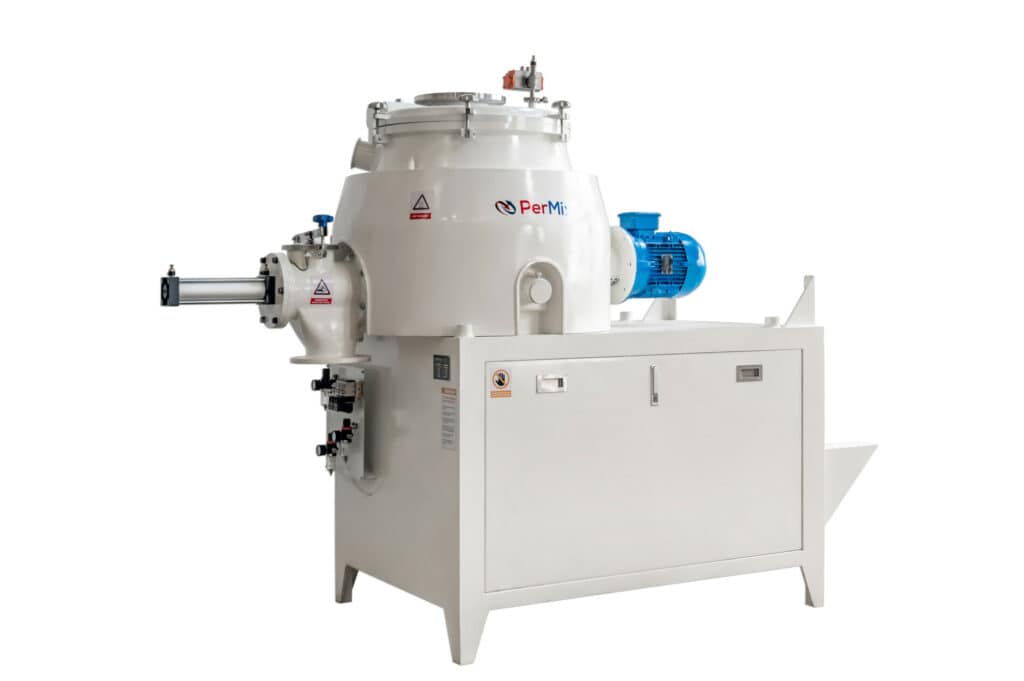
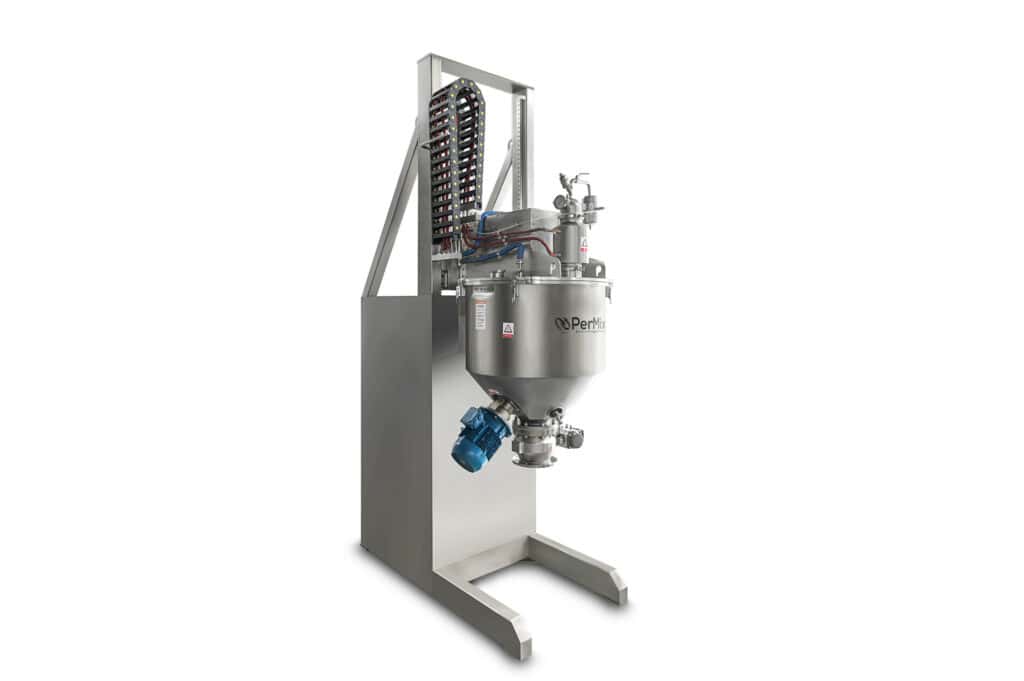