Named for this achievement, these sieves are designed to combine strength, simplicity, and superior sifting. The sieves offer a larger net screen area per stack than previous sieves, fewer fasteners, and no gaskets. “We set out to develop a sieve that would be leak proof down to a minus 100-micron particle size without the use of any gasketing,” said Jeff Seeger, senior technical sales engineer.
Behind the engineering of the Summit Sieve was the goal of creating a sieve with more net screen area but weighing the same or less than the current HDPE plastic NOVA sieve. Culminating from Great Western’s knowledge gained in working with modular sieves and plastic sieves, the Summit Sieve has been proven to improve production capacity, equipment service life, and meet or exceed product quality assurance standards.
The Summit Sieve features a revolutionary seal design which uses a combination of three different techniques to seal without needing gaskets for the entire life of the sieve. The design of the sieve helped Great Western to create new precision manufacturing techniques during the fabrication process. This precision manufacturing process creates a tray that interlocks with the sieve above and below to create the gasketless seal.
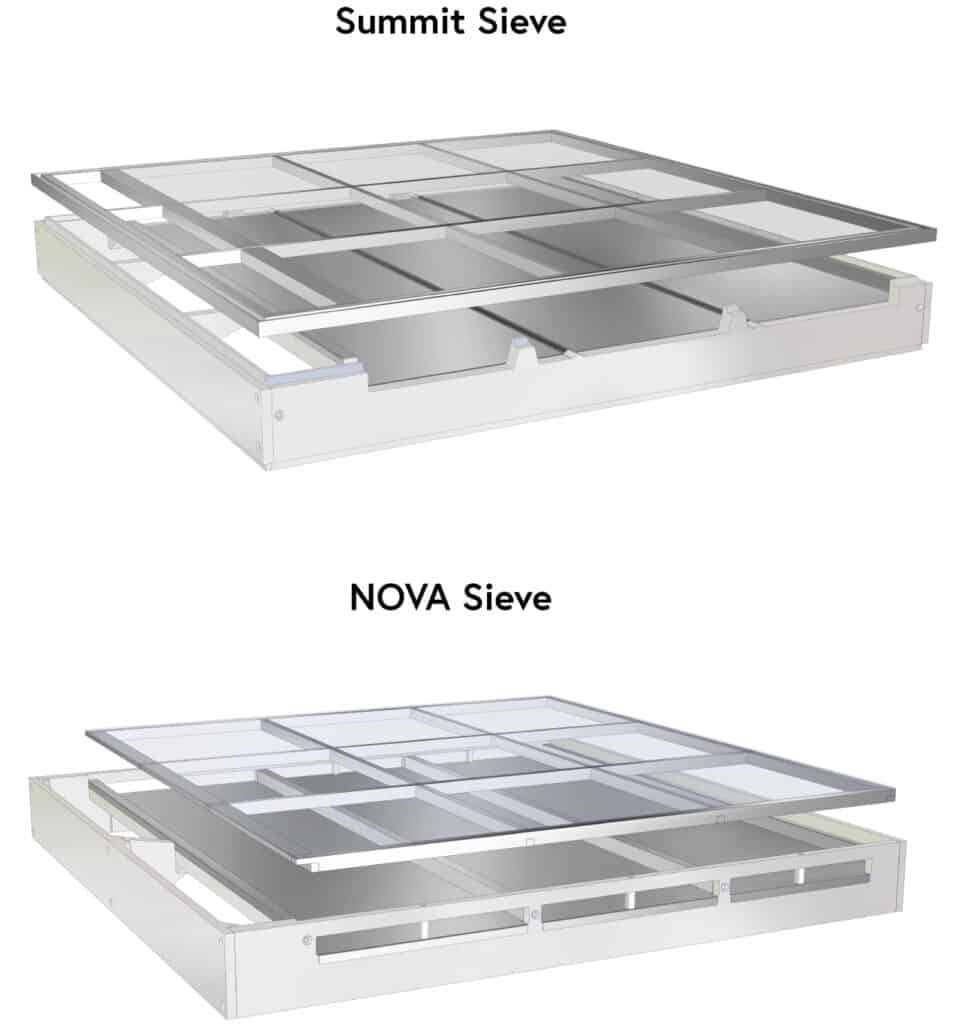
In comparing the Summit and NOVA sieves, the most obvious difference is the design of the screen tray. For the NOVA sieve, the screen tray nests within the sieve, uses combination pan and screen cleaners, and does not use a backwire. The Summit Sieve screen tray features the same beveled edges of its sieve, and interlocks at the sieve’s edges as part of the sieve stack. This design helps to improve the seal by eliminating the issue of friction between sieve-to-sieve gasketing. It additionally helps to create more strength throughout the sieve stack, as the underside of each sieve locks directly into the screen tray below it.
“By interlocking the top and the bottom of the sieve with an aluminum tray, this prevents any bowing of the plastic side pieces,” Seeger said. “We also incorporated support columns that line up from top to bottom of the stack to give added strength to the sieve to prevent any sagging of the side opening boards.”
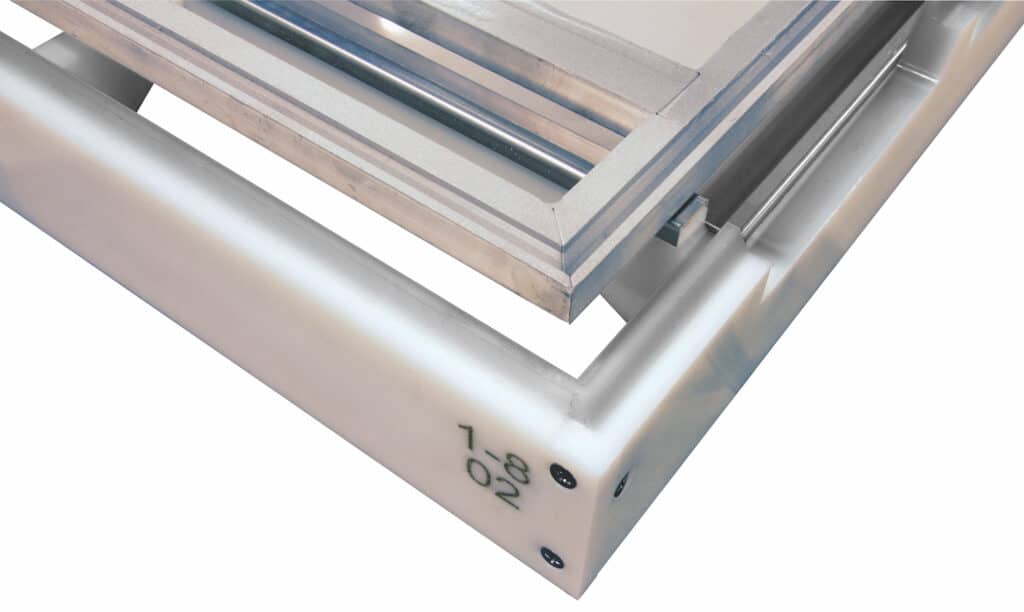
Material leaks in sieve stacks are often the result of worn gasketing that is near the end of its service life. Therefore, the removal of sieve-to-sieve and gasketing eliminates this issue, subsequently increases the ease and efficiency of maintenance and inspections. Joel Younger, plant manager at Bay State Milling Co. in Woodland, CA stated that “We have specific granulations we need to meet and the gasket seals between tray-to-sieve along with sieve-to-sieve felt seals have failed quite frequently, resulting in a lot of downtime and frustration. The Summit Sieves, with zero felt and interlocking sieves/inserts, have eliminated these issues all together. The felt free design is so much cleaner and user friendly. This interlocking Summit Sieve design has proven itself so far and should keep us running with a lot less downtime and frustration, but most importantly allowing us to maintain the product separations we need for our customers.” Users can also expect to see cleaner separations with added screen area, and no chance of oversized particles leaking around finer screen meshes.
The lightweight Summit Sieve has received fantastic reviews from others who have also made the switch with Great Western:
“We have installed Great Western Summit Sieves at three Ardent Mills locations. The millers like the sturdy sieve construction and the secure manner that the tray fits into the body of the sieve. Replacing the sieve-to-sieve felt seal between traditional sieves with the Summit’s mechanical interlocking design reduces time required for replacing/refastening felt, as well as removing a possible source of contamination from the felt. At one location, the conventional sieves that we replaced were prone to leaking oversized material into the flour. We tried a number of times to re-felt the sieves, but could not resolve the issue with specky flour. We thought that this would be a good opportunity to test the Summit sieve and we were pleased that the new Summit stack resolved the issue. I’m looking forward to seeing more Summit Sieves in our mills.”
– Scott Martin, Senior Director of Technical Milling, Ardent Mills, Denver, CO
“I believe that the sieves are very well built and put together very well. They press together very well, closing that gap and potential for sieves to leak. I look forward to seeing the future of how these sieves will grow and continue to be used in many mills to come.”
– Stephen Banks, Head Miller, Grain Craft – Barnesville, GA
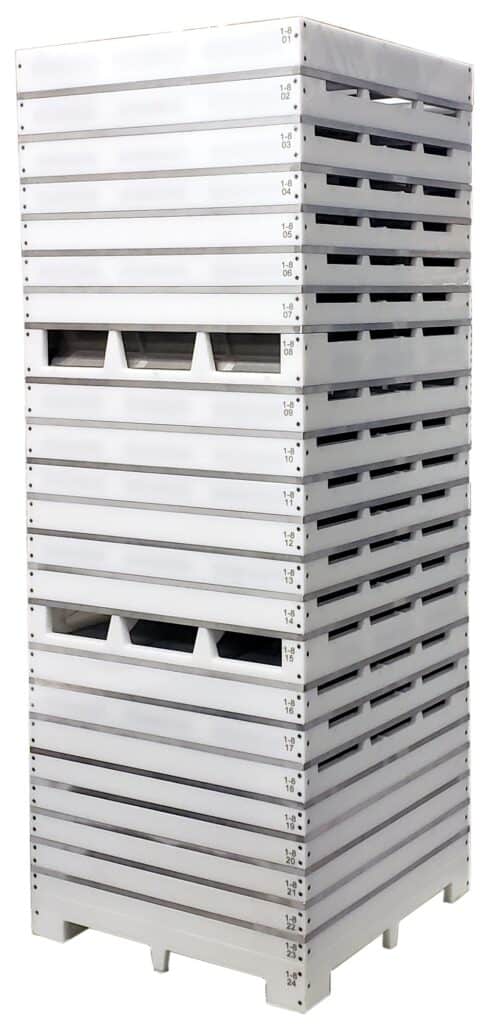
Other features of the Summit Sieve include minimal number of fasteners that have been strategically positioned outside the product zone to reduce ricks of contamination.
An overall stronger design with fewer parts gives peace of mind that product quality will be improved.
The Summit Sieve is available in a range of sizes to fit North American and European sifters.
For more information about the Summit Sieve visit www.gwmfg.com, call 800-682-3121 or email us at sifter@gwmfg.com.