In the end of the year 2020, Heilig Mixing Technology commissioned a V-Mix 28,000 PLW mixer with a useful volume of approximately 25,000 litres for a customer. All product contact parts of the mixer, such as the mixing screw, product outlet, cover and conical vessel are made of stainless steel. Remaining parts, such as the swinging arm, drive and bridge construction, are made of mild steel and covered with a multi-layer coating system. The mixer had to meet at least three customer requirements:
- Create a good, homogeneous mixture in a short time
- Ability to add liquids during the mixing process
- The parts of the mixer must be able to pass through a door and corridors.
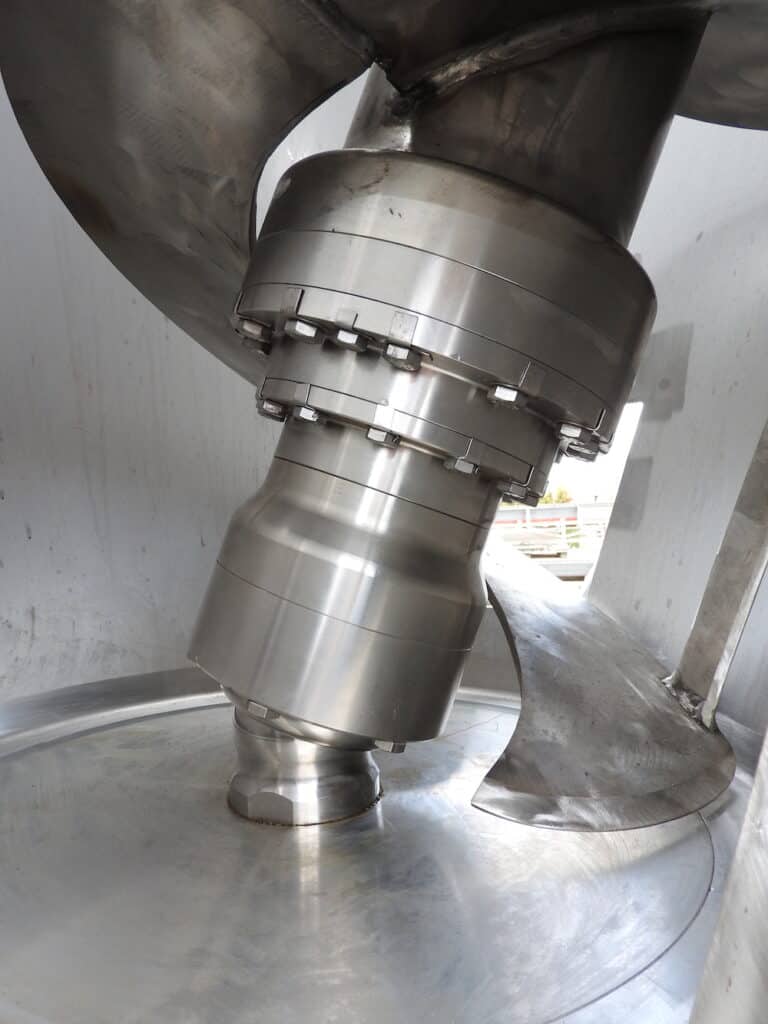
Limited time
The challenge was to mix a 25,000 litre batch homogeneously in just 12 minutes. Engineers from Heilig Mixing Technology have succeeded in making this possible, among other by increasing the diameter of the mixing screw to Ø600 mm. This does not compromise the very high mixing accuracy. The mixing process still takes place in a product-friendly and energy-efficient manner. A conical mixer consumes approximately 2 Watt/kg of product. This is only a fraction of the energy consumption of other mixer types such as a vertical ribbon mixer that consumes 20W/kg.
Adding liquids during operation
There are several options for adding liquid during the mixing process. One of them is injecting the liquid at fixed points, through orifices in the cover. A disadvantage of this manner is that the liquid, as the agitator moves in different positions, the liquid enters into the mixture directly. This can cause puddles and lumps in the mixture, as the liquid is not mixed directly into the product. Also, at the top of the vessel the swing arm will moves through the liquid jet, which can cause pollution of the swing arm, due to sticking product.
Adjustable nozzles
A much better method is to supply the liquid through one or more adjustable nozzles. In this case, the liquid will be added via a feed line through the drive of the mixer to a spray tube which is mounted directly below the swing arm. In this case the liquid can be applied evenly to the mixture via nozzles whose spray angle and spray direction are adjustable.
Dimension of parts
Since the conical mixer – with a diameter of 5.5 meters and a height of 7.55 meters – had to be installed inside of an existing building, engineers ensured that all parts were no wider than 3.0 meters. This made it possible to transport the different parts through a door and the corridors. For this reason, the mixing vessel had been divided twice horizontally and twice vertically.
Vessel
A challenge when mounting a mixer with vertical separated parts is keeping the vessel evenly round. A uniform diameter means a constant distance between the vessel wall and the mixing screw, which is essential for transportation of the product during the mixing process. A divergent distance diminishes the mixing accuracy.
Approval
After the completion of the production and the test run, the customer wanted to check the mixer in the Heilig factory in Heerhugowaard for quality and correct execution. The customer cancelled this due to the corona restrictions. He was satisfied with the assessment of detailed image and video material of the test run. This led to an approval on all points.
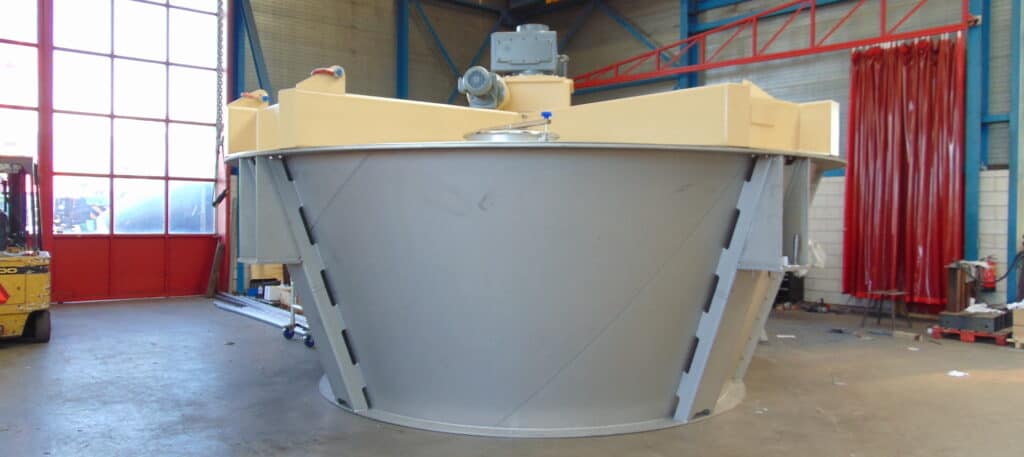
Commissioning
The V-Mix 28,000 PLW was then disassembled and prepared for transport. The assembly of the mixer at the location of the customer was carried out under the supervision of Heilig Mixing Technology and has been completed without any problems, after which the mixer was put into operation successfully.
Reliable in mixing technology
As a specialist in mixing technology, Heilig Mixing Technology can look back to more than 40 years of experience in the design, construction and installation of conical mixers. The delivery program not only includes a new silo-, conical-, vertical ribbon- and paddle mixers from 3 to 100,000 litres, but also fully or partially overhauled machines. The company from Heerhugowaard also is involved in the inspection, maintenance and optimization of mixers. A team of qualified and committed employees stands for core values, such as reliability and flexibility.
Why Heilig Mixing Technology:
- Short delivery times and immediate availability of spare parts from various mixer manufacturers
- Our own, modern production workshop
- Specialized staff with fully equipped service vehicles
- Process optimization, thinking along with the customer
- Complete solutions, from idea to implementation and maintenance.