The brief was to provide a system to accurately dose aluminium can lids from a bulk bag source into the downstream process line at varying rates from 20 – 80Kg/hour. The can lids have a higher level of non-aluminium material and must therefore be dosed into the recycling line at a specific rate in relation to the downstream process.
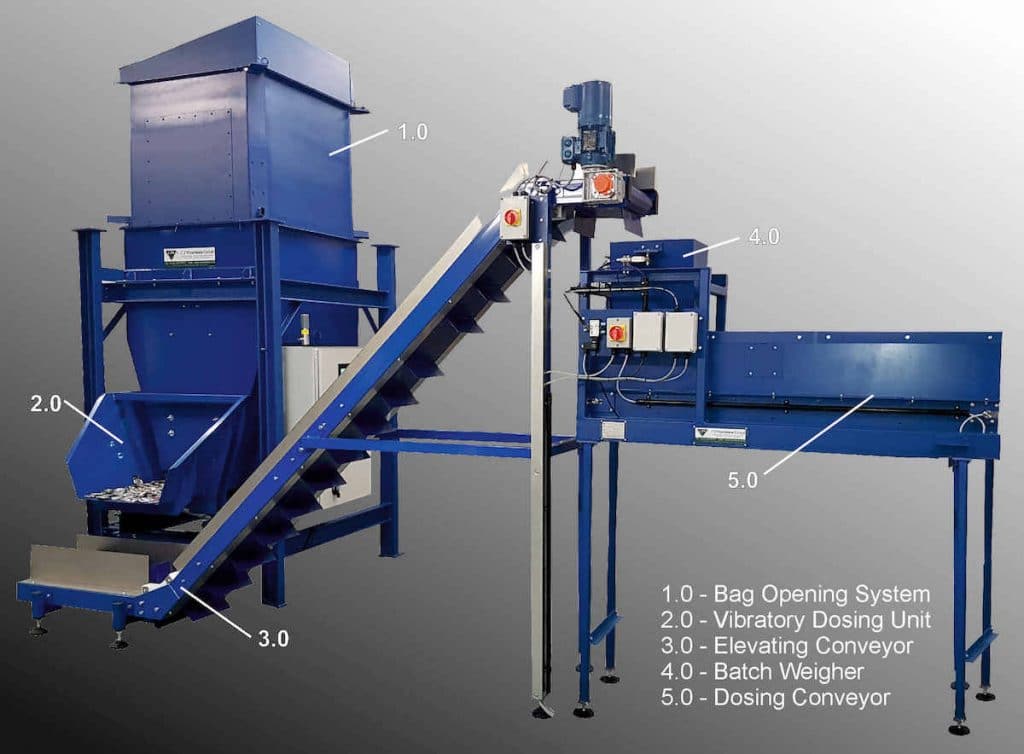
In addition to this the line can only operate for a specific time period before a pre-determined shut-down period is initiated to reduce the potential levels of fumes given off by the non-aluminium recycling process.
The system developed by CJ Waterhouse is composed of a number of constituent component machines which work together to discharge the bulk bag, separate the can lids out and provide a controlled, known weight feed to the downstream process.
These individual machine components combine to provide an integrated turn-key solution to the customers specific requirement and are detailed in the following sections:
1.0 Bulk Bag opening System
The bulk bag opening system is designed to accept 1M3 FIBC bags, loaded via the electric hoist system. Internally the system houses a bespoke multi-blade cutting assembly with a central piercing cone which penetrates the base of the bag and produces 4 diagonal cuts from the centre to the corners. This cutting operation is performed under the bag weight alone and allows complete discharge of the bag contents to the hopper below. All blades and piercing cone are removable for sharpening and replacement.
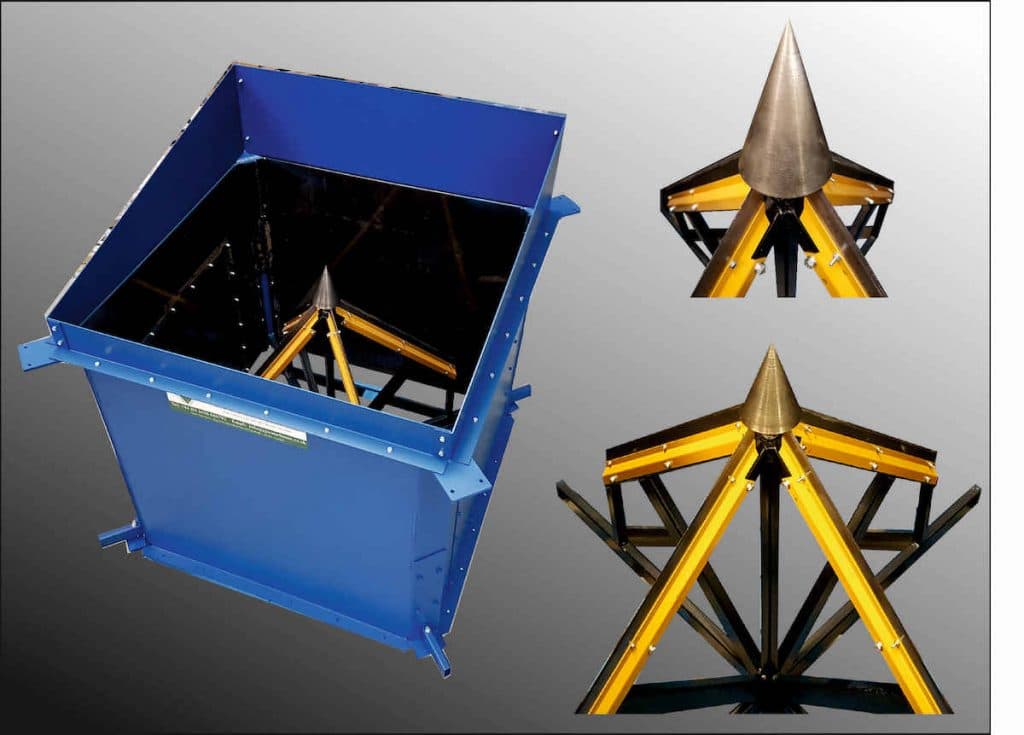
2.0 Vibratory dosing unit
The vibratory dosing unit resides beneath the bag opening section and is designed to provide a controlled feed of bulk materials to the downstream elevating conveyor. The unit is supplied complete with variable speed control which varies the vibration amplitude and hence the speed of material transfer. It is the speed control at this point which ultimately dictates the overall throughput of the system at its output. The feeding device is also fitted with a stream depth regulator plate to adjust the depth of material travelling over the feed trough and eliminate potential material over-run.
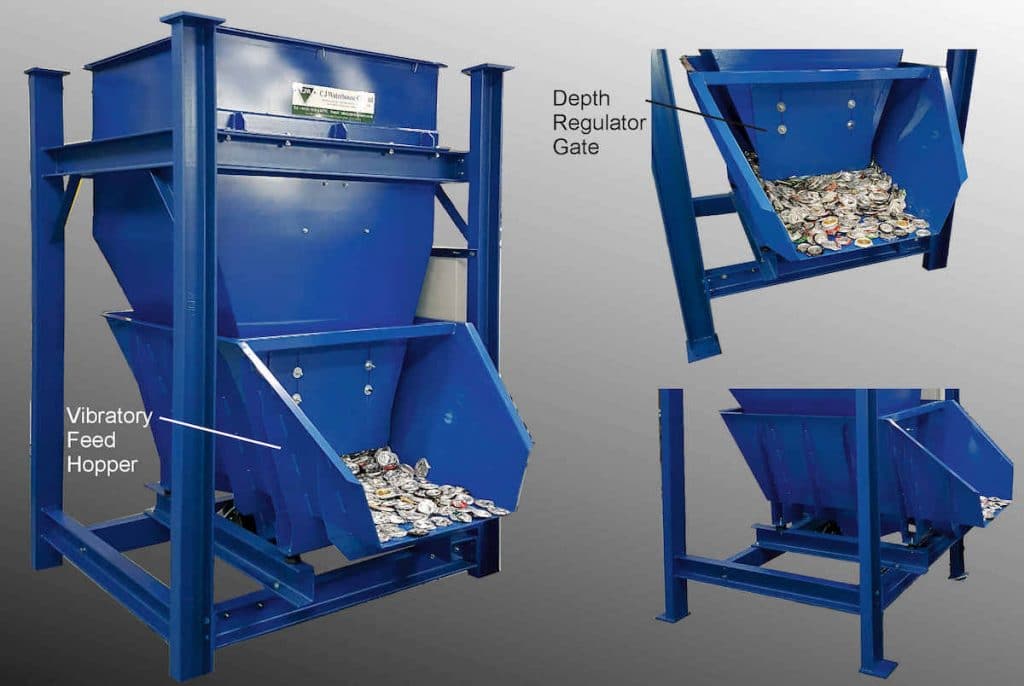
3.0 Elevating separation conveyor
The elevating conveyor collects its material directly from the discharge point of the vibratory hopper and is designed to feed it to the batch weigher at a controlled rate. The conveyor has a high flighted plastic belt and side walls to prevent spillage and slippage of the can lids back down the conveyor. The operation of the conveyor is controlled by the downstream weighed and only runs when the weigher requires additional material.
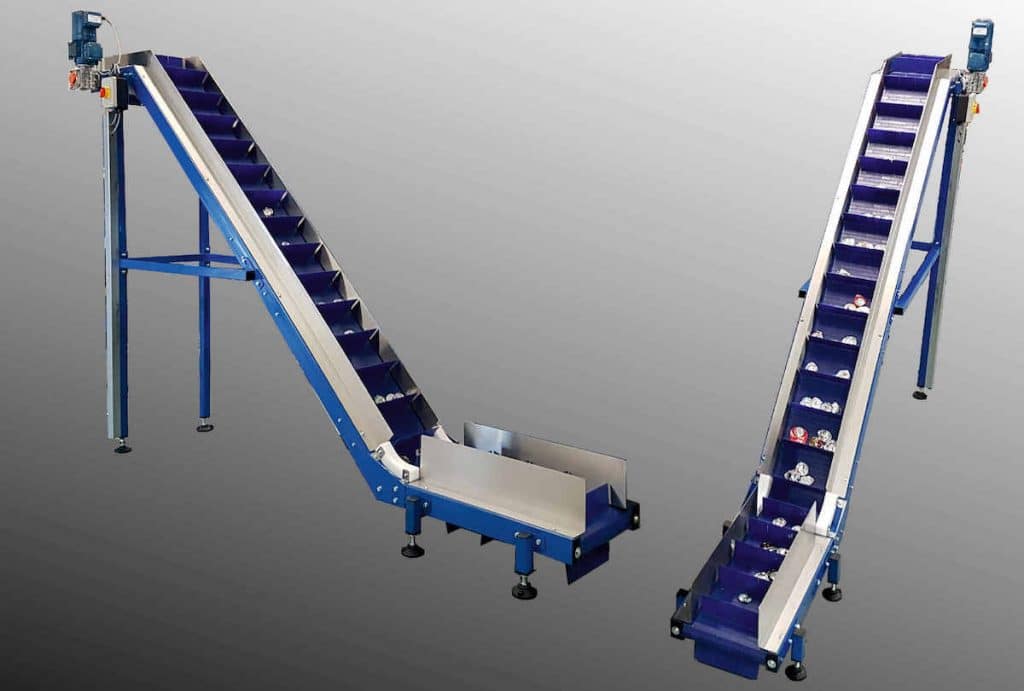
4/5 Batch weigher & Dosing Conveyor
The batch weigher and dosing conveyor form a single combined unit where the weighed discharges its batch directly onto the conveyor belt beneath. The weigher is a dual loadcell batch weigher with twin bomb door discharge gates. A pre-determined amount of material is fed into the weigher from the elevating conveyor, the discharge gates then open and the
material falls onto the dosing conveyor belt below. The dosing conveyor then moves this product away from the weigher drop area ready for the next batch to be dropped. In this way a continuous output of material at a known rate is achieved.
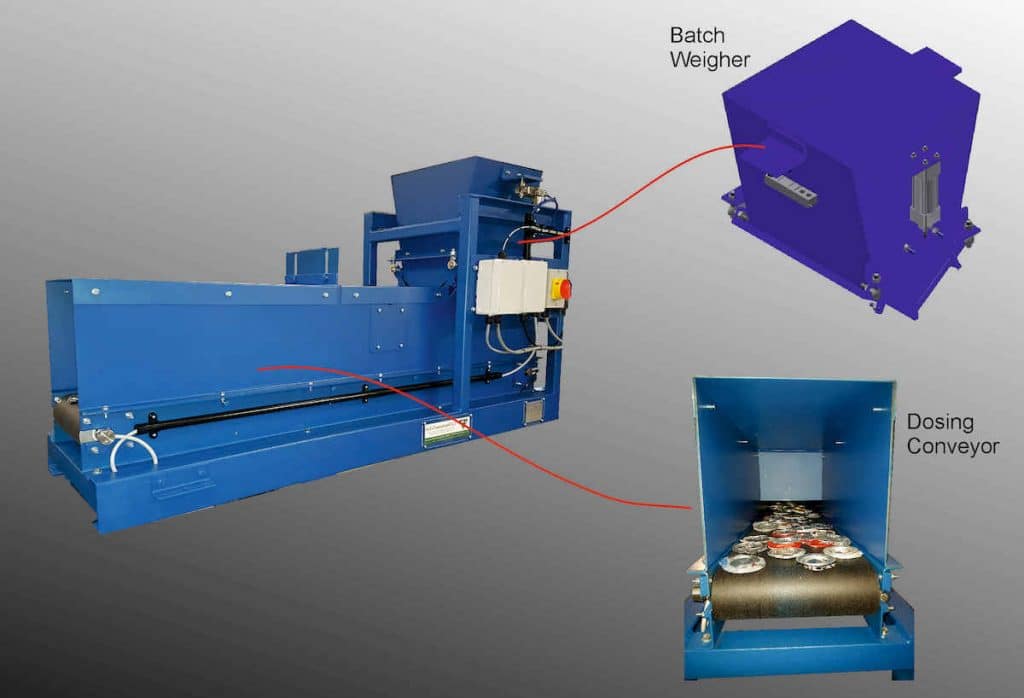
Control
The machine mounted control panel houses a block PLC which provides sequence control of the can lid dosing system. The panel also incorporates a door mounted HMI unit providing a graphical representation of the system together with numerous data presentation, set up and configuration pages.
The system provides automated throughput and speed control in relation to the required rate set by the operator on the system set-up page. As the system runs it constantly monitors the totalised throughput of the weigher against time and cross references it against the required throughput. Speed alterations are performed by the PLC as a direct result of the feed back
data from the weigher.
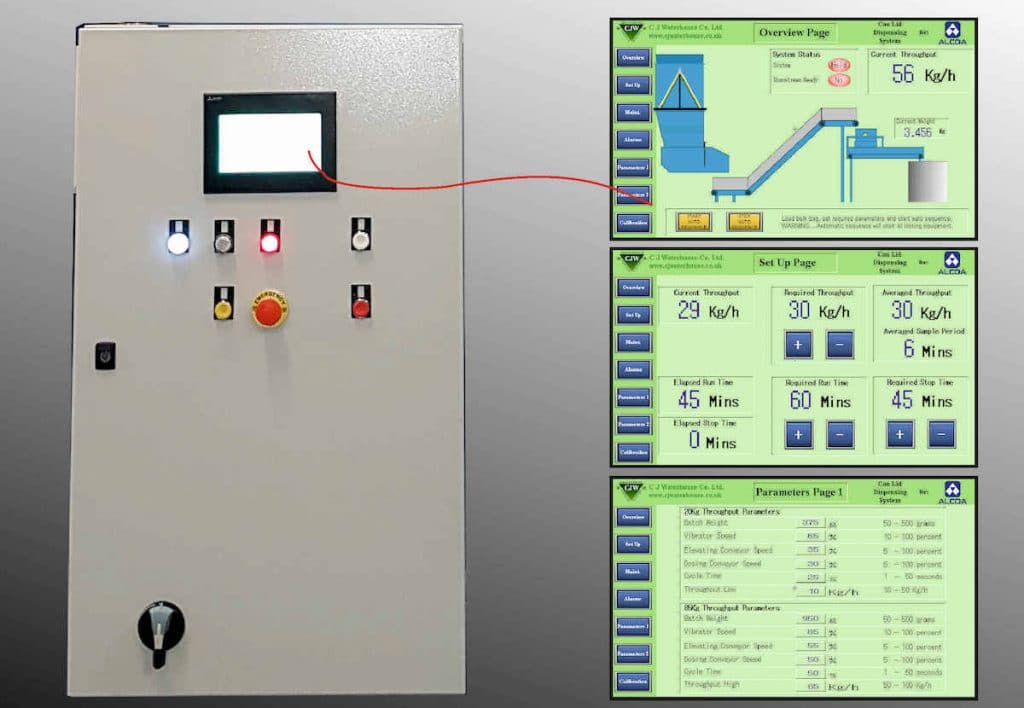