It is selected as the process ‘gas of choice’ due to its excellent properties perfectly aligning it with the aforementioned uses.
Some basic facts about nitrogen;
- It makes up the majority of the air we breathe
- Colorless and odorless
- Does not support combustion
- Is non-oxidizing and in most cases non-reactive
- Does not support life (hence its use to keep food fresh – like in crisp packets)
- Boiling point of -196°C, and freezes at -210°C
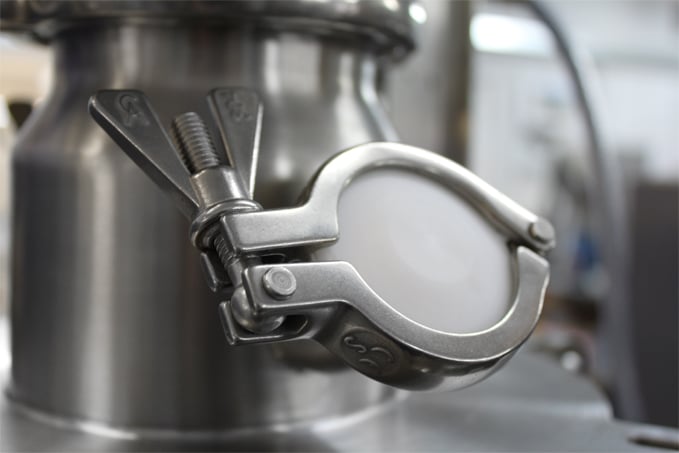
Inerting
Nitrogen generally does not support combustion by replacing the oxygen within a given space. With a potential liquid to gas expansion ratio of almost 1:700, it will quickly replace the air present within a given space.
For milling applications that require explosion protection (e.g. ATEX, Class and Division or IECEx), nitrogen is a commonly used method of inerting the milling zone to reduce the potential for an explosion. Size reducing materials will normally cause the material and mill contact parts (e.g. gearbox, screen, housing) to increase in temperature and, although very unlikely, there is always the potential for a spark from metal-to-metal contact. Note: the Hanningfield Under-Driven conical mill range has a factory-set gap between the screen and impeller, while the Over-Driven conical mill range is supplied with spacers, which ensure metal-to-metal contact does not occur.
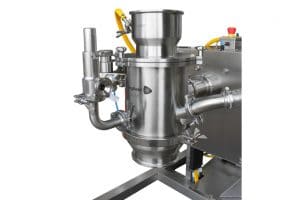
Nitrogen inerting adds an extra layer of protection to help eliminate all possible ignition sources. Typically, the inert gas is fed into the milling chamber via nitrogen ports at the desired pressure and volume. A variety of different components can be used in conjunction with nitrogen ports, such as temperature probes, oxygen analyzers, pressure relief (venting) valves, PLC logic controls, and pressure regulators; all used to help guarantee a safe and steady flow of nitrogen into the mill. The goal is to maintain safe oxygen levels within the milling system.
Product Integrity
Nitrogen is often used to help preserve food and protect materials that may degrade when in contact with oxygen. As such, entire processes may be blanketed with nitrogen to protect the material throughout until it is eventually packed. Flushing the packaging in so-called MAP modified atmospheric packaging equipment is now commonplace.
In milling applications, it is common to use an oxygen analyzer (see photo below) to measure the level of oxygen within the milling chamber. Once the oxygen drops to an acceptably low level, the material can be charged for milling. For critical applications, the level of oxygen can be controlled by continuously monitoring oxygen levels in the milling system and modulating the ingress of nitrogen to maintain the prescribed level. This is accomplished through process automation.
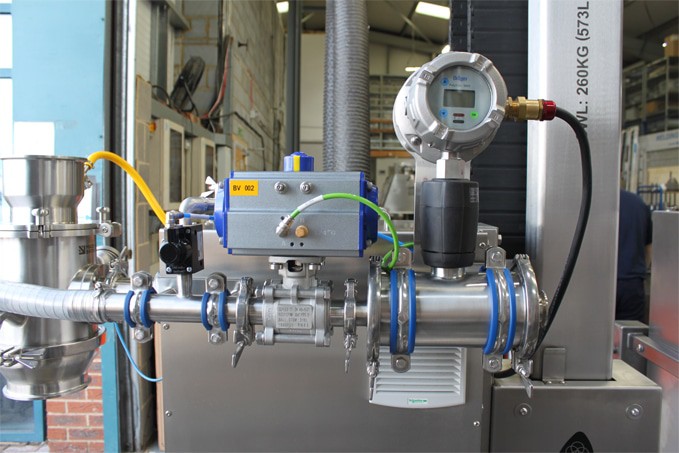
Cryogenics
Nitrogen is the most used and ideal gas for cryogenic freezing of material before milling. It remains as a gas until -196°C, enabling the user to supply a constant flow of extremely cold gas to freeze materials before milling.
Materials with a high-fat content such as plant matter are excellent examples where nitrogen can greatly improve the milling operation. This works by bringing the material far below the temperature where it may melt or release oils. This occurs by embrittling products that are waxy by freezing materials with high moisture or fat/oil content.
Cryogenic milling is widely employed within the pharmaceutical cannabis industry, where cannabis exhibits many material properties which can be challenging during size reduction (e.g. moisture content, oil/resin content, and fibrosity). In cannabis milling applications it is common to inject nitrogen in its liquid form directly into the mill to reduce the heat of grinding. However, in some circumstances, ‘nitrogen bathing’ the material before milling using specialized cryogenic feeding equipment is required. This is due to the size of the infeed material, where direct exposure with liquid nitrogen for a specific time allows for complete chilling or embrittlement of the process material.
Cryogenic freezing material can also help to protect material that degrades when it is exposed to heat increase due to the friction of milling. Materials containing proteins may often be processed using nitrogen to prevent the fat, oil, and protein denaturing when exposed to the heat of milling. The loss of essential oils such as in expensive spices and medicinal herbs can be minimized during the milling process with the utilization of liquid nitrogen.