This special bio segment, where proteins are grown and manufactured in a sustainable and environment friendly process, has been under development at least the past 10-15 years. Mostly such proteins are today used in animal feed.
In the early 2020 Alvibra started investing quite a lot of time and work in this, still relatively new, bio protein market, and especially in the end-of-line part of it, where the grown larvaes must be seperated from the frass.
During 2020 Alvibra delivered the first pilot-plant, from which an additional amount of experience has been harvested. It is still operational today.
During our jurney we learned that it is not as easy as one might think. As a vibration technology specialist, our BSFL solutions includes careful technical considerations and validations based on real life experiences. Our feeding and screening solutions are thereby put together and well balanced between powerful vibration amplitude, -frequency and -angle, combined with a design suiting the requirements of the operation, cleaning, product and enviroment. Designs of our belt and other type conveying is specifically suited for this segment as well.
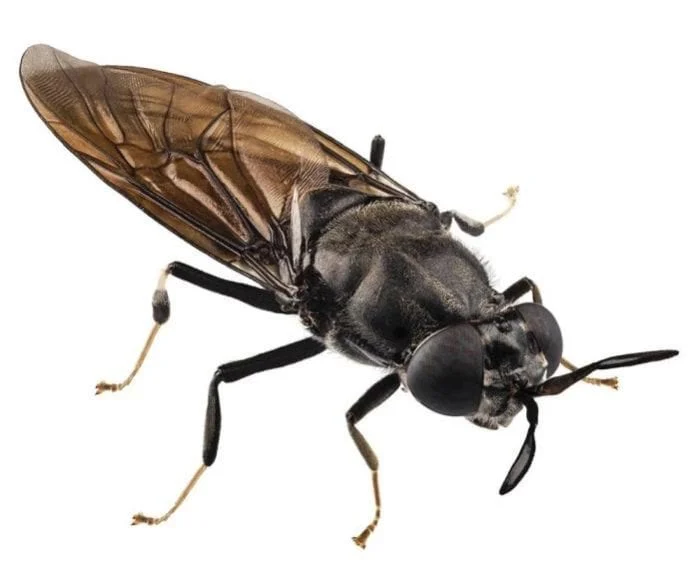
Today there are more small and a few large scale BSFL plants operational around the globe. We have now also learned that the various BSFL growers don’t process and work the same way, which again means each project is either a little or a lot different from each other.
In other words Alvibra don’t offer or deliver standard equipment for BSFL production, we offer dedicated BSFL equipment based on know-how and specific data matching the various BSFL plant requirements.
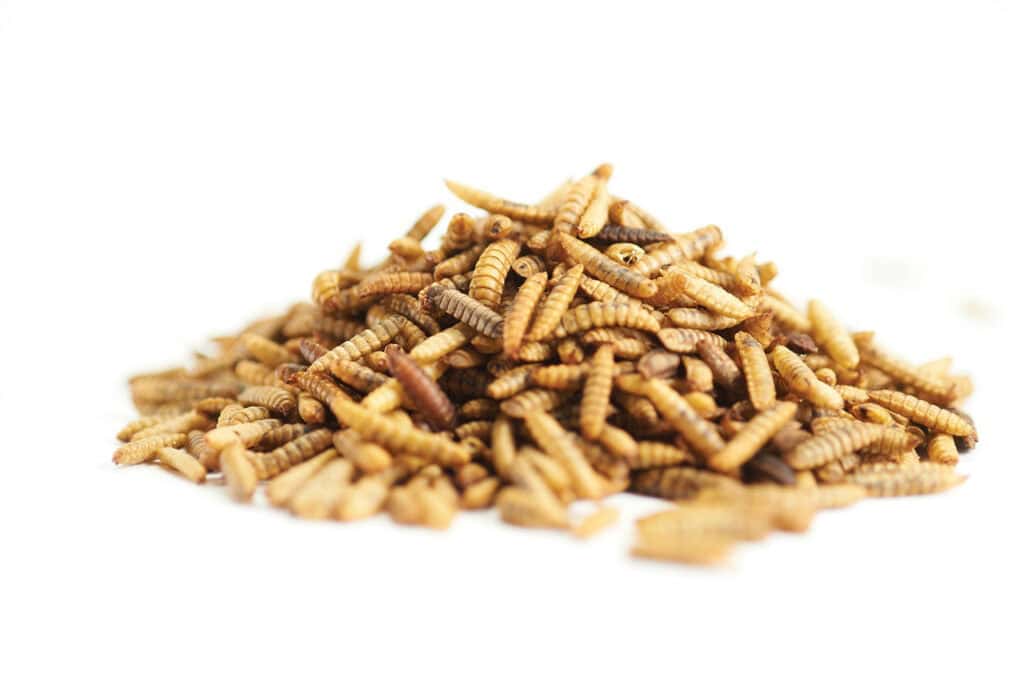
In short, when the larvaes and frass are automatically emptied from the growing containers, we typically take care of further transport, feeding, spreading, screening and further handling or distribution of the seperated larvaes and frass.
However, recently during this exiting and challenging jurney, Alvibra also developed and delivered equipment for further upstream BFSL processes, where clearly the larvaes are much smaller and even more tricky to handle.
The header image shows an example of a delivered end-of-line installation handling 9-10 tph of mixed BSFL and frass. The BSFL sifters include oversize lumps removal, a continuous screen cleaning system for reducing build-up and a quick-release system for fast and easy screen replacement.
The delivery also includes easy cleanable platform ramps for safe access of supervision, cleaning and screen-replacement including also transistion conveying belts. The line is carefully designed for good access and made in a U-shape configuration – and is further already prepared for future extensions like product buffering and washing etc.