Quicklime is produced by lime burning. The starting material is limestone, which occurs naturally in various forms and in large quantities, and which is thermally decomposed into quicklime (calcium dioxide) and carbon dioxide during the burning process. The result is a white powder, dusty, abrasive and corrosive on contact with water: quicklime.
In a lime plant in Germany, the quantity of quicklime produced after lime burning was to be recorded for better process control. The task was to integrate a scale that could cope with the typical properties of the bulk material, quicklime, directly into the existing conveying process with as little effort as possible.
After on-site consultation with MTS MessTechnik Sauerland GmbH, it quickly became clear that the use of an ImpactWeigh impact scale would be a suitable solution.
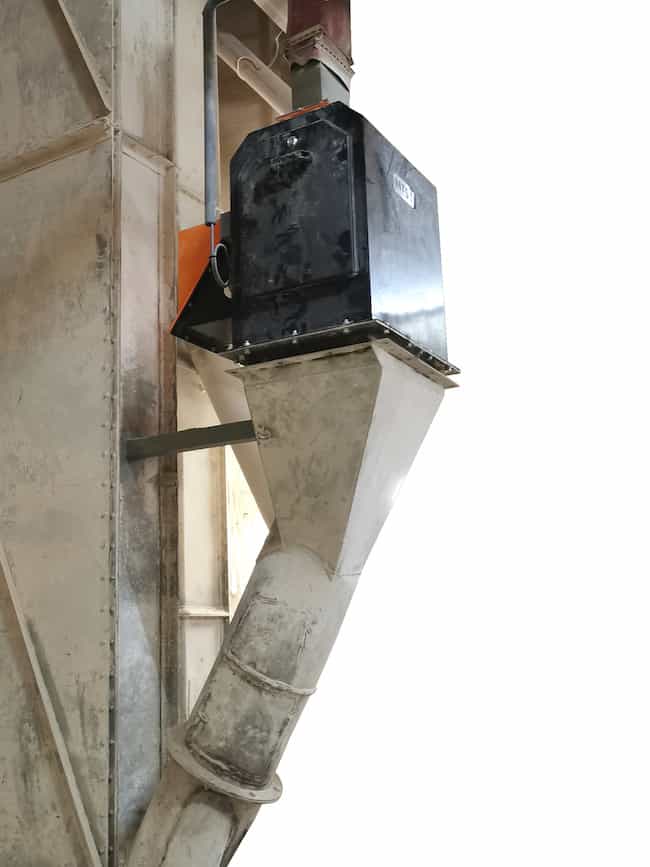
Impact scales weigh bulk materials in the vertical process flow through the scale, whereby the conveyed material hits the impact plate in free fall and the generated impact impulse is detected by a load cell. The ImpactWeigh impact scale weighs with a measuring error of max. +/- 1 to 2 % of the maximum flow rate. These scales are therefore a very good alternative to other weighing systems. Due to their compact dimensions and simple design, they are quick and easy to install, inexpensive and low-maintenance. However, for a good measuring accuracy, some requirements should be met for the use of an impact scale: a good flowing and homogeneous material to be conveyed that generates a sufficient impact impulse on the impact plate, a defined feed of the conveyed material to the scale and an installation of the scale free of vibrations or air currents.
In the application at the lime plant in North Rhine-Westphalia, the conveying process offered ideal conditions: the impact scale could be installed directly downstream of a screw conveyor, which ensures an uniform feed. The continuous flow rate of 25 t/h at a bulk density of 1 kg/l generates a sufficient impact impulse on the impact plate. This was equipped with an additional plate made of abrasion-resistant plastic (RhinoHyde), which is screwed onto the impact plate as wear protection and can thus also be easily replaced if required.
For easy and regular checking of the measuring accuracy, the ImpactWeigh was additionally equipped with a static adjustment device. This allows the operator to check without much effort whether the scale is still displaying the reference value determined during adjustment or whether readjustment is required.
Since its commissioning by an MTS service technician in February 2022, the ImpactWeigh impact scale has achieved reliable and accurate measuring results since.
The evaluation is carried out via the ModWeigh PPW basic control unit, whose performance parameters (resolution, filter, etc.) additionally support the measuring accuracy of the scale. The connection to the higher-level control system is made via Profinet.