The main four problems you should be aware of when selecting a magnet are:
- Blockages: fixed magnets restricting flow
- Coverage: limited coverage leaving some product only partially protected
- Retention efficiency: contaminants may escape the magnet and be re-introduced to the finished product
- Cleaning and maintenance: biohazards being introduced via dead zones or unsuitable design
Although all Magnattack® dairy-grade magnets are approved and safe for dairy applications, we wanted to outline the benefits of each, as well as the challenges you should expect.
Firstly, when choosing magnets for dairy applications, it is important to consider several factors:
- Is the magnet of sanitary design and build?
- Is it USDA-accepted?
- Is the cleaning process sanitary and simple to ensure least possible intrusion to the product zone?
- Can it be easily accessed for cleaning (if a manual-clean design)?
- In the case of difficult products (such as lactose) what means are taken to prevent build-up and binding of cleaning mechanisms?
- Is the magnet resistant to abrasion?
- Does the separator assembly consist of high-grade magnetics (such as RE80®) to ensure longevity and maintaining of magnet strength?
- What design criteria is in place to ensure effective magnetic separation is achieved without blockages?
- What means are taken to ensure magnet strength is maintained over time?
- Does the magnet comply with current HACCP and best practice standards (e.g., 0909MAGSEP 1-2010)?
- Is the magnet supplied with proper certification?
Having a magnetic separator that fits the above points is crucial when a sensitive product application is in question.
Let’s have a look into some of the Magnattack® dairy-grade magnet options:
Mag-Ram® Automatic Self-Cleaning Magnet
A self-cleaning separator that is best used in sensitive dairy applications on spray dryers or bulk powder packing. No ‘walking’ or ‘jamming’ when attempting to clean multiple bars simultaneously, as is the case with conventional designs attempting to coordinate two air cylinders to pull a bank of magnet bars through a common wiper.
The Mag-Ram® design permits the use of tight wiper seals which ensures the greatest versatility of control and that highly efficient magnet cleaning is achieved. The Mag-Ram® is also extremely hygienic, due to the absence of stainless-steel sleeves which inherently build up with unclean product residual.
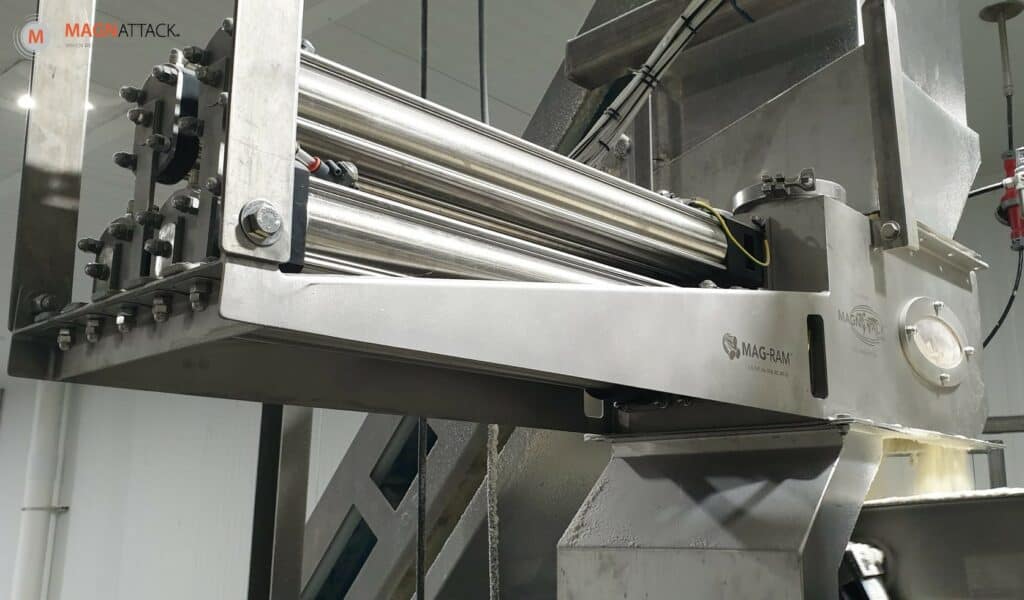
Rapidclean® Grate Magnet
The RE80® Rapidclean® Grate Magnet provides superior magnetic separation in dry food product lines. Designed to enable safe and effective manual cleaning with the ability to collect and analyse findings, the cleaning process is conducted outside of the product stream, greatly reducing recontamination risks, and allowing for visual inspection of bars.
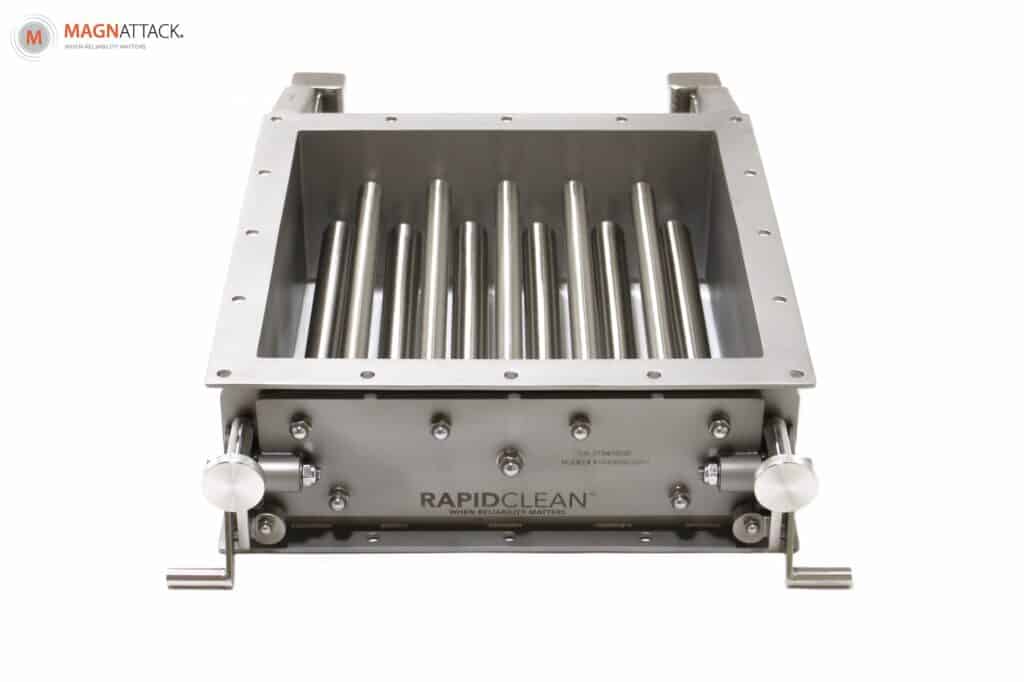
Emulsion & Slurry Pipeline Separator
The RE80®HT Emulsion & Slurry Pipeline Separator was engineered to achieve effective foreign metal fragment control and risk reduction in thick and viscous liquids, slurries, and emulsion lines. Acutex® Probe Magnets ensure minimal resistance to flow and smooth transition of product.
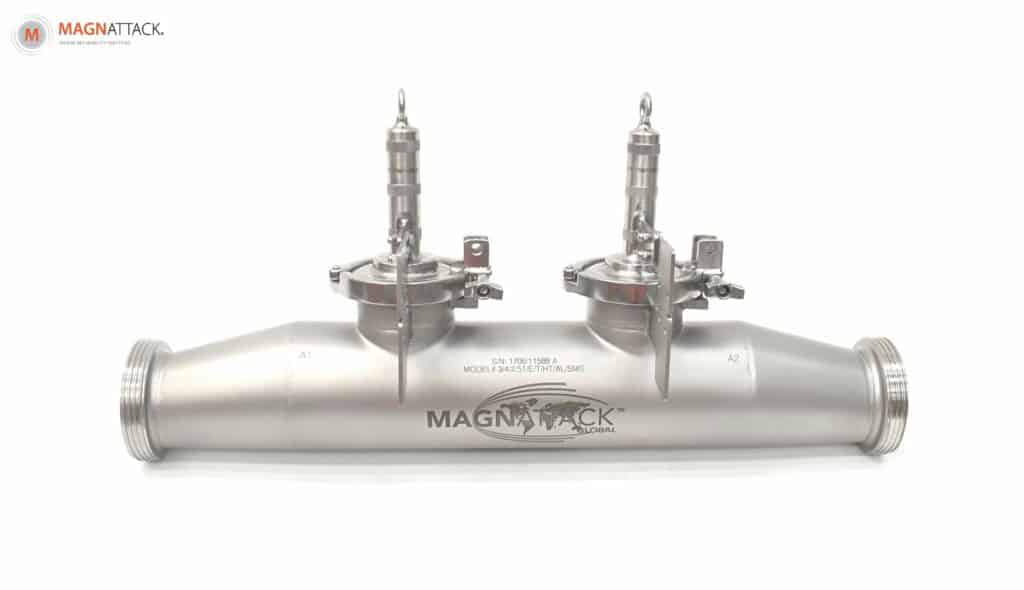
RE80®HT ACUTEX® PROBE MAGNETS
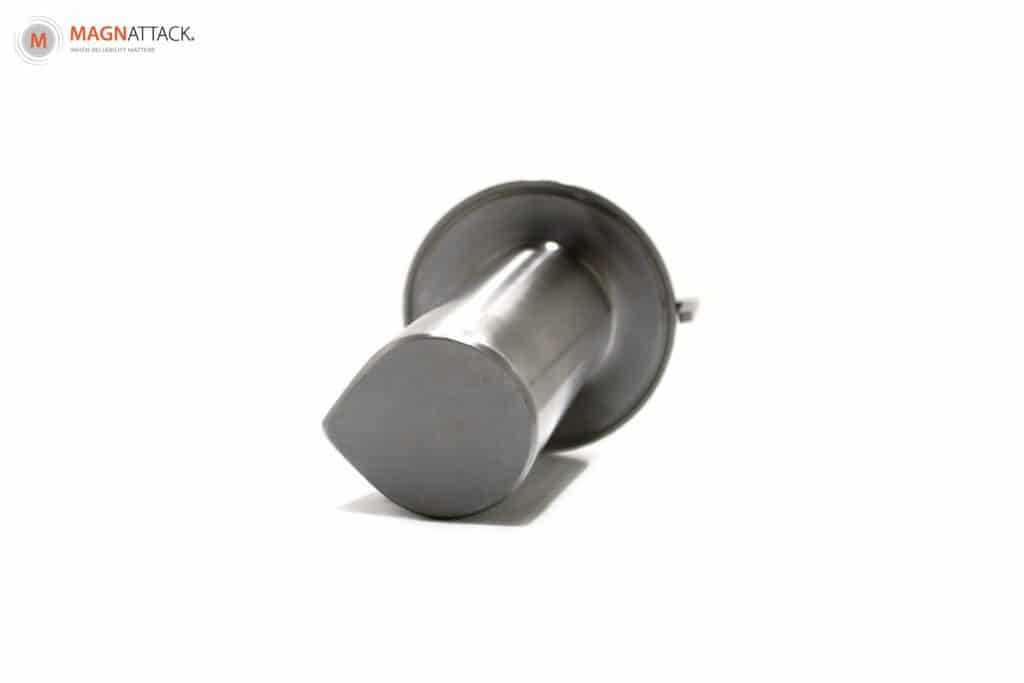
The Emulsion & Slurry Pipeline Separator features our powerful, high-intensity +11,000 Gauss Acutex® Probe Magnets. These patented Probe Magnets intercept the flow of product and extract metal fragments including work-hardened stainless steel and stone particles.
The distinctive lachrymiform (or teardrop) shape of the Acutex® Probe Magnets allow for very smooth transition of viscous products to move around the magnet with minimum resistance to flow. Maximum product to magnet coverage is achieved without causing leaks, blockages, and pressure problems.
The peak (or V-section) of the probe is faced towards the oncoming product stream, ensuring that collected magnetic fragments are washed to the back of the probe and safely retained until cleaning operations are underway. This feature greatly reduces the risk of recontamination caused by the impact of the product flow dislodging the collected fragments and reintroducing them back into the product stream.
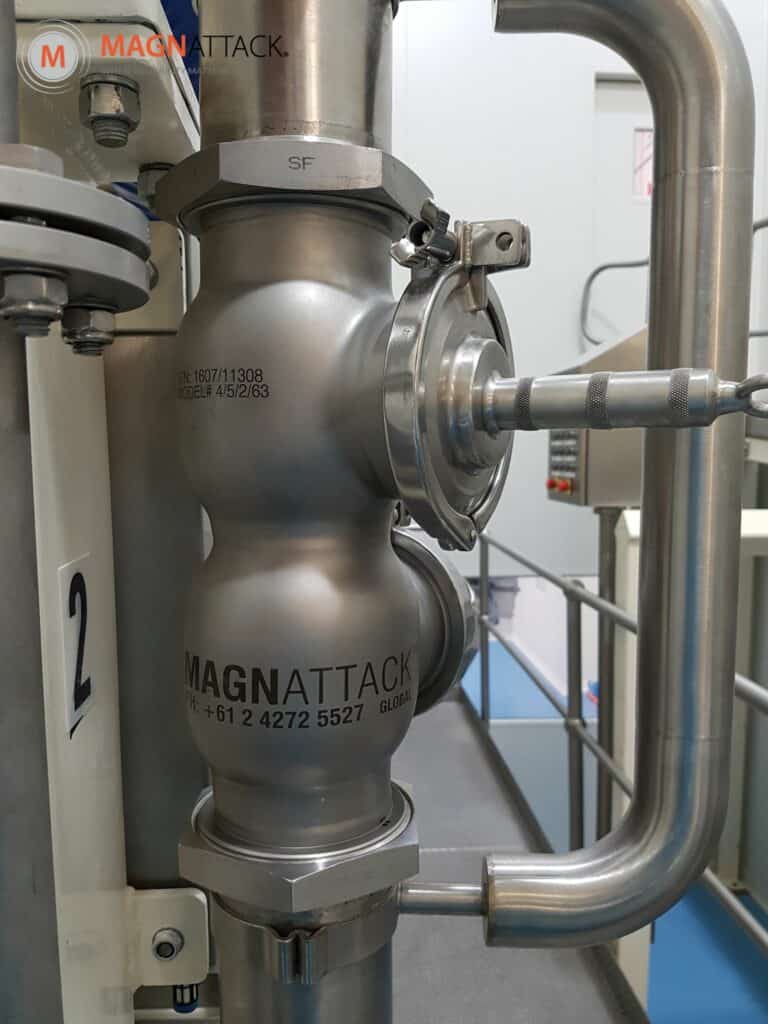
Powder Transfer Magnet
The Magnattack® Powder Transfer Magnet is a highly sanitary USDA Dairy-Accepted magnetic separator engineered specifically for sensitive powder transfer lines such as in dairy and pharmaceutical plants.
The Powder Transfer Magnet incorporates key design features of the Spherical Pneumatic Transfer Magnet, providing highly efficient separation of metal fragment contamination without experiencing bulk density or blockage problems.
The magnetic separator features high-intensity RE80® +11,000 gauss Acutex® Probe Magnets configured to remove weakly magnetic contamination and work-hardened stainless-steel fragments and stone, thus greatly increasing food safety control and product purity.
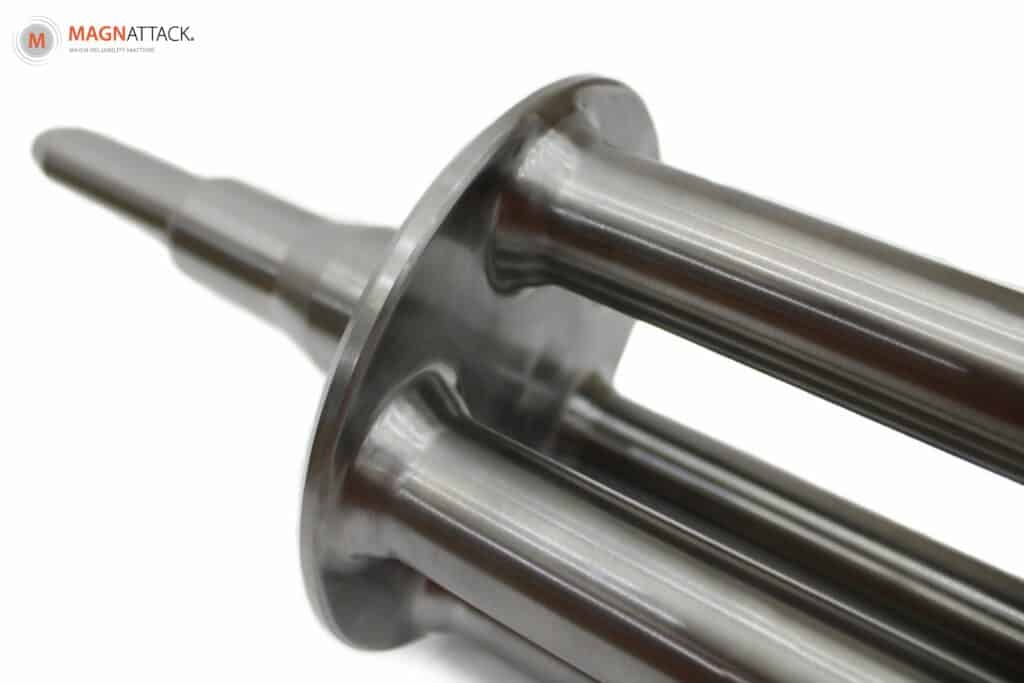
Rotary Powder Separator
Rotary Grate Magnets are designed to remove ferrous and magnetic particles from product flows that tend to plug and bridge in stationary magnetic grates. The Magnattack® rotary action prevents the product from bridging the process stream whilst breaking apart soft lumps and sticky materials. By using unique RE80® Bar Technology, the Magnattack® Rotary Magnet design also provides a superior product-to-magnet contact ratio in comparison to conventional grate magnets.