To address these issues, STANDARD INDUSTRIE International has designed and further improved a containment solution called LIFTUBE®. This patented equipment is placed on belt conveyors to optimize their tightness. This system ensures a reduction in dust emissions, material losses, maintenance time and guarantees operator safety.
LIFTUBE® replaces 3 roller stations on conventional conveyors. In practical terms, standard 1-metre modules that can be upgraded are easily installed on all or part of a new or existing conveyor, while retaining the original belt, frame and motorisation. The system is installed between the loading and unloading points. Available in widths from 500 to 1600 mm.
Thanks to the LIFTUBE® design, the belt is contained within a sealed envelope, reducing the risk of material escaping to the outside. Because the cover can be clipped on, it fits perfectly into the upper grooves of the edge supports. It is also watertight thanks to the foam-laminated hoops installed at each end, which enclose the strip.
When a plant shows interest in covering its conveyor with LIFTUBE®, STANDARD INDUSTRIE International systematically carries out a full on-site audit to study the installation of the conveyor and the behaviour of the belt during material transport.
If a new conveyor is to be installed, the LIFTUBE® study is carried out on the basis of plans and according to the plant’s objectives. For example, in a limestone quarry: to avoid as much loss as possible when material falls onto the belt.
During the site survey, the following control points are identified:
- Study of feeding points. This is where there is a major safety issue for operators. This area of the conveyor is particularly in need of protection.
- Check the width of the conveyor, troughing and inclination.
- Observe the belt running when empty and loaded. See if it runs to the left or to the right. In which direction it moves the most and whether it vibrates.
- Check whether the belt is turning over.
- Check where the material falls. This is where there is a major risk of material loss and the spread of dust. The material must be prevented from spreading across the entire width of the belt.
- Validation of the need for an installation resistant to high temperatures.
- Check the motor power required for the planned equipment (more or less than 20 meters of LIFTUBE®).
The benefits of LIFTUBE® : - All areas of the conveyor equipped with LIFTUBE® are protected, guaranteeing operator safety.
- Sealing is optimized to prevent dust emissions.
- The belt edge is held in place along its entire length, avoiding the chain effect.
- The drop zone is equipped so as to keep the vein of material well in the middle and to achieve throughputs of around 10 to 15% higher with the same width of strip. This equipment ensures that all the material flows in the right direction and not into the environment.
- The unique roller tilting system provides easy access for changing this wear part.
- The LIFTUBE® can be fitted to belts with an incline of up to 22 degrees.
- Some LIFTUBE® installations can handle more than 1,000 tons of material per hour.
On which types of conveyors and for which applications is the installation of LIFTUBE recommended?
- In mines and quarries: Conveyor for transport to crushers, conveyor at mine exit (ores: gypsum, anhydrite, etc.)
- In cement plants: kiln feed conveyor (transport of coal, alternative fuels), mill feed conveyor, fly ash conveyor, clinker cooling conveyor, clinker feed conveyor, shipping dome conveyor, truck loading conveyor, etc.
- Glassworks: cullet and broken glass conveyor (production scrap), protection against crystalline silica dust emissions.
- Waste treatment and biomass powers: conveyors for fuel, sawdust or hazardous waste.
- Steel industry: conveyors transporting ore, limestone, coke, coal and sinter.
Case studies in the use of LIFTUBE® :
VEOLIA Germany – Power generation
PROBLEM :
This wood recycled plant producing energy based in Bavaria was looking for a solution that would fit in with its plan to reduce emissions and seal its old conveyor belt. The passage of shredded wood of different particle sizes required optimum sealing to avoid overflowing and the risk of the belt shifting. The 650 mm belt is fed with raw material by a loader, which delivers all types and shapes of wood regardless the size of material. This creates jolts in the belt and risks the covers being torn off. In addition, the specific nature of the region, with its high snowfall in winter, meant that the hoods had to be more resistant.
SOLUTION :
STANDARD INDUSTRIE, in collaboration with REMA TIP TOP, developed a specific solution to meet the requirements of the plant’s main conveyor sealing project.
As a result, 55 meters of LIFTUBE® 650 were installed on a conveyor belt carrying shredded wood to the boiler for energy production.
RESULT :
Raised hoods with an extra-large opening allow wood to pass through without a badly trimmed board tearing the hoods off. What’s more, if a piece gets stuck, the oversized hatch allows you to grab and pull out oversized pieces. What’s more, the LIFTUBE® design offers a special joint to ensure watertightness. The hoods have been developed with a thickness greater than the standard dimensions to withstand the weight of the snow, so they won’t sag.
WIENERBERGER France – Brickworks
PROBLEM :
Wienerberger is a brick and tile factory that dates back to 2011 and produces 150,000 tons of bricks a year. To achieve this level of productivity, the heart of the plant, where production takes place, is automated: “Everything works by itself. That’s our advantage here. We are one of the most automated and robotized plants in the group”.
In 2021, regulations will require factories using silica to control the emission of so-called CMR (Carcinogenic, Mutagenic, Reprotoxic) dusts. This is what is motivating the Group to invest in improving the safety of its staff.
SOLUTION :
The project involves equipping three existing belt conveyors:
TB3: complete LIFTUBE® equipment on a 1200 mm wide belt transporting clay
TB2 & TB1: partial LIFTUBE® equipment on a 1000 mm wide belt, mainly at the drop points and the protection of re-entrant points.
The hood prevents dust emissions. It prevents the conveyed product from being polluted by contact with the outside environment. The thickness of the cover is greater, adapted and recommended for product chutes. The centring plates channel the material in the middle of the belt so that it is not in direct contact with the lateral curtains, thus limiting wear on the lateral curtains.
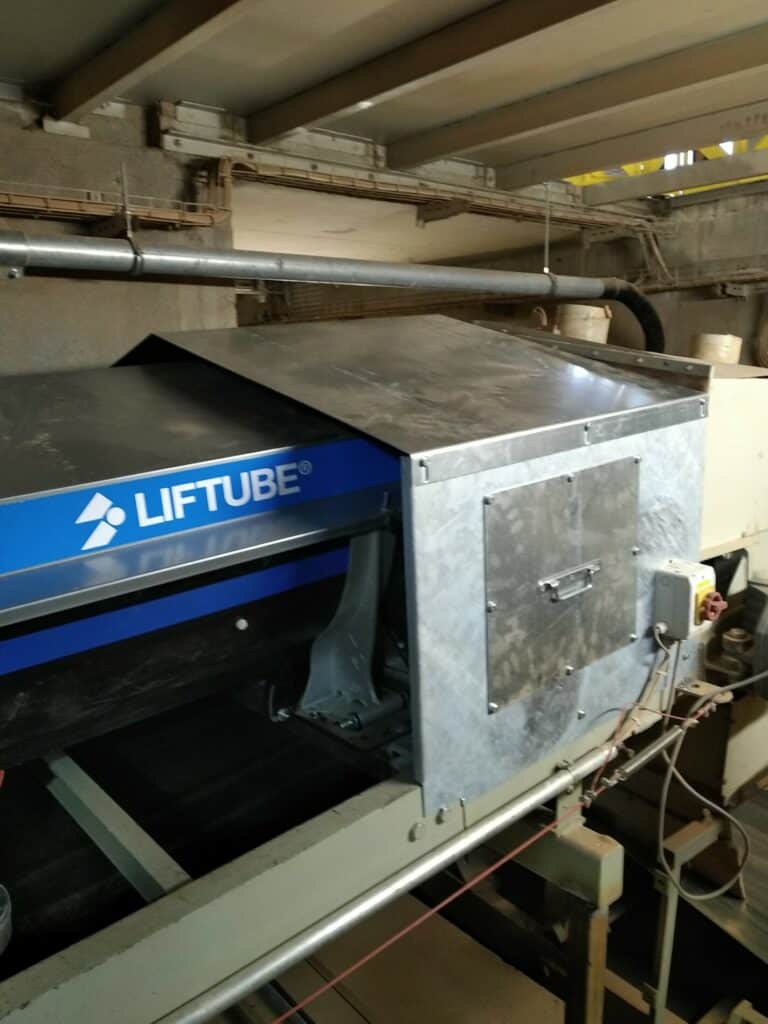
RESULT :
• Environment: reduced dust emissions between loading and unloading.
• Quality: full protection of the material. No product pollution.
• Total safety: protection of entry points.
• Economy: minimum and very simple maintenance.
• Cost-effectiveness: optimized flow rates.
• Standard, adaptable, upgradeable components.
• Installation of the LIFTUBE® system without modifying the installed power.
CONCLUSION
To meet the challenge of efficient powder waste management in processing industries, containment devices on conveyors are becoming essential. While current solutions such as the LIFTUBE® are effective, STANDARD INDUSTRIE International understands that changing environmental standards and increasing corporate environmental awareness are driving a continuous search for innovation. The future of powder waste management will involve the integration of intelligent technologies, increased automation and even more sustainable practices. However, we must remain vigilant when it comes to implementation costs.