Research into new anode and cathode chemistries will focus on improving battery life, durability, safety, compactness, energy density, affordability and wireless charging.
So where does ‘Mixing’ technology fit in?
Winkworth Machinery is a world leader in mixing technology and can provide a variety of mixing solutions that can be and have been used in the development and production of lithium-ion and other newly developed processes for the future battery market.
We are experts in mixing and blending, which is important when working with such a diverse range of raw materials, particle sizes, textures, and even external properties (heating, drying, vacuum).
Each battery manufacturer develops its material differently due to their specific objectives. Consequently, creating new battery chemistry presents many challenges. They include high battery control and compliance, cross-contamination prevention, adjustable flow rates for cohesive or very loose powders, keeping humidity low and controlling operating temperatures.
The anode (positive), the cathode (negative), and the electrolyte solution are a battery’s three common constituent parts. Pushing a flashlight button, for instance, causes current to flow from the negative terminal to the positive terminal via the battery and bulb. The reason for this is that the battery is made up of chemicals that facilitate the transfer of electrons from the negative to the positive terminal. Additionally, an electrolyte solution is present, which facilitates the transfer of sodium ions (Na+) from the negative to the positive terminals. As long as the battery has stored energy, electricity will keep flowing through the cell. The chemical reaction that occurs inside the cell controls the chemistry of a battery. Lead acid, nickel cadmium, lithium-ion, and zinc air batteries are the four most common chemicals used in modern batteries. Each battery’s chemistry produces a unique set of characteristics.
Battery production demands stringent and complex methods and technologies. Electrode manufacturing is crucial for battery cathode and anode production. And the crucial stage is often mixing.
Mixing
Mixed formulations might be powders or liquids, but some technologies require both. Each technology depends on understanding essential parameters and choosing the most effective mixing approach to achieve homogeneity, repeatability and quality end products for the next stage in battery manufacturing. Manufacturing high-quality batteries starts with choosing the right electrode slurries, mixing devices, and procedures. Formulations may exhibit shear-thinning, time-dependent, and pseudo-plastic semi-flow features. Equipment that applies high shear stress may have to be avoided since the anode active materials may have a fragile crystal structure.
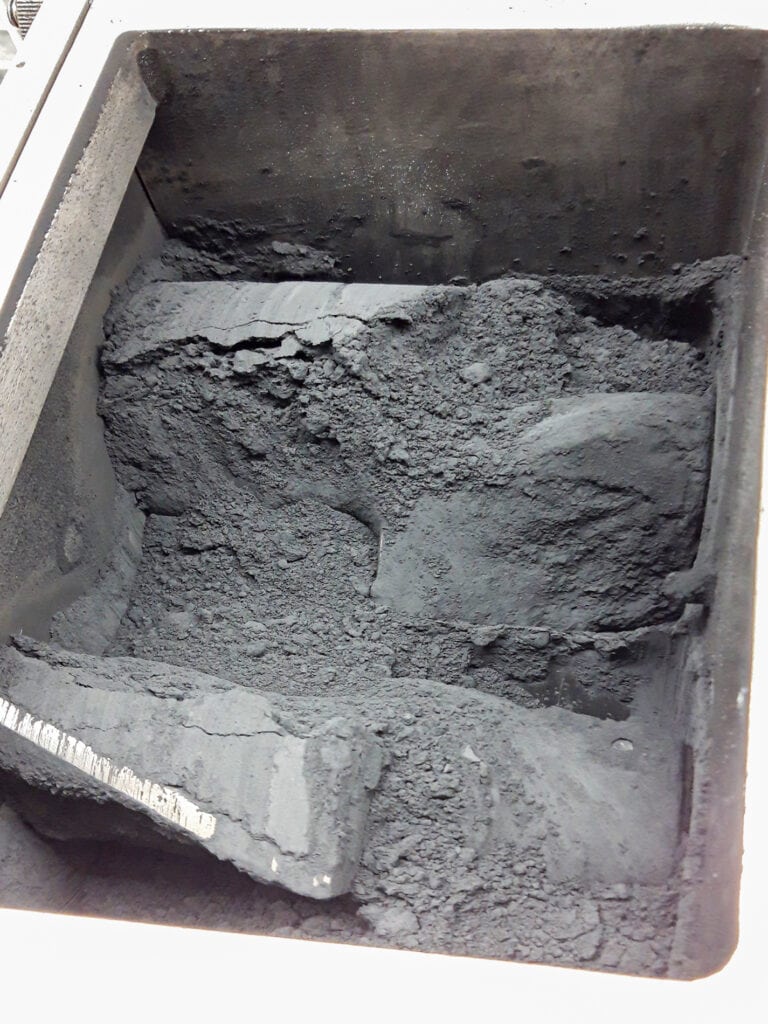
Binders may be introduced to improve adhesion between active material particles during mixing. It should be stable enough to retain its adhesive quality even when exposed to an electrolyte or oxidation-reduction reaction. Binder materials should be evenly distributed, have strong adhesion, solubility in industrial solvents, electrochemical inertness, and resistance to most chemicals.
A battery’s anode and cathode cells often appear identical and are produced using similar, if not the same, machinery, but preventing cross-contamination between the two is crucial. Therefore, anode and cathode components are often processed independently.
Particle-size distribution can impact mixing and electrode quality. Oversized or undersized particles can create dust, so they must be removed. Additionally, more point contacts in active materials can create more holes, reducing battery capacity. The electrode’s conductivity can be improved by adding conductive additives to plug those holes. Lithium battery anode and cathode surfaces need to be uniformly coated to give good stability. Consistency, cycle life, and safety define its importance to all batteries.
There are many reasons why some of the world’s leading battery manufacturers have chosen to work with Winkworth Machinery for their design, development, and production processes, including tried and tested technology with mixing experience dating back to the 1930’s.
Winkworth Machinery has a long history of working with companies in the battery industry, and our products are in use all over the world. We will assist in ensuring you meet your mixing needs from consultation to design, manufacture and installation. At our fully-equipped onsite mixing test centre, we can often replicate the challenges of your manufacturing process to provide an accurate assessment of how our equipment will perform. This allows us to offer a tailored solution for your specific objectives.
Conclusion
New battery R&D and production are accelerating and are crucial to our efforts for a greener planet. The production of low-cost, high-integrity components is driving this technology. Mixing advancements can boost battery manufacturing. Work with a solution provider like Winkworth Machinery who understands the challenges and is willing to innovate and contribute to overcoming them.