Kinematica offers a gentle solution for foaming instant coffee to improve flavor, instant properties, and drying process efficiency.
Coffee Powder With Manimal Flavour And Instant Properties
Conventional methods for the production of soluble, dry coffee are spray drying or freeze drying. They require high temperatures and long residence time – both killers for sensitive coffee flavours.
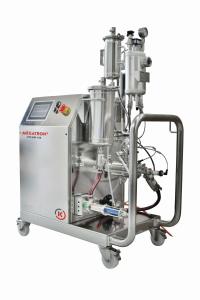
Manufacturers are looking for drying treatments that are gentler with lower energy requirements. Foaming of coffee prior to spray or freeze drying is a well-known process.
Foamed coffee powder reduces the bulk density, which directly correlates with the treatment time and temperature. The lighter the powder – the faster the heat treatment, the better the flavour quality and the better the instant properties.
The foaming systems based on rotor-stator principles present on the market require a harsh treatment of the raw material, which is not desired by the producer.
The Membrane Technologie For More Flavour
The foaming technology MEGATRON® MT-MM from Kinematica offers a gentle treatment for the creation of a micro-foamed structure. Gas is sparged through a dynamically enhanced metal membrane with pore sizes down to 2 µm. The gas bubbles are detached from the membrane by a dynamic cylinder leading to the required shear rates for smallest bubbles.
This design enables the decoupling of the throughput from the shear rates, which is not solved in conventional membrane technologies. The MEGATRON® MT-MM is ideal for sensitive material due to its special design, leading to an order of magnitude smaller thermal and mechanical load compared to conventional rotor-stator foaming systems.
The Ideal Solution For Pilot And Production Sizes
The foamed structure can be adjusted to the desired properties. Bubble sizes from 2 to 200 µm with a gas fraction up to 90 % can be reached. The membrane design allows a narrow bubble size distribution for long lasting and stable foam.
Kinematica offer two configurations: (1) a pilot scaled version with a through put from 2 to 70 L/h and (2) an industrial scaled version up to 300 L/h. The integrated cooling systems allows a precise control of the processing temperatures from 5 to 80 °C.
Kinematica provides you with the perfect dispersion solution, tailor-made and Swiss quality. In addition to our flexible equipment and our technical support, we also offer you scientific support – from ideation to prototyping in our facilities with your material.