The air gun tank is connected to an air compressor. A volume of compressed air between 4 & 400 Liters is released instantly through a suitable outlet. The AIRCHOC® air gun acts directly on the product. The effect obtained corresponds to a blast. Each programmed shot avoids a blockage of the material and guarantees the production process flows with no stop.
The use of an AIRCHOC® air cannon stabilizes and optimizes the industrial process. Indeed, when the cleaning is done too late, it can lead to a loss of material (hardened material for example), a contamination or fermentation of products, or even a temporary stop of production.
The AIRCHOC® is designed to be installed on raw material storage units (sand, powders, flours, grains, wood chips, peat, straw, mulch, etc.). AIRCHOC® can also be found at the end of the process on fly ash or lime silos.
3 examples of installations at some of STANDARD INDUSTRIE International’s customers:
For COLAS Group, concrete manufacturer
Processed material: sand with a particle size -0 to 4
Problem:
Regular build-ups on the storage silo for sand with a grain size of 04.No material could be extracted because of the build-ups. The customer used to poke from the moving skip located below and create a dangerous movement for the operator.
- Installation of an AIRCHOC® 50 Liters in wireless version
- Manual firing of the AIRCHOC® via remote control from the control station.
Result
Elimination of clogging and safety for the operator.
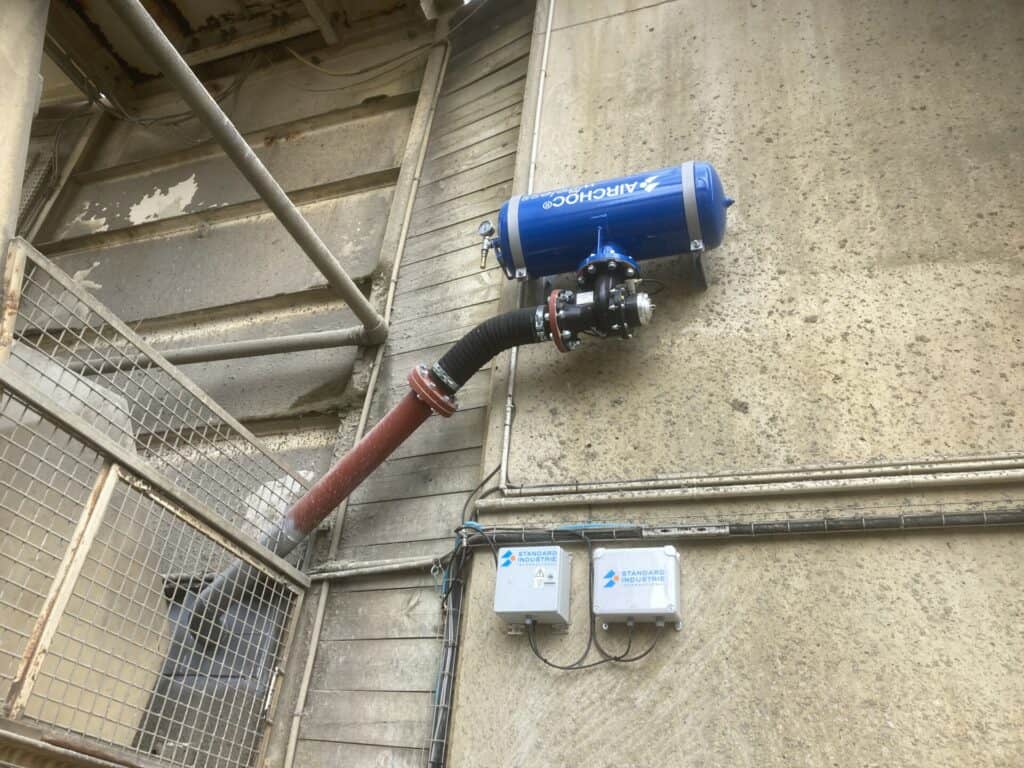
For IDEX environnement, biomass boiler operator
Material processed: 69m³ of biomass / hour (wood chips, wood shavings, Related sawmill products)
Problem:
The boiler burns 150 000 tons/year of biomass
The customer faces issues with ash deposit building up on the bundles of his 2 economizers (eco 1.1 + eco 1.2). This decreases the gasflow speed that needs to be treated. IDEX main cleaning tool was the soot blowers in its boiler. Over the years those soot blowers became insufficient to face the new build ups. Moreover higher maintenance costs were to be considered.
Solution:
- 4 AIRCHOC® air cannons were installed on the first row of beams on the economizer 1.
- The choice of a 200-liter tank allows a large volume of air to cover all the installed beams.
- The customer adapted the firing frequency of 1 shoot every 15 minutes.
Result:
IDEX is satisfied with the result because the flue gas treatment circuit recovered its efficiency as it could be clean and the boiler can meet its production targets. Moreover, maintenance costs were reduced.
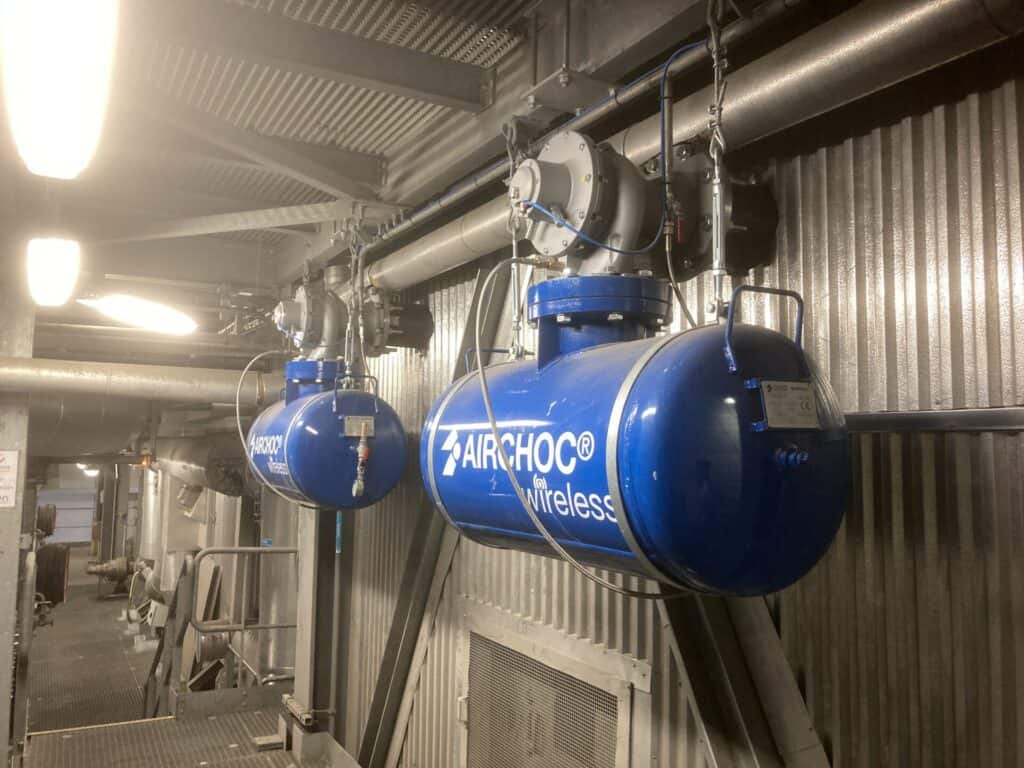
KNAUF, manufacturer of gypsum
Processed Material: gypsum
Problem:
The gypsum, with variable moisture content can be sticky and therefore hard to extract.
Solution:
The installation of AIRCHOC® air cannons at various strategic points at the beginning of the process, especially when the gypsum is still in a powder form has made it possible to solve the flow problems and made the extraction of the product easier
Result
The customer, satisfied with this solution, regularly upgrades its fleet of AIRCHOC® air cannons by replacing the old models with new ones.
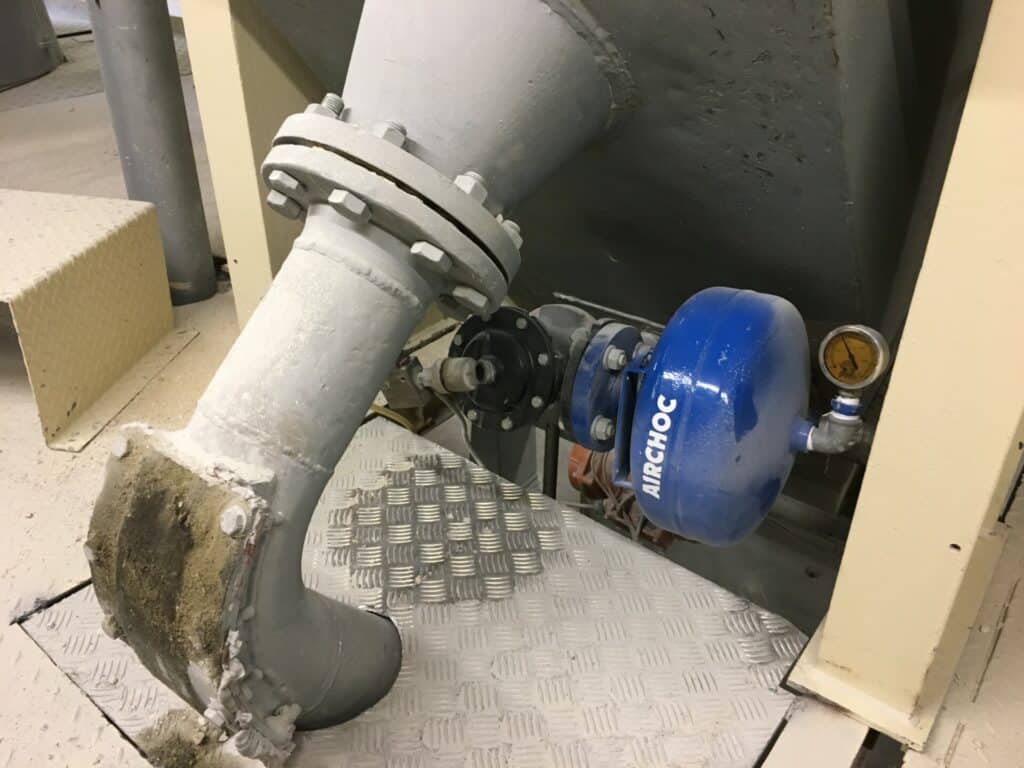