The growing popularity also means that more vegetable proteins are needed, which come from products such as soy, peas, or grains.
For this reason, the client RMG B.V decided at the end of last year to invest in the construction of a new grinding installation and bought an Alpine fine grinding mill for this purpose.
RMG B.V. already has several lines operational for grinding various food products such as cocoa and has already gained extensive experience with this.
Outside the mill itself, air management is just as important in a grinding process. For this RMG B.V approached various system integrators. Poeth Solids Processing had extensive experience in building total processes in which filters and air transport are a crucial part. Poeth started building grinders for wind and water mills 100 years ago and has developed further over the years with the construction of hammer mills and complete grinding and solids process lines. However, Poeth does not produce fine grinding mills himself, but only hammer mills (finenesses up to approx. 200 microns), but has sufficient know-how for the entire periphery around a fine grinding mill. RMG B.V.; “Poeth soon came up with a well-thought-out technical total concept for the integration of the Alpine mill. Since these large filters are also developed and produced in-house at Poeth, they were able to respond flexibly to our specific wishes. The limited installation height and the fact that the roof could not be opened required a custom solution with insight into how to assemble the whole. They had already delivered projects and machines to us that we were very satisfied with, which is why the choice quickly fell on them ”.
Process description:
Via an existing pneumatic transport, the product is sucked by means of a transport switch to the new separator above the mill. A magnet and metal detector with an ejection flap ensure that no metal parts can end up in the mill. A buffer bunker above the mill ensures that there is always enough product above the mill. The mill is fed by means of a frequently controlled lock and is linked to the power consumption of the mill. The shredding takes place when the material to be ground hits the rotor and fixed rupture discs, with impact speeds of up to 140 m / s finenesses of d97 = 10 µm can be achieved.
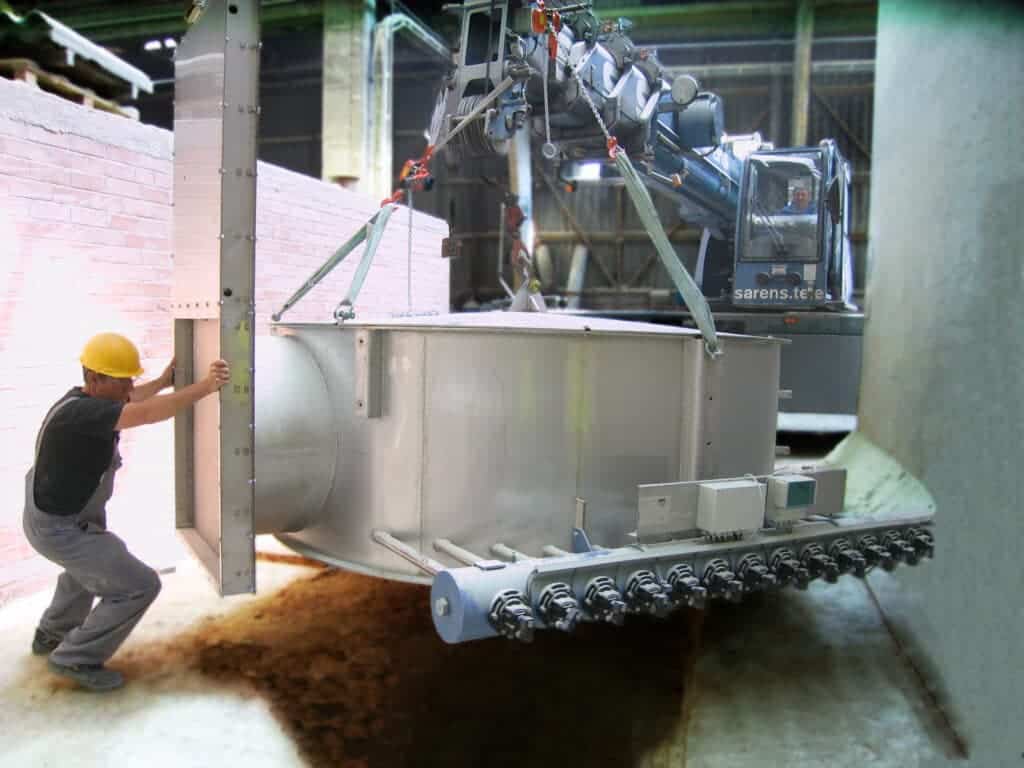
A 90 kW frequency-controlled fan provides a capacity of 10,800 m3 / hour at a static pressure of 19,224 Pa. The air is brought into the grinding chamber via 2 points, a correct regulation between these two flows ensures optimal grinding results. In many grinding processes, the air quantity determines the residence time in the grinding chamber, which in turn has an effect on the fineness. A shorter residence time results in a coarser grinding. The sucked-in air is pre-filtered by a Hepa filter. The mill is of course equipped with the necessary atex facilities. The grinding filter is pressure-resistant and equipped with various facilities such as explosion pressure relief.
Atex
The filter that extracts the mill is fitted with a bursting disc. This is a deliberately chosen weak spot of which the collapse pressure (burst pressure) is known in advance. This is safely discharged outside via a short channel. Explosion pressure relief does what the word says and no more than that: it relieves the pressure so that the filter in which the pressure could rise as a result of an explosion does not explode and become a dangerous projectile, a kind of fragmentation bomb. An Atex-approved explosion panel opens in the event of an explosion, but will not fragment, otherwise it would not have been certified.
Since the filter is inside, the explosion flame and pressure must be led to the outside by means of a relief channel. However, this is only possible under strict conditions, because, among other things, the efficiency of the bursting disc decreases sharply with the length of the channel and is therefore limited in its applicability. If a relief channel is not possible, a flame filter over the explosion panel offers freedom of installation in many cases.
In addition to controlling the explosion within the filter box, measures have also been taken to prevent the explosion from spreading to other parts of the installation. An explosion non-return valve is placed in the suction pipe. The damper blade is kept open by the airflow. In the event of an explosion, this airflow is cut off and the valve closes by its own weight and blocks the pipe. The non-return valve thus compartments both flames and pressure.