Poor flow uniformity can cause under drying (which can create processing problems through the remainder of the plant, packaging problems, shelf-life and product stability issues, as well as clumping, caking and other product quality issues. Poor flow uniformity can also cause over-drying which can increase the risk of product degradation, dust generation, explosivity and fire risks, as well as alter the chemistry and diminish the product quality and performance attributes.
Production of particulate materials often includes one or more of the following processes: washing, crystallization, precipitation, polymerization, wet agglomeration, or other means to produce the desired particle characteristics. The resulting product often is a slurry, paste, or wet granular material or cake. In most cases, these processes are followed by solid-liquid separation and or then through thermal processing (drying). Slurry is often pumped into a centrifuge, a filter, or a press to remove the bulk of the liquid before further thermal processing. Between these two process steps, thickened slurry, paste, or wet cake must be reliably stored and metered which is often overlooked.
Thermal processing efficiency is closely tied to the uniformity of solids in-feed. Surges in solids or liquids in the flow will cause insufficient drying. Loss of feed or underfeeding can cause over-drying the material. To ensure efficiency and reliability as well as to provide safeguards to the process, the majority of all thermal process steps require a surge of material and a means of accurately feeding. This is certainly the case for batch to continuous operations.
Reliable storage and feed system design requires a clear understanding of the flow properties of the wet solids for the range of operating conditions.
Flow Concerns
Wet materials in general are hard to handle and are prone to flow problems. Flow stoppages caused by arching or ratholing, and loss of surge capacity due to material buildup on the walls of storage and transfer chutes are very common in many of these systems. Material buildup and dead regions can cake, clump or degrade and produce additional problems in feeding and thermally processing the material. Problems in this part of the system often result in dangerous operator interventions or in an array of flow-inducing support equipment that rarely ensures the desired level of process robustness and capability needed. Often unplanned downtime is required to clean the system out and bring the process back into conformance.
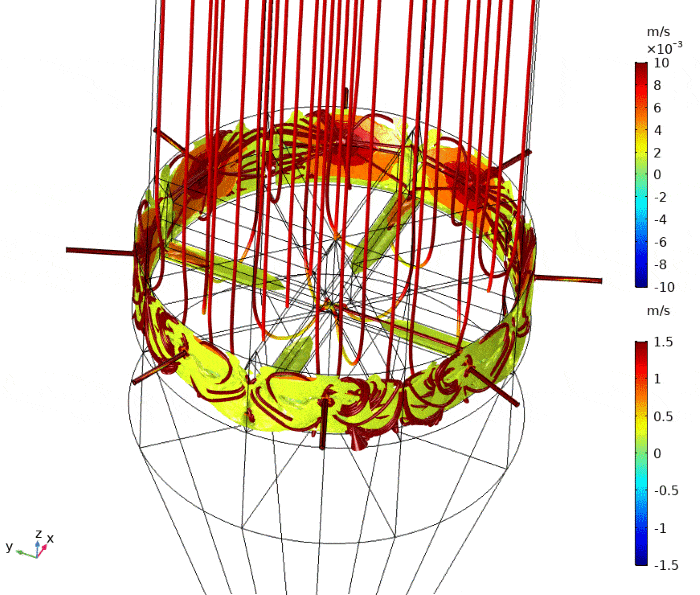
Problems with wet material handling can be avoided if the equipment designs are based on the flow properties of the particular material handled. The necessary flow properties include the Flow Function (unconfined cohesive strength as a function of consolidation pressure), the wall friction angles, the chute angles, and the compressibility, as well as permeability for cases of fine powders (1). These properties can be used to design hoppers, feeders and chute transfers to provide reliable flow and prevent buildup and flow interruptions. Flow property information can also be used to size pressure isolation devices to achieve uninterrupted flow at the desired rates for thermal processing above and below atmospheric pressure (e.g., flash, rotary, fluidized, vacuum, and some freeze/cryogenic processes). The field of science on the flowability of bulk solids has come a long way in the last 50 years with many reliable, standardized methods (2).
Case – Direct Thermal Processing
Direct contact thermal processing can be economically accomplished for many solids. Thermal exchange is accomplished by injection of controlled, conditioned gas flow at a set temperature which usually flows countercurrent to the solids flow (can also be cross flow). These units often provide efficient heat transfer by achieving intimate contact between the treatment gases and solid particles. Additionally, these units can reduce capital expenditures by doubling as storage or surge capacity and are more tolerant of, and can recover from, upstream process perturbations as they can enable very long residence times (hours) of thermal exposure.
Controlled residence time of the solid particles and uniform gas distribution is a critical part of the unit design and a continuous operation is typically desired and is possible. The unit must be designed to ensure robust mass flow, i.e., all of the particles are in motion as material discharges from the bottom outlet. Material from the center as well as the periphery moves toward the outlet. In thermal treatment applications, a near-uniform velocity is essential to enforce uniform residence time. This usually requires a design that not only provides mass flow but also provides a low-velocity gradient in the hopper.
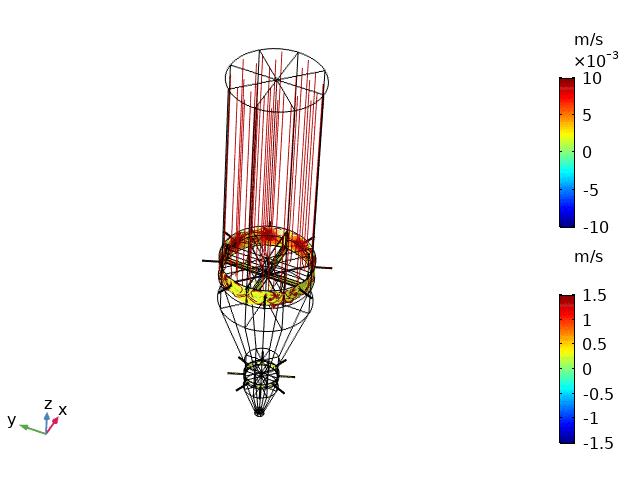
For these units, there is often a limit to the amount of gas that can be injected based on the settled bed permeability and compressibility. Too much countercurrent gas can upset solids flow and induce fluidization. A proper design ensures this will not occur. This method is routinely used in petrochemical plants (3) after the polymerization reactor and before the secondary operations (extrusion/pelletization). Solvent-laden polymers are direct thermally treated and residual polymerization, catalyst deactivation, and monomer degassing occur all while providing a buffering stock to downstream processing.
Case – Reliable Feed Of Wet Cake
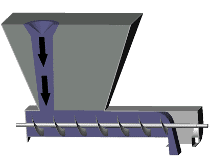
In a zirconium sulfate processing plant, wet cake discharged from a belt press into a chute which functions as a surge hopper with a screw feeder beneath to meter the material into a downstream flash dryer.
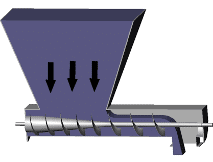
The original system experienced constant plugging problems and created enormous upsets and control problems in the flash dryer. An examination of the flow properties of the wet cake explained the behavior and gave the basis for correcting it.
The wet cake had significant cohesive strength and would easily arch if given the opportunity. The feeder attached to the bottom of the chute had a “V” trough design (as an equipment cost savings). This essentially added a small (but, as it turns out, very significant) convergence at the bottom of the chute and provided the support necessary for an arch to form. Another feature contributing to the problems in this system was the design of the screw itself. The use of a constant pitch conveying screw (again as an equipment cost savings) in this application prevented flow from occurring overall but a very short length of the chute. A variable pitch, variable shaft screw replacement corrected this, along with a change to a U-Trough.
REFERENCES
(1) Carson, John, Pittenger, Brian, Marinelli, Joseph, “Characterize Bulk Solids to Ensure Smooth Flow”, Chemical Engineering, April 2016, pp. 50 – 59.
(2) ASTM D6128-00 Standard test method for shear testing of bulk solids using the Jenike Shear Cell. ASTM D6773-02 Standard shear testing method for bulk solids using the Schulze Ring Shear Tester.
(3) Pittenger, Brian, “Purging Volatiles in Polyolefins Processing”, presented at 26th Annual Polyethylene/Polypropylene Chain Global Technology& Business Forum, June 26-28, 2018, Düsseldorf, Germany