What is abrasion and why is it important to prevent it?
Abrasion is the process by which solid materials in motion rub against each other and against the mixer tank. This phenomenon can lead to wear on the mixer’s walls and tools, resulting in damages and cracks in the structure. Wear also affects mixing quality and reduces mixer efficiency. Abrasive materials such as sand, cement, metallic powder, etc. are particularly problematic, as they can cause severe wear in a short amount of time.
How to protect your mixer against abrasive products?
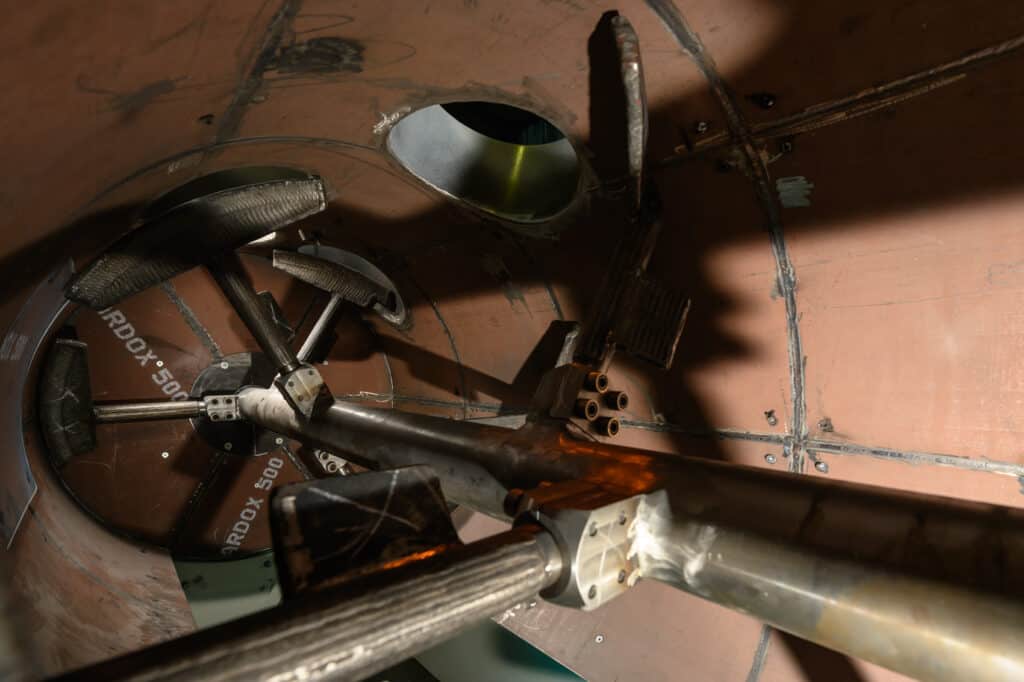
To prevent the mixer from wear and tear due to abrasion, plenty of abrasion protection devices can be added to your industrial mixers.
Abrasion-resistant materials
The first solution is to use wear-resistant materials for the construction of the vessel and tools, such as abrasion-resistant steel or specific alloys (e.g. Hastelloy, which resists both abrasion and corrosion). The mixer walls are made from one of these materials to increase their lifetime with abrasive products. The choice of material depends on the specific characteristics of the abrasive product, such as hardness, particle size and chemical composition.
Shields and coatings
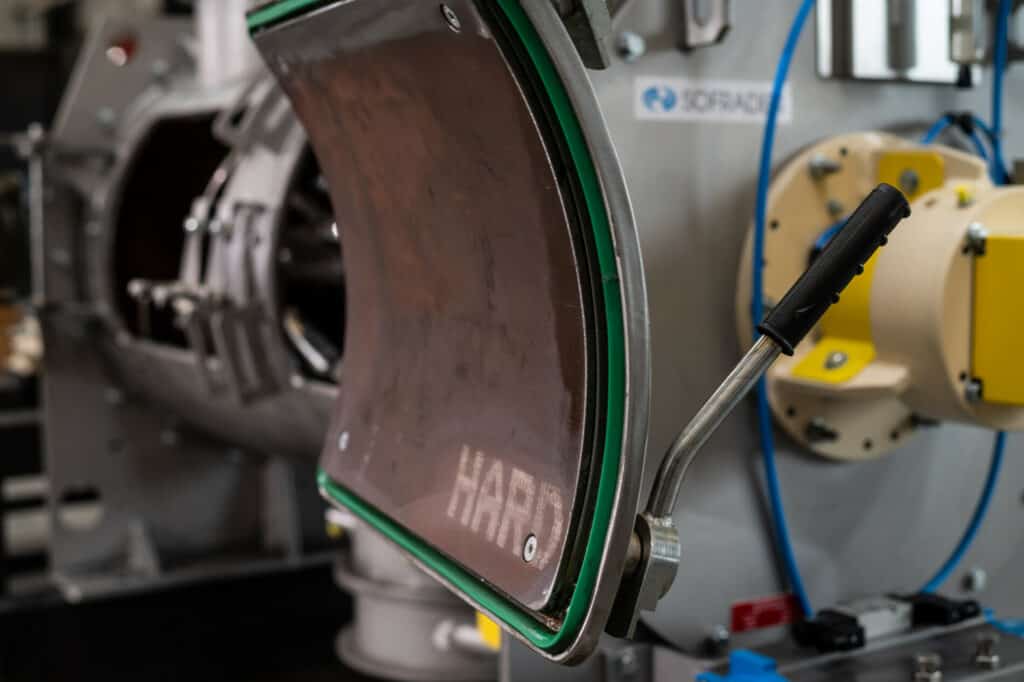
Another solution is to use shields made of abrasion-resistant materials, rubber or ceramics. Shields are attached to the mixer walls to form a protective layer against abrasion. This is an interesting alternative if the products mixed are also corrosive: a steel shield is added to a stainless steel vessel. Another advantage of the shield is that it can be changed once it has worn out.
For mixing tools (paddles, lump breakers, ribbons, troughs), coatings such as tungsten carbide are available.
Regular maintenance
Regular maintenance is essential to keep industrial mixers in good shape. This is particularly important for mixers handling abrasive products, as they are more susceptible to damage and wear. Regular inspections, vessel thickness checks and cleaning are essential to avoid the presence of residues that can damage or wear out mixer components. This includes inspecting the mixer for signs of wear, (cracks, “waves” on the bowl, chips) and replacing worn components where necessary.
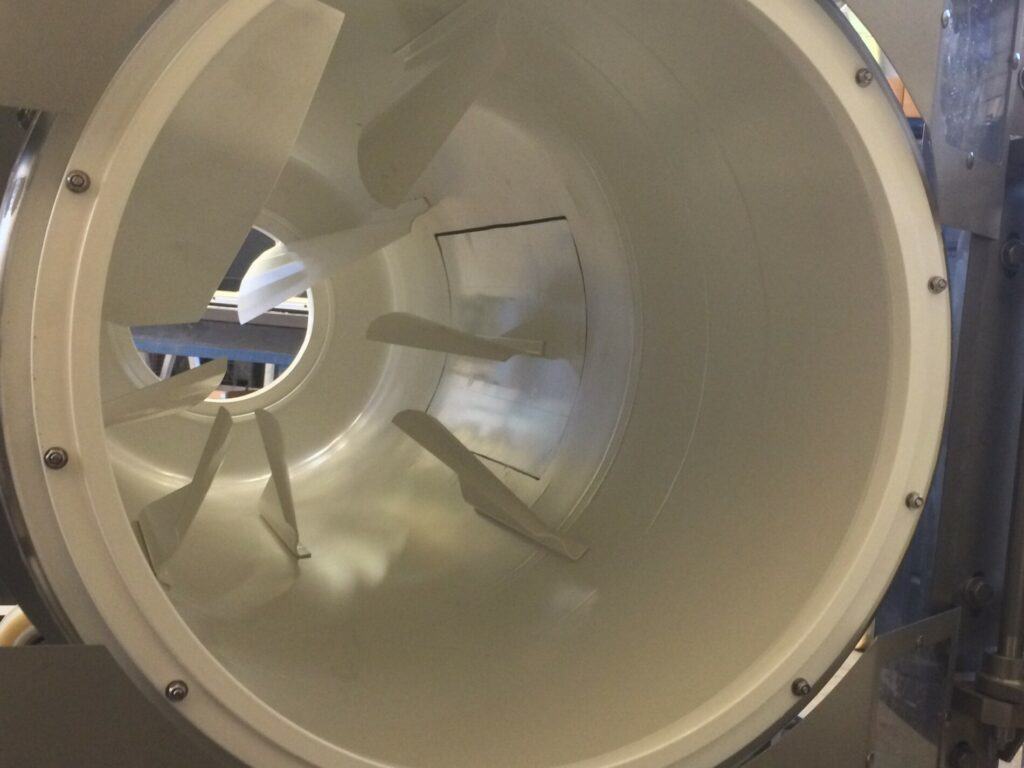
Shielding or anti-abrasion tank? What’s the right choice?
When it comes to protecting an industrial mixer, shielding, the use of anti-abrasion materials and hardfacing are popular options. Here are a few criteria to consider when choosing:
- Type of wear: Consider the type of wear the mixer will be subjected to. If the wear is primarily abrasive (caused by materials rubbing against the mixer), abrasion-resistant steel may be a good option. If the wear is caused by a combination of abrasion and impact, shielding may be a better choice.
- Wear severity: Consider the severity of wear to which the mixer will be subjected. If wear is light, a vessel made of abrasion-resistant steel may be sufficient. If the wear is heavy, the addition of a shield is necessary.
Product characteristics: the more abrasive the product, the greater the need for abrasion protection to ensure equipment longevity. Particle shape plays an important role in wear. Powder characterization will enable you to choose the right protection. - Production volumes: the higher the mixer’s production volumes, the more it will be called upon. In this case, tank armoring and tool reloading is a good option. If annual production volumes are low, abrasion-resistant materials will suffice.
- Budget: Budget is an important factor to consider. Shielding and hardfacing may be more expensive initially, but will considerably extend machine life and save money in the long term. Heavy-duty steel tanks will be less expensive initially, but require replacement of the entire tank once worn.
Ultimately, the choice between using abrasion-resistant steel, hardfacing and shielding will depend on the specific needs and requirements of your industrial mixer. Consult an expert in the field to determine which option is best suited to your particular situation.