Using high pressure water or solvent to clean storage containers, IBCs or tanks on the tank trucks is a common process in the chemical / petrochemical industry. Between the loadings of two different products, the tanks must be cleaned thoroughly to avoid contamination. For transport of petroleum products, to prevent the so called switch loading, the tank trucks should be cleaned before a new load, if the previous product loaded had a lower flash point (e.g. gasoline) than the new loading (e.g. diesel or kerosene). To achieve the best cleaning result, high pressure washing nozzles are widely applied. When the washing jet impinges on the tank wall, it forms a mist of fine droplets. The combination of water droplets, vapor of flammable chemical or petroleum products and air forms an unpreventable explosive atmosphere. How dangerous could it be during the cleaning of tanks?
Static electricity – often neglected potential risk
Where does the static electricity during the tank cleaning process come from? The remaining products from the last loading can be easily drifted by the cleaning water. As a result, the relative movement of their molecules during the application of the water jet will lead to electrostatic charging. The charged mist produces high electrical potentials and the maximum value, which occurs in the center of the tank, depends mainly on the size of the tank and the charge density of the mist. If isolated conductors were present in the tank, incendive sparks could occur at much lower potentials. Isolated conductors are inevitably formed when washing with liquid jets from high-throughput nozzles because these produce large isolated liquid volumes as the jet breaks up. If the electrostatic charges generated during the cleaning process cannot be dissipated in time, the accumulated charges can easily ignite the vapor / air mixture in the tank. Theoretically, spark discharge can be easily avoided by simply grounding all conductive parts. However, experience shows that the safe grounding of all conductive parts in practice is not always that easy to ensure. This applies in particular to mobile objects which have to be grounded again and again by the staff, such as tank trucks or containers. How to ensure a reliable and effective grounding of them?
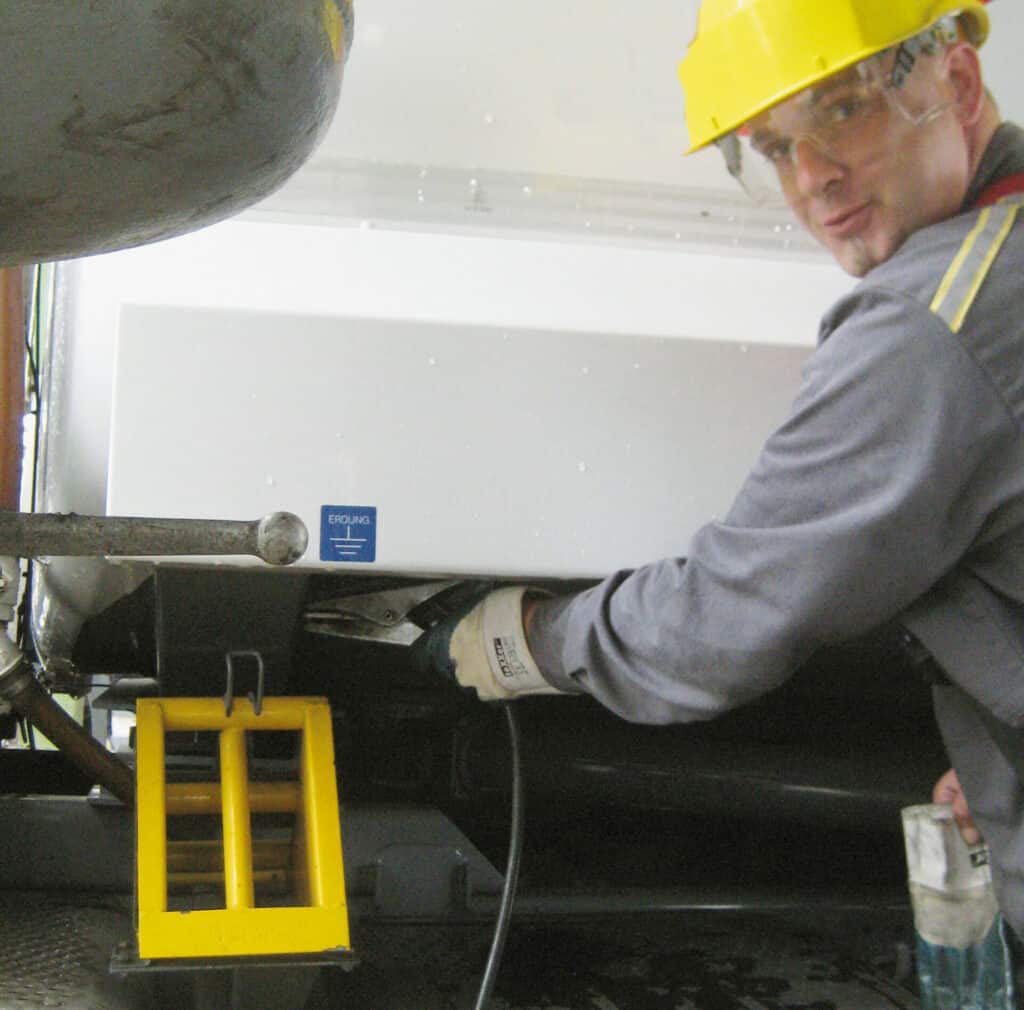
Reliable grounding monitoring system for tank cleaning stations
According to the IEC TS 60079-32-1: a grounding cable should be connected to the truck before any operation is carried out. And to ensure the grounding of objects, TRGS recommends a ground monitoring system (interlock equipment) that blocks the operation process when the grounding cable is not connected or not working appropriately.[1] It is further recommended by IEC TS 60079-32-1 that the system should be capable of differentiating between the truck and other metal objects. This type of system can prevent operators from connecting the grounding system to objects that may be electrically isolated from the truck’s container.[2] The main difference between the tank trucks and the metallic objects are their electrical properties. The electrical characteristic of tank trucks are not only resistive. A typical tank truck nowadays has an electrical capacity and resistance. To fulfill the recommendation from the IEC TS 60079-32-1, the grounding device should be able to measure the impedance of the object. It should be capable to distinguish between proper truck grounding and metallic parts on the gantry. It should also be able to identify the grounding connection when the operator connects the system to the insulated part on the truck. Most cleaning stations do not only clean tank trucks, but also tank containers or IBCs. Unlike tank trucks, tank containers must be moved by a chassis into the washing position. The chassis is made of steel and thus conductive. When using a grounding device according to IEC TS 60079-32-1, there will be difficulties to recognize other objects than tank trucks and give a release signal to start the cleaning process.
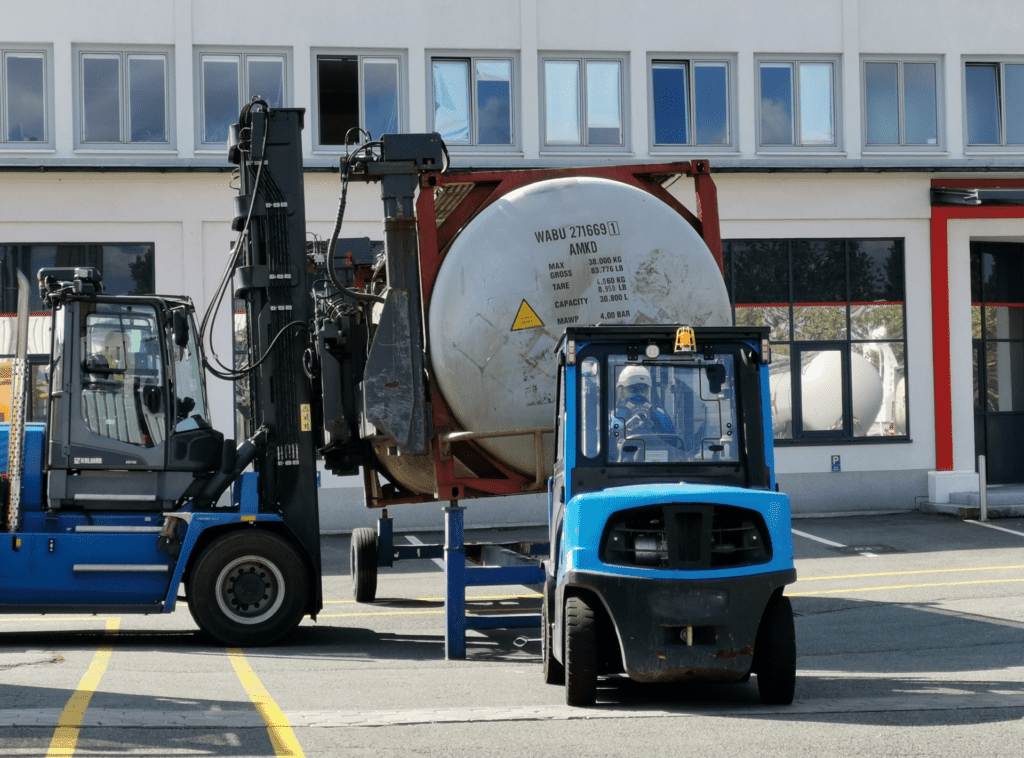
Case Study: A cleaning station in Northern Germany
The cleaning station is located in Northern Germany, with two washing lines for tank trucks and tank containers. Both lines are equipped with grounding devices with tank truck recognition functions to prevent static electricity hazards. As more and more tank containers need to be cleaned in the station, the operators were facing a difficult situation. The grounding devices with truck recognition ensure the grounding connection on the tank trucks, but encounter problems to recognize containers. The devices identify tank containers on a chassis as simple metallic parts on the gantry, due to the material of the chassis and the conductive ground in the cleaning station. As a result, the workers are not able to get release signals from the grounding devices. Therefore, they need to ask their director from time to time for a bypass confirmation to get water for starting the cleaning process.
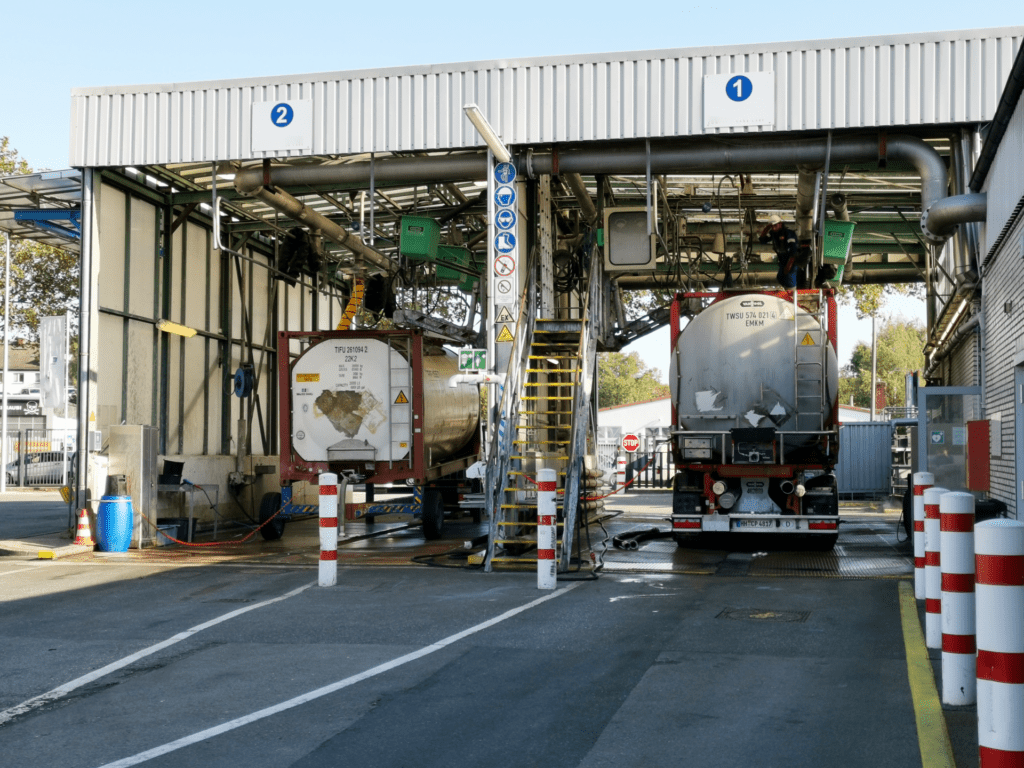
The situation in cleaning station is obviously different from filling stations. In this situation, a grounding device with recognition function is not a helper to ensure the grounding condition, but instead, a trouble maker. If the object recognition is turned off, release signals can be sent even when the grounding clamp is connecting to the gantry parts. However, in this case a safe identification of tank trucks can no longer be assured. This leads to an operational challenge: The operators of the facilities need to make sure that the grounding connection is made to the object, the workers need a reliable signal to start the washing process as soon as possible. How can we solve this conflict and keep the safety meanwhile?
TIMM Object Selector as the problem solver for cleaning stations
The grounding device with truck recognition function is surely the best choice for cleaning stations, where only tank trucks are cleaned. The requirement for the recognition of tank containers is on the other hand a challenge for the grounding devices. TIMM has developed the TIMM Object Selector to solve this dilemma.
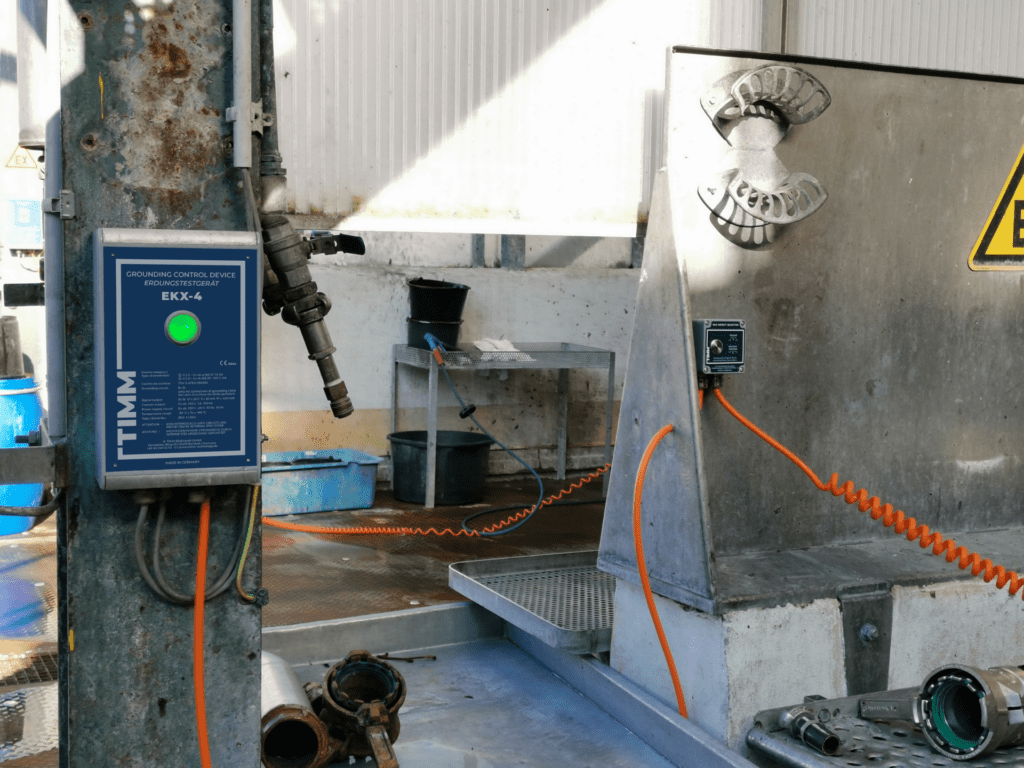
After connecting the grounding clamp to the tank containers, the device will display a flashing signal light indicating a connection to gantry parts. After having checked that the grounding device is properly connected to the grounding point on tank container, the washing worker can use the TIMM Object Selector to change the working mode of the grounding device to get the release signal. At the same time, the grounding connection is still permanently monitored and evaluated. If the grounding condition is not safe for static electricity dissipation, the grounding device will deliver a light signal accordingly and shut down the process the immediately. The object selector provides the possibility to adjust the recognition function quickly depending on the individual situation. After the cleaning process and disconnection of the grounding clamp, the grounding device will be set back to tank truck mode automatically, so that no manipulation on safety is possible. The TIMM Object Selector is a practical, user-friendly and safety-oriented solution for cleaning stations, in which different objects are cleaned, e.g. IBC, tank containers and tank trucks. On one hand, it ensures the reliable and monitored grounding connection for the operator regardless of which objects are to be cleaned; on the other, it enables efficient and speedy cleaning processes for the workers.
This articel was written by Yi Chen, Sales Engineer at TIMM
[1] IEC/TS 60079-32-1 Explosive atmospheres – Part 32-1: Electrostatichazards, guidance p. 43
[2] IEC/TS 60079-32-1 Explosive atmospheres – Part 32-1: Electrostatic hazards, guidance p. 43