Rotary valves design types
Polimak offers numerous valve configurations depending on the characteristics of the handled bulk materials and the process, respectively. The fundamental valve components include a body (housing) with an inlet port and an outlet port, a rotor (shaft with blades), two end plates (outboard or inboard) and a drive system. Open-end or closed-end rotors with fixed or adjustable blades having at least six pockets are commonly used depending on the application. Our housings come with rectangular, square or circular inlet and outlet ports. Polimak valves are produced from various materials of construction such as cast iron, stainless steel and Hardox. Special coatings for abrasive bulk materials or highly polished finishes for food and dairy industries are available.
We manufacture standard and heavy-duty rotary valves for various industrial applications. Outboard bearing plates in which bearings are moved away from the head plates are generally used in heavy-duty models. These valves can be used to handle fly ash with varying temperatures as high as 300 C, fine dosing of lime and activated carbon, and many others. Their volumetric capability ranges from 0.4 – 663 L/Rev. To prevent contamination through the seals, air purge fittings are used.
Polimak produces the three general types of rotary valves, namely flow-through, blow-through and off-set, each suitable for various applications.
Flow-through
Flow-through valve types are also known as drop-through valves. The two ports, inlet and outlet, are vertically aligned and tend to be the same size. During operation, empty rotor pockets are filled by bulk solids flowing vertically down from upstream equipment, they are carried through and then vertically discharged at an outlet. Drop-through valves are widely used for non-cohesive and free-falling dry bulk materials like sand, wheat, rice, coffee beans and many others.
Blow-through
Blow-through valves have troughs that connect to pneumatic conveying lines, hence they are installed directly in a conveying line without any intermediate equipment. Bulk materials are supplied to a valve via an inlet, then a rotor turns and drops the bulk materials into the trough where the conveying air blows through emptying the rotor pocket and transports the materials directly into a supporting system. Blow-through valves are utilised for sticky and cohesive bulk solids flour, milk powder, custard etc.
Off-set
Off-set rotary valves are sometimes referred to as slide-entry valves. The inlet and outlet are offset from the valve’s housing vertical line. When a rotor rotates past a valve’s inlet, this offset permits an upcoming empty rotor pocket to only partially fill. Partial filling minimises bulk material shearing.
It also prevents jamming of a rotor caused by dry bulk particles trapped between the rotor and valve housing. The volumetric fill efficiency of an empty pocket is generally around 60%. It is used for bulk materials like sunflower seeds and peanuts.
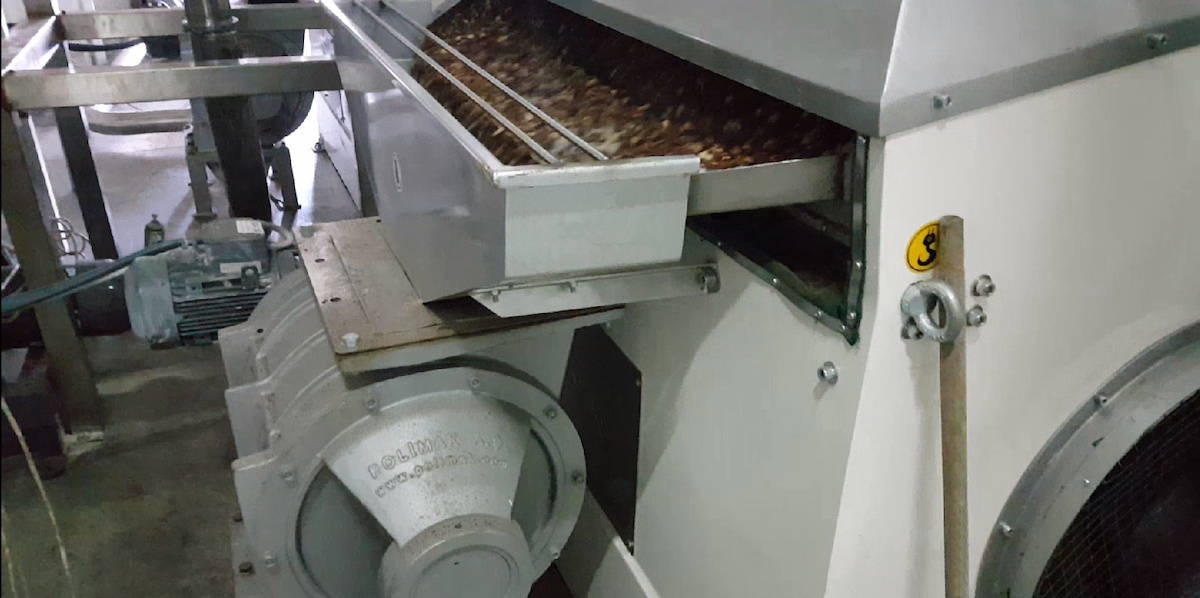
Rotary valves industrial applications
Simple in construction, rotary airlock valves are modifiable to fit most industrial applications. Our rotary valves are ideal for handling granular or powdered dry bulk solids. Some common applications for which rotary valves are utilised in industrial processes include:
Bulk solids discharge from silos
Rotary valves are widely used to discharge dry bulk solids from storage silos. They are mounted to the bottom of a silo cone to control bulk solids’ discharge.
Dust particles discharge from cyclones
Also known as a centrifugal collector, a cyclone is a dust collection equipment that separates particulates from the air by centrifugal force. It forces an incoming airstream to spin in a vortex. As the airstream is forced to alter direction, the particulates’ inertia drives them in the original direction and causes them to separate from the airstream. The main vortex curls downwards carrying coarse particles while the inner vortex generated at the bottom of a cyclone curls upwards carrying with it fine dust. The airlock valve discharges the coarse dust particles that settle at the bottom of the cyclone.
Dust particles discharge from Baghouse dust collectors
A reverse jet collector is commonly known as a pulse jet collector. A pulse jet collector makes use of bags held from a metal cage that is fastened to a tube sheet at the top of the collector. Dust enters the collector and its particles deposit on the outside of the bags. The deposits are cleaned by short periodic bursts of compressed air injected into the bags. These bursts cause flexing of the bags which result in dust particles breaking and falling of the bags. The particles settle at the bottom where they are discharged by an airlock valve. The airlock minimises the need for downtime in a process and reduces operator intervention.
Bulk solids processing equipment feeding and discharging
Most bulk industries require additional equipment for controlled feeding and discharging of the handled dry solids. Ball mills, pin mills, cone mills, hoppers, convey systems and many other pieces of equipment require a steady rate of material flow to operate effectively. Rotary valves can be used with such equipment to feed or discharge bulk materials in an effective and controlled manner.
Feeding pneumatic conveying systems
Rotary airlock feeders are utilised to feed dry bulk solids to conveying lines from upstream devices like storage silos or hoppers. They prevent air leakage and maintain constant feeding of dry bulk materials.
Handling large-sized bulk solids
Polimak manufactures rotary valves for smoothly handling large-sized dry bulk solids such as chickpeas, broad beans, hazelnuts. Our valves offer safe and efficient bulk handling with 0.1% harm guaranteed.
Our custom engineered production integrates defining the problem, conceptualisation, design, confirmation, production and installation. Polimak’s teams perform these steps efficiently and provide custom engineered solutions in a fairly short time.