Soda ash production, however, has traditionally suffered from inadequate cooling methods that, among other challenges, require high volumes of air and come with steep energy requirements.
“The quantities of the air we’re talking about is at a scale that requires significant air-handling systems that incorporate large fans and extensive ducting,” says Albert Bedell, Regional Director, Asia Pacific for Solex Thermal Science, adding these take up significant space, draw heavily on plants’ power systems and have the added obstacle of dealing with dust control.
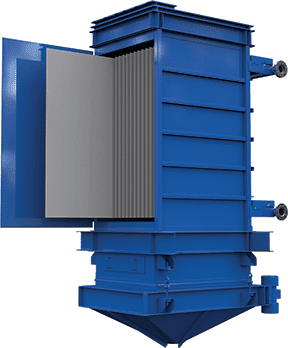
Increased adoption of indirect cooling alternatives in the form of plate-based vertical heat exchange technology is offering soda ash producers a turnkey solution to many of the challenges the industry has long just accepted, says Bedell.
“In addition to low energy costs, indirect cooling technology offers the advantages of improved product quality, no emissions, and more,” he says. “In short, it’s a simple, lean, and more efficient means of cooling bulk solids such as soda ash.”
But first … a bit more about soda ash
Also known as sodium carbonate – and not to be confused with the sodium bicarbonate found in many classroom volcano experiments – soda ash can be separated into two different grades: light and dense.
- Light soda ash is a fine, crystalline powder that looks like table salt or baking soda. It’s a key ingredient in products such as detergent, soap and paper.
- Dense soda ash, meanwhile, is chemically identical but presents as small granules. It’s what’s used in the production of flat glass and glass containers – for example, reducing the melting temperature of the sand used in glass production, or helping shape glass articles.
The majority of soda ash produced in the world is used in the production of glass for the construction industry.
Soda ash can be mined from natural deposits and purified or, more commonly, synthesized using the Solvay or Hou’s processes. Regardless of the upstream process or source of the material, the material is calcined in large rotary kilns. Because of the high temperature (e.g. upward of 150°C) required in the calcining process, soda ash needs to be cooled to ensure the safety and operability of the subsequent packaging and transportation process.
The need for cooling
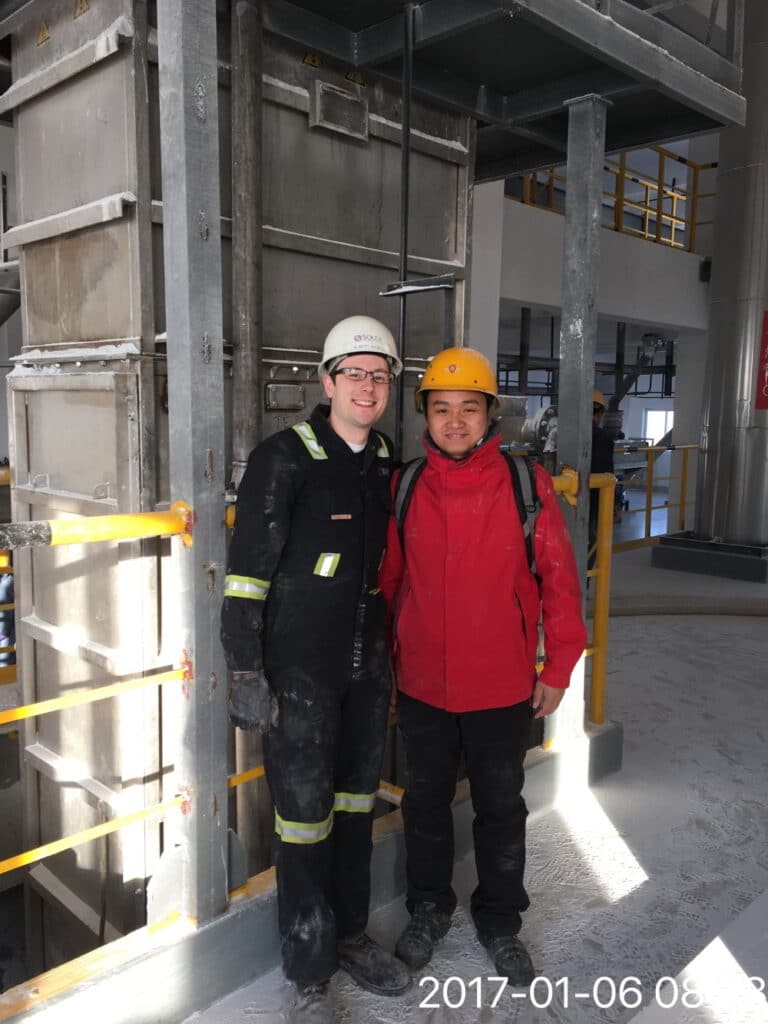
“This cooling stage has typically been accomplished through direct-contact solutions such as rotary drums, fixed or fluidized beds, and paddle or air-conveying coolers,” says Zhang Houqing, Deputy General Manager with Chemequip Industries, a partner with Solex that has been active in the Chinese soda ash market for 11 years.
“While these direct heat transfer systems have been in place for decades, they are proving to be an inefficient use of resources, with high energy consumption.”
For example, direct air-cooled units require a large amount of air required to achieve sufficient cooling. In the case of a typical 30 tph soda ash cooler, that could range from 30,000 to 50,000 m3/h of air to enable the cooling process.
With indirect cooling technology, the soda ash flows by gravity between vertically orientated stainless-steel plates, while a heat transfer fluid (e.g. cold water) flows counter-current through the plate’s internal channels.
The configuration only requires a small amount of air for condensation management as the soda ash is cooled, thereby eliminating the need for sophisticated air handling and cleaning systems. It’s estimated the energy consumption of indirect cooling technology is up to 90% less than direct-contact alternatives.
“And because air flow is typically minimal, dust emissions are low,” says Zhang.
Bedell notes that Solex has been involved in the soda ash industry since 1995 when a producer in Turkey began using indirect cooling technology in the production of heavy soda ash.
“Since that first installation, our equipment has been installed in dozens of facilities worldwide, processing both natural and synthetic soda ash,” he says, noting the current global installed capacity of Solex coolers in the soda ash industry is more than 11 million tons per year.
Chemequip, meanwhile, is deeply entrenched within China’s soda ash industry, with a market penetration above 60%, says Zhang. He notes the company is currently working on further innovation within the soda ash production process in the form of heavy ash crystallizers, distillation tower ammonia condensers and carbonization tower external cooling crystallizers.
“By collectively drawing on the experience learned through our combined successful installations, both Chemequip and Solex can provide a highly reliable, efficient and economical cooling solutions to soda ash producers worldwide,” says Zhang.