A brief history of conveyor belts
Primitive conveyors have been around since 1790. The invention of vulcanised rubber in 1844 was a significant milestone. In 1892, conveyor systems used for carrying coal, ores and other products started to be developed. In 1905 mining engineer Richard Sutcliffe invented the first rubber conveyor belts for use in underground coalmines. They revolutionized the mining industry, rapidly replacing men and pit ponies. Since those formative years, conveyors have become essential equipment across a wide spectrum of different industries, none more so than dry bulk handling.
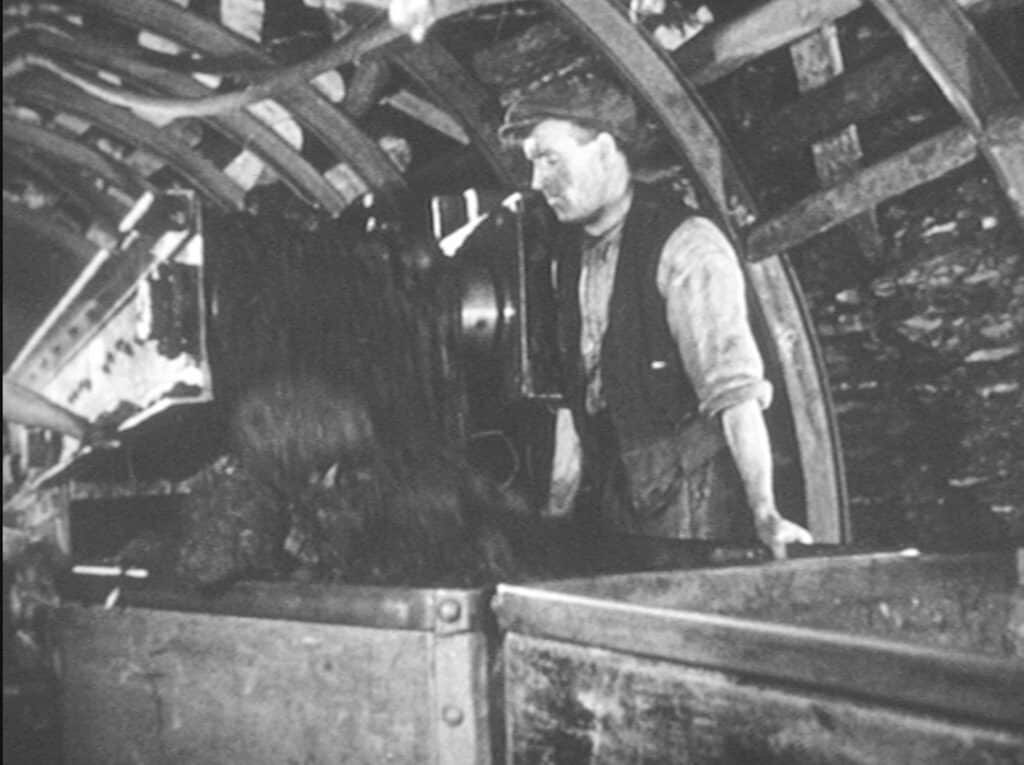
First used in mines, conveyors are now essential equipment in a multitude of industries.
The very first conveyor belts were made using a very primitive form of rubber that was sensitive to temperature changes. The rubber covered a single-ply jute or hemp (sackcloth) or cotton fabric carcass, usually joined together by what is now termed as a ‘finger splice’ jointing method. Although the jointing method worked well, the inherent weakness was that moisture penetration caused the inner jute or cotton ply fabric to rot. The inventions of nylon in 1935 and polyester fiber in 1941 led to the gradual replacement of cotton plies with the much stronger and more durable nylon and polyester fabric plies most commonly used nowadays. Over broadly the same period, natural rubber (NR) was replaced with synthetic rubber, most commonly in the form of Styrene- Butadiene rubber (SBR) and Nitrile rubber (NBR) because of its far greater adaptability and durability. The modern day conveyor belt had been born.
Increased demands
As industry and the commercial environment became increasingly competitive, the demand to maximize output and speed up the transhipment of materials also increased. Set against this was the need to minimise costs, which opened the door to the large-scale ‘economy’ manufacturers of South-East Asia. As a result, the levels of low-grade ‘economy’ imported belting have increased significantly. In fact, almost all European belt manufacturers now supplement their production by importing from Asia and re-selling under their own brand, allowing them to compete at the low-price end of the belting market.
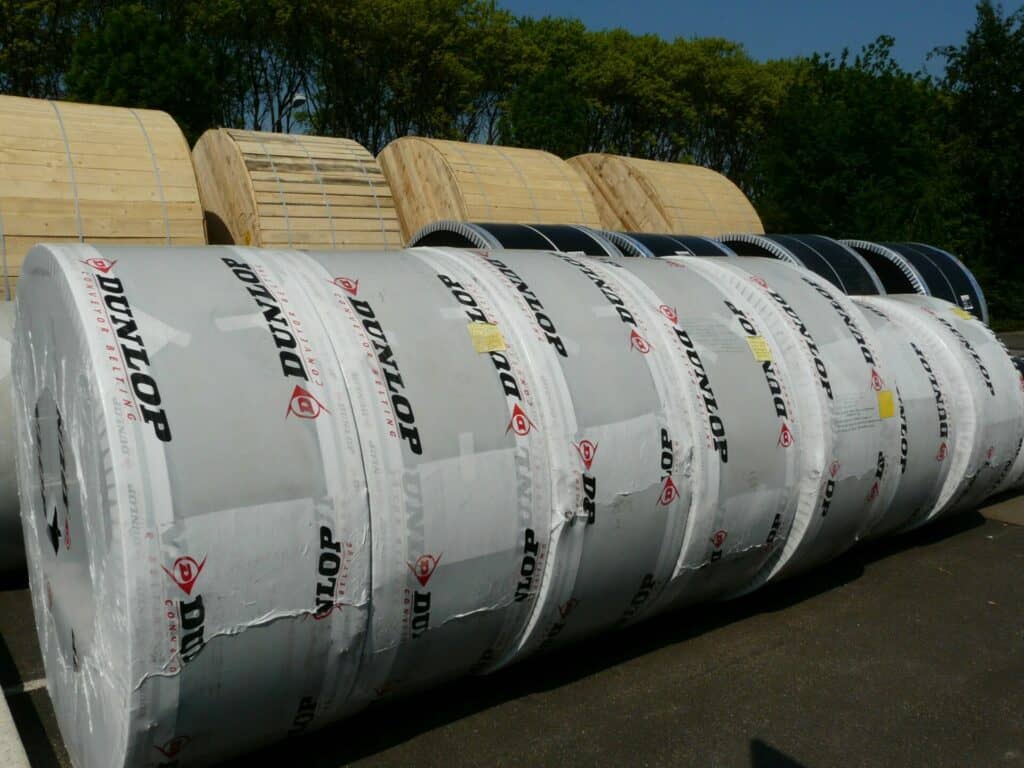
An exception to the rule – 100% made in The Netherlands
However, one major European manufacturer, Dunlop Conveyor Belting in the Netherlands, remains the exception to this practice and manufacture every belt they sell using their own facilities. Dunlop’s market approach is based solely on quality and ‘lowest lifetime cost’ and only supplying belts that provide much longer operational lifetimes than their rivals.
Lowest lifetime cost
To those seeking to reduce conveyor belt expenditure, the use of low price imported unbranded belts may seem irresistible but it creates a never-ending cycle of stoppages, repairs and replacements. The ultimate goal for the R&D team at Dunlop’s headquarters in Drachten was therefore to develop an affordable super-tough belt that would provide up to 50% lower lifetime cost compared to conventional belting.
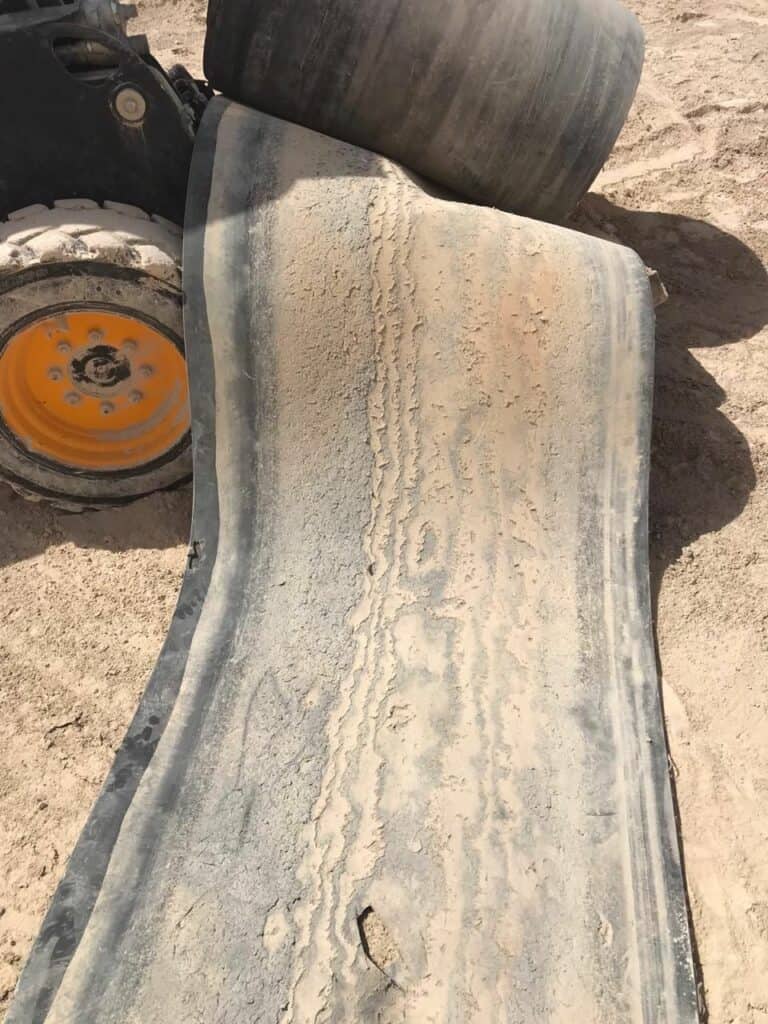
The use of imported low-grade belts creates a never-ending cycle of repairs and replacements.
In order to do this they decided to harness not only the latest advances in science and technology but also to combine them with what had worked most successfully in the past. The result was the creation of a unique super-strength single-ply belt, which they have called Ultra X.
Back to the drawing board
The objective of the Dunlop engineers was to design a belt that had a much higher resistance to impact, ripping and tearing compared to conventional belting while at the same time maximising production efficiency in the pursuit of affordability. “On demanding applications where accidental damage is a problem, the key to the solution lies in the construction of the carcass. Because we had already developed exceptionally hard wearing rubber compounds it meant that our engineers and technicians could concentrate their efforts on the design of the carcass,” explains Rob van Oijen, Dunlop‘s manager of application engineering in the Netherlands.
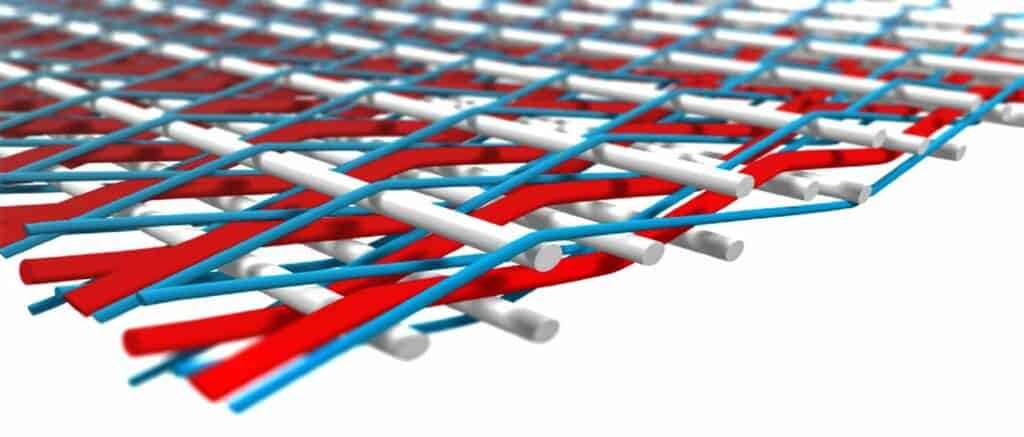
The big secret – A super strength ‘breaker weft construction’ fabric made only by Fenner Dunlop
Ironically, they discovered the answer in their Fenner Dunlop sister company’s in-house fabric weaving facility in the USA who had developed an amazingly tough patented fabric. The unique fabric uses crimped warp polyester yarns to provide high strength and low stretch. These combined with strong ‘binder’ and ‘filler’ yarns to create a super-strength ‘breaker weft construction’ that could be used to produce a single-ply belt carcass with exceptional strength and stability under load characteristics.
The discovery also provided the solution to the problem of affordability in the market. Because the single-ply carcass is made from fabric manufactured in-house they could guarantee top quality and a plentiful supply without added margins. It also helped to maximise efficiency of production because there are fewer calender runs and also allowed production runs to be longer than usual. Another bonus was that having no rubber skim between the plies not only resulted in a thinner, stronger carcass, it also helped to keeps the cost down.
Throughout its development, sections of belt carcass were repeatedly tested to destruction, including measuring the tear resistance according to the international EN ISO 505 standard. The tests revealed that the (Ultra X) fabric possessed more than 3 times greater longitudinal rip resistance, up to 5 times better tear resistance and a far superior resistance to impact compared to traditional 3-ply or even 4-ply belting.
A question of strength
So far, Dunlop have made Ultra X available in two strengths – Ultra X1, which is designed for users of EP315/2 and 400/3 conventional ply belts and Ultra X3 , which is designed to replace EP500/3, 500/4, 630/3 and 630/4 ply belts. They plan to extend that range by adding higher tensile strength versions in the form of Ultra X4 and Ultra X5. The fact that Ultra X is a single-ply construction belt designed to replace conventional two, three and four-ply belts has certainly raised a few eyebrows. The first question seems to be how a single-ply belt could possibly provide sufficient tensile strength and also have extra high levels of durability and wear resistance? Rob van Oijen is more than happy to explain.
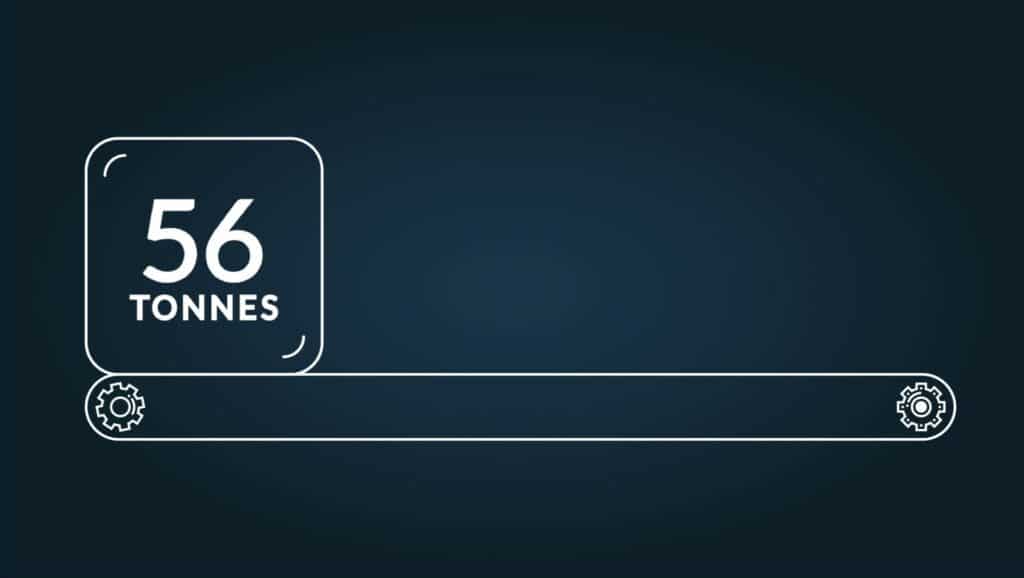
A 1m wide Ultra X3 single ply belt is able to pull up to 56 tonnes in weight.
“We keep coming back to the unique fabric that we are using, which is able to withstand the kind of punishment that would destroy a normal belt. Ultra X also has amazing tensile strength. The longitudinal tensile strength of the X1 is 330N/mm and the X3 has a longitudinal strength of 550N/mm. We stepped away from the conventional range for multi-layer belting for good reason. A single-ply construction requires a finger-splice joint to be made endless and although they take about 30% longer to make, the enormous advantage of finger splice joints is that they retain up to 90% of the belt’s tensile strength. This is why finger splicing was the standard method used to connect the very earliest conveyor belts. It worked then and it certainly works now! By comparison, a 2-ply step splice only retains a maximum of 50% and a 3-ply step joint only achieves a maximum tensile strength of 67%”.

Finger splice joints provide the greatest strength and durability
“The higher level of splice efficiency combined with the tensile strength of the X1 and X3 effectively creates equivalent tensile strengths and belt safety factors that are more than comparable to 3 or 4 layer conventional belting”.
Rob freely admits that finger splices are a little more costly but in his experience this reduces quite significantly with growing experience. The much longer operational lifetime being experienced more than compensates for the higher splicing cost. “The technical and economic arguments in favour of finger splicing are unquestionable. Finger splice joints are stronger and more durable. As one of our customers recently said, “In the past we were using cheap import belts and we often had to call the 24/7 splicers to make a new splice or do splice repairs. Also, the belts kept stretching. Since we started with high quality Dunlop belts we do not have belt stretch or splice problems anymore”.
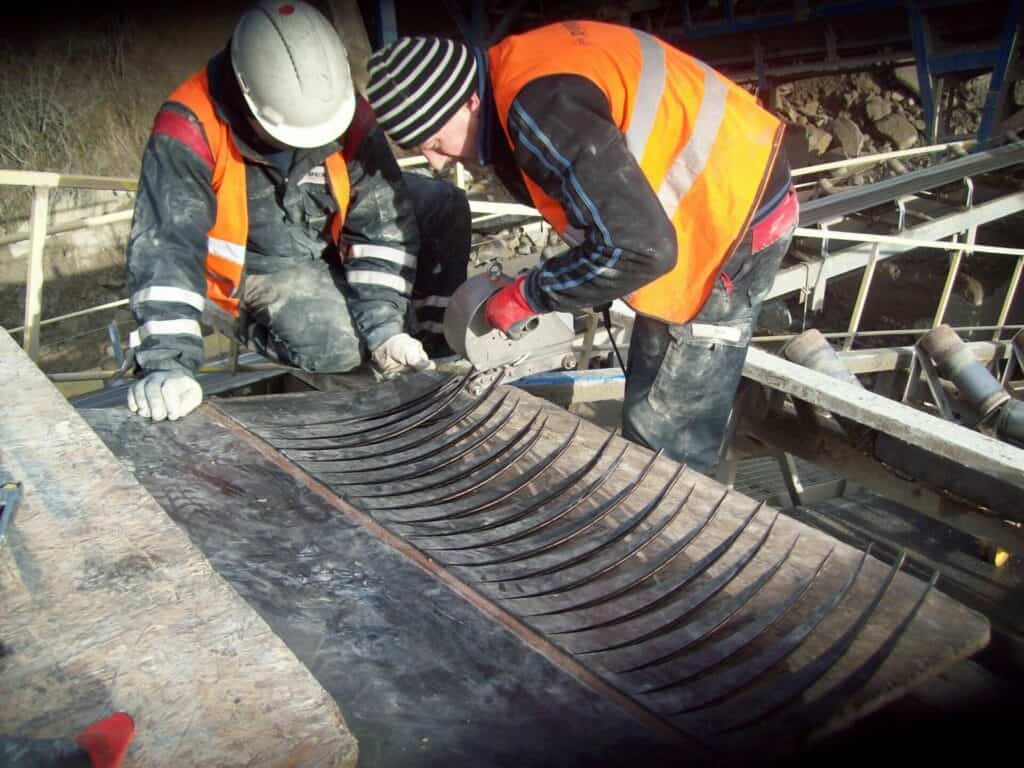
The cost of making the splice is a small fraction of the cost of a system shutdown
To help their customers, Dunlop supply splice kits including finger pattern templates, materials and tools, a guide manual and a training film as well as training and supervision where warranted. For those who still want to avoid finger splicing, the good news is that Ultra X also possesses excellent mechanical fastener retention. There certainly does not appear to be any question mark against the overall strength of Ultra X because, as their promotional film proudly states, a 1m wide Ultra X3 single ply belt is able to pull up to 56 tonnes in weight.
No complaints
When Dunlop first launched Ultra X it was a deliberately low-key affair and under the radar of most of the market. As Dunlop’s sales & marketing director, Andries Smilda explains, they had many reasons for taking such a cautious approach. “We knew from the years of research and intensive laboratory testing that we were onto something special. But Dunlop being Dunlop we still wanted to prove it in the field so we worked with several tried and trusted end-users”. “Having sold many tens of thousands of meters has confirmed beyond doubt that Ultra X is all that we thought it would be and more. We have not had one single warranty claim”.
Dunlop’s claims seem to be supported by a growing number of operators who are discovering that Ultra X has doubled the average lifetime they usually experience. In France, since replacing conventional multi-ply belts with Ultra X, an operator conveying sand and gravel has seen an 87% improvement in productivity thanks to a dramatic reduction in stoppages caused by broken splices and other repairs. And a conveyor engineer in The Netherlands remarked “Ultra X3 was best product we could find in the market, thin, light and very strong; perfectly suitable for our installation”.
A cultural change?
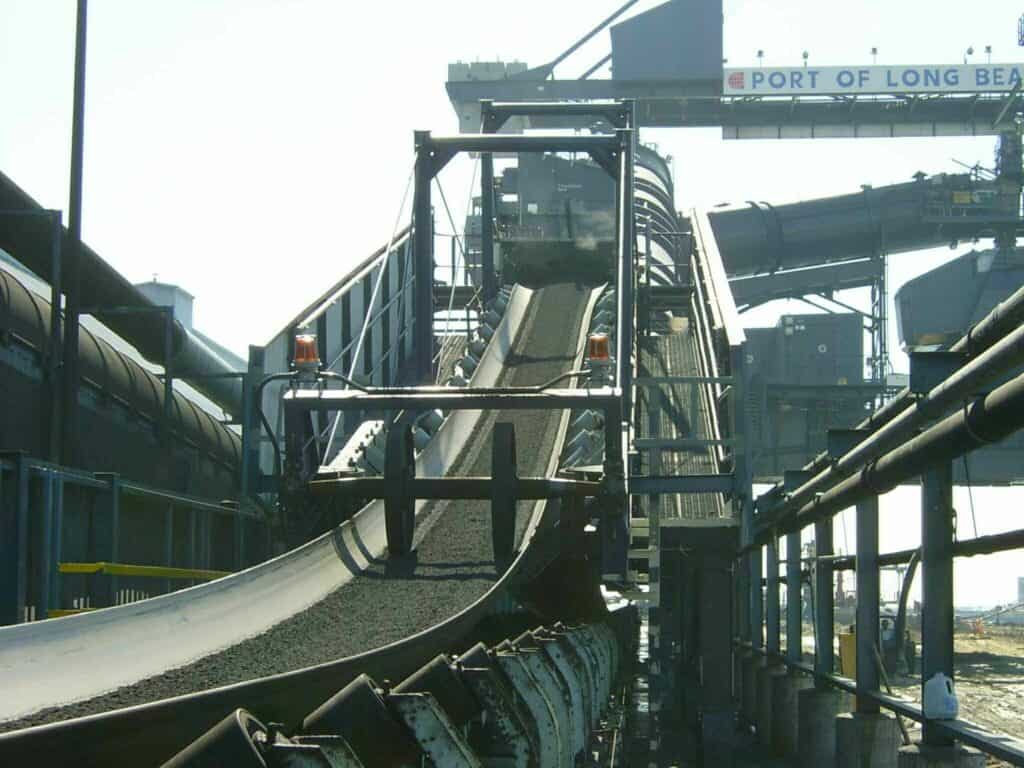
Increased strength and durability of Ultra X is leading to increased productivity
To many port and terminal operators, the idea that a single-ply construction belt can provide the necessary tensile strength while possessing considerably more resistance to wear and tear compared to conventional multi-ply belting is difficult to comprehend, especially while also competitive on price. However, if operators can look beyond traditional beliefs and thinking then I strongly suspect that Ultra X really could be a real winner for them.
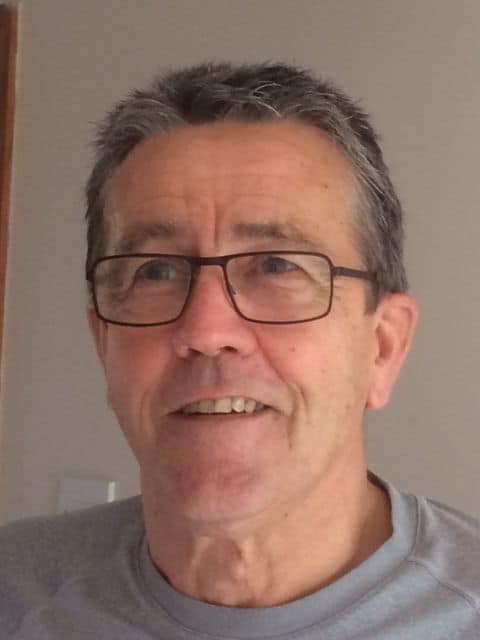
Leslie David
About the author:
After spending 23 years in logistics management, Leslie David has specialised in conveyor belting for over 16 years. During that time, he has become one of the most published authors on conveyor belt technology in the world.