It is a cost-effective maintenance solution that uses 6 bar compressed air only when the shots are activated and is adaptable to many bulk areas. STANDARD INDUSTRIE International’s technical teams study an optimal installation recommendation according to the clogging factors and the environment of use (risks, high heat zone, corrosiveness, humidity).
Particularly attentive to its customers’ requirements, the design office team spent nearly 3 years testing modifications to its legendary AIRCHOC® air cannon:
- The quick exhaust valve was replaced with a pneumatic valve system that improves impact force.
- The silencers have been replaced by a protective cap which, in addition to protecting the new valve system, absorbs the noise caused by the shots. The main advantage is that there is no risk of clogging in the exhaust system.
- As these 2 wearing parts (Quick exhaust valve + Silencer) are removed from the design, maintenance is simplified and less expensive for the user.
What benefits does the new version of the AIRCHOC® air cannon bring?
The AIRCHOC® has always had the performance, profitability and safety characteristics expected by user customers. The latest innovations of the AIRCHOC® version 6 are focused on:
Compressed air savings
Thanks to a better sealing of the piston and thanks to a better impact force on the clogging (10% higher than the old version). Indeed, the air pressure can be reduced for an equivalent result. The version 6 of The AIRCHOC® meets the challenges of the global energy saving policy.
Reliability
Particularly due to an improvement of the impact force of the shots coming from the cannon. (No quick exhaust valve): No air passes through the piston seal, thus no wear and tear on the seal. This means that the air cannons are always available for preventive shots and thus maintain the production flow. The tests guarantee 3 years of shooting cycles without replacement of the triggering system.
Spare parts
Which have been streamlined and selected for their durability. The new design of the AIRCHOC® with fewer wearing parts and components ensuring good resistance, allows for reduced and simplified maintenance. This is a considerable advantage when maintenance operations require access at height and important safety precautions. In this regard, Standard Industrie has also created an AIRCHOC® maintenance kit that avoids operators and foremen from having to perform lengthy and costly interventions. Here again, Standard Industrie responds to the need to save on maintenance and spare parts for large consumers such as cement plants.
In summary, the AIRCHOC® is the solution for plants that want to reduce maintenance and spare parts replacement on their cleaning system, and reduce their compressed air consumption.
The first few customers already benefiting from the AIRCHOC® improvements are very satisfied, as testified by Abraham Campos Figema, Maintenance Manager of the cement plant “CEMENTOS FORTALEZA” in Mexico.
Since 2020, this customer agreed to test the prototype of the new AIRCHOC® 6 air cannon head created by STANDARD INDUSTRIE International and placed in the plant on the kiln inlet.
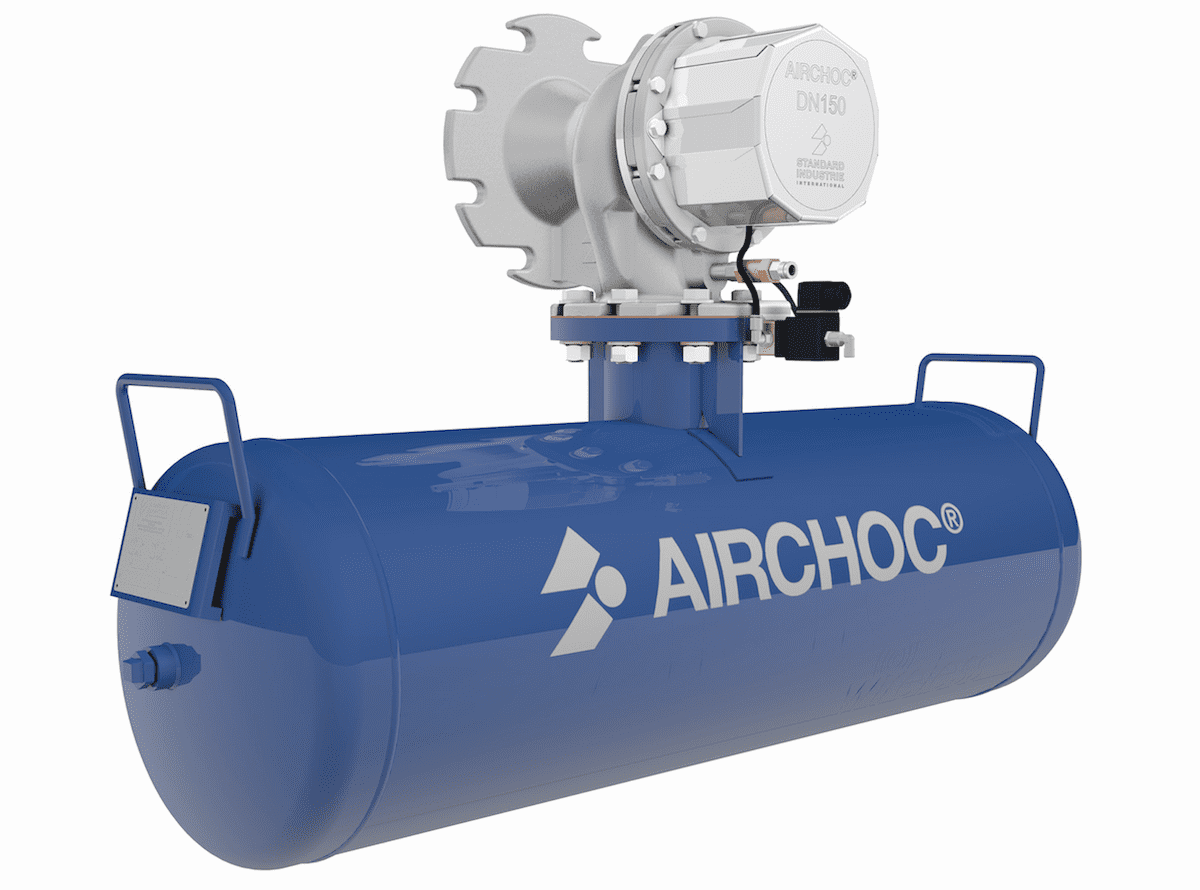
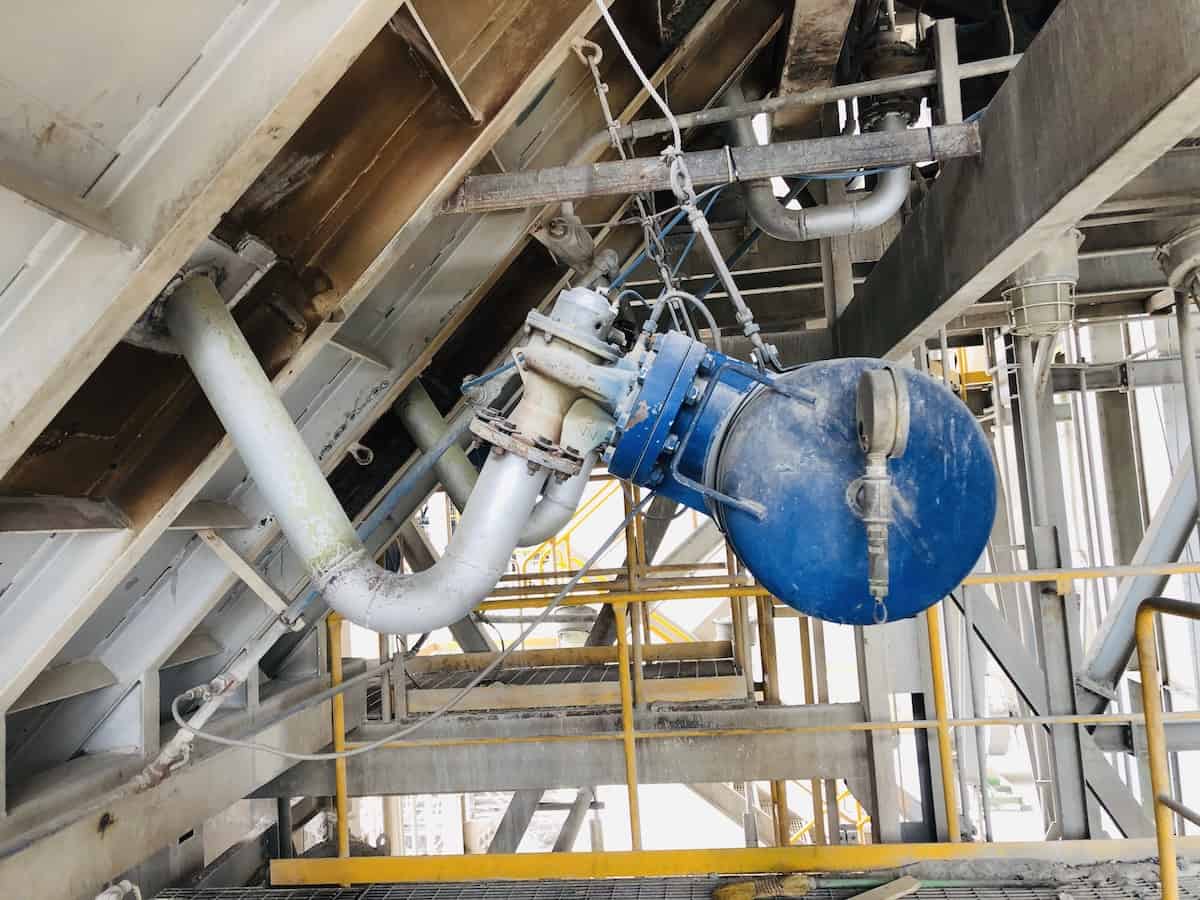
After 2 years of use in the research and development of this product, here are the answers it has given:
“How much maintenance time do you save with this new AIRCHOC® head compared to the previous version 5 for one year of operation?
24 working hours per year and less risk of intervention on the hot equipment.
How many maintenance kits for the quick exhaust valve have been saved in one year?
24 maintenance kits.
What do you think about the reliability of this new development (ACCMECBRD610) for the future?
The reliability is very good because there was no maintenance for one year.
Have you noticed a difference between version 5 and the new prototype, what do you think about the power (impact force) of this head compared to the previous one?
Of course, the head is much stronger than the previous one. The impact force is good for the area where we placed it, which is the hottest area of our system.
Do you need a more powerful conical head to reduce the pressure level of the compressed air and save energy and money?
Of course, saving compressed air means saving energy and therefore money.
Do you have any other comments on your experience?
Yes, it is good that there are developments to increase the reliability of this equipment because it mitigates the risk of having personnel working on hot equipment, CONGRATULATIONS!”
STANDARD INDUSTRIE International has succeeded in offering a solution that is both efficient and economical. Relying on its proven expertise with many bulk manufacturers around the world, the company is committed to offering reliable and durable “made in France” equipment to ensure that its customers maintain their productivity.