It has research centers in Portugal, the USA, and China; industrial-scale production units in Portugal, Ireland, and China; and offices in Hong Kong, India, and Switzerland. ACS was asked to replace the cyclone from the spray dryer manufacturer in New Jersey (USA). The goal was to increase the recovery of very fine and valuable powder (Fig. 1).
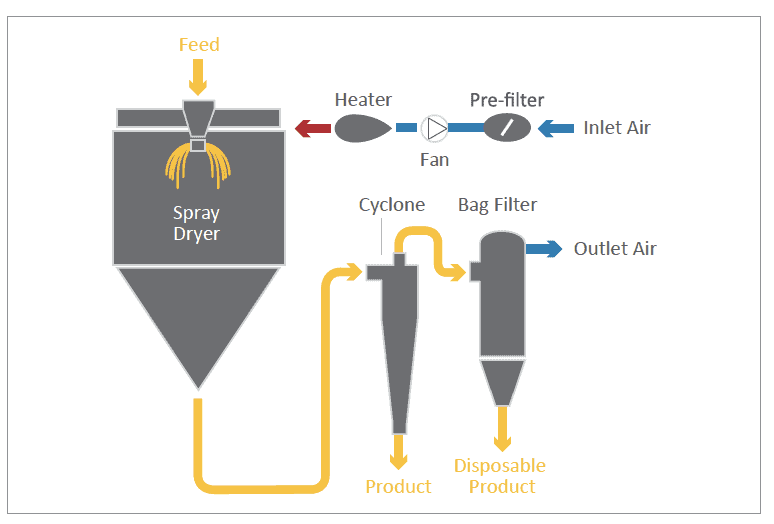
Identifying the problem and solution
To increase powder recovery, considering a design flow rate of 82 kg/h, a median particle size of 1.6 μm, and a true particle density of 1.61 g/ml, ACS designed and supplied a high-efficiency cyclone, the Hurricane HR with ø130mm. Hovione provided the detailed operating conditions and the total particle size distribution (Fig. 2). Using ACS’s numerical simulation tool – PACyc (Particle Agglomeration in Cyclones), ACS estimated a reduction of powder losses from 40% down to 16%.
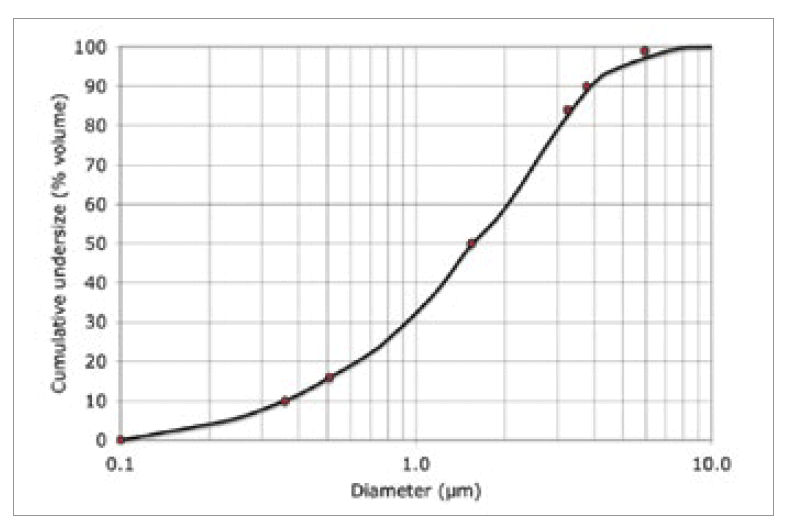
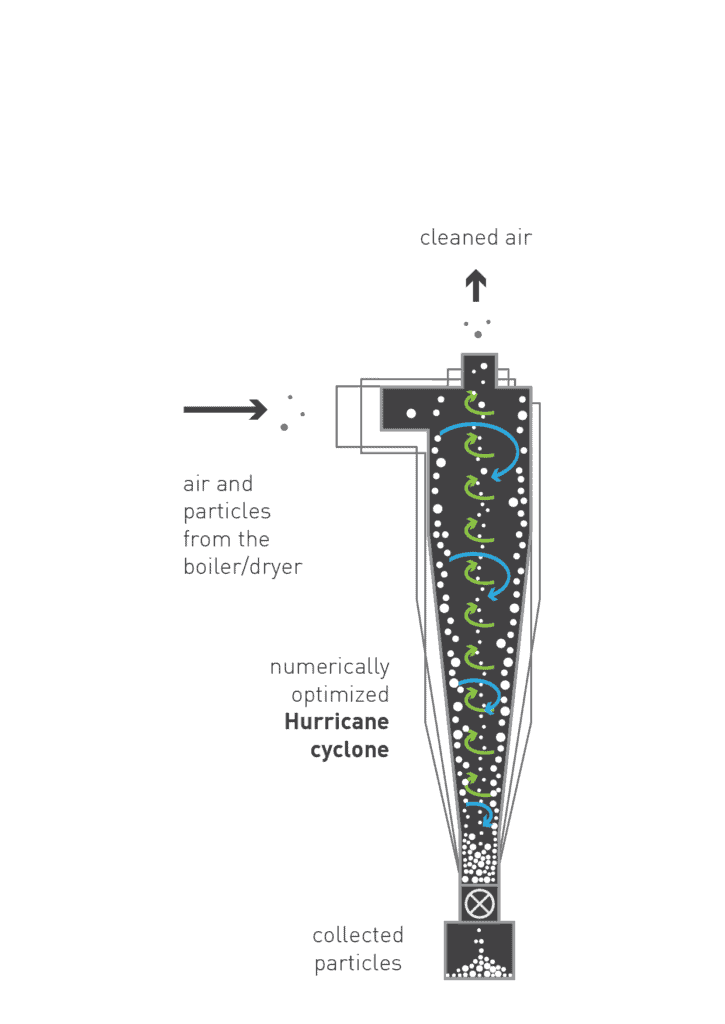
Understanding how cyclones word
The separation dynamics inside a cyclone is very difficult to model. Cyclones are usually designed empirically or, less often, according to models which do not consider the interparticle agglomeration inside the cyclone. ACS has developed its own unique model for cyclone efficiency prediction which considers agglomeration in turbulent flow fields – The PACYC MODEL (Chemical Engineering Journal 162 (2010) 861–876.
Optimizing cyclone efficiency
Supported by the PACyc Model, ACS can rapidly generate millions of virtual prototypes (cyclone geometries) and, through numerical optimization, select the best geometry for each given case. The design takes into consideration several economical and operational constraints, such as size, pressure loss, or manufacturing cost.
ACS Hurricane HR cyclones have been demonstrated to be more efficient than any other known cyclone available in the marketplace for the same pressure drop and manufacturing cost.
ACS’ competitive advantage is sustained by a unique ability to accurately estimate – and consequently guarantee – a requested efficiency, resulting in better cyclones, tuned for their specific application.
Design Basis
- Type of powder [Inhalable API]
- Particle density ds (g/ml) [1.61]
- Particle size distribution [See Fig.2]
- Gas composition [N2]
- Design flow rate (Kg/h) [112]
- Solids content (g/h) [50]
- Gas temperature (oC) [89]
- Operating pressure (mbarg) [Atmospheric]
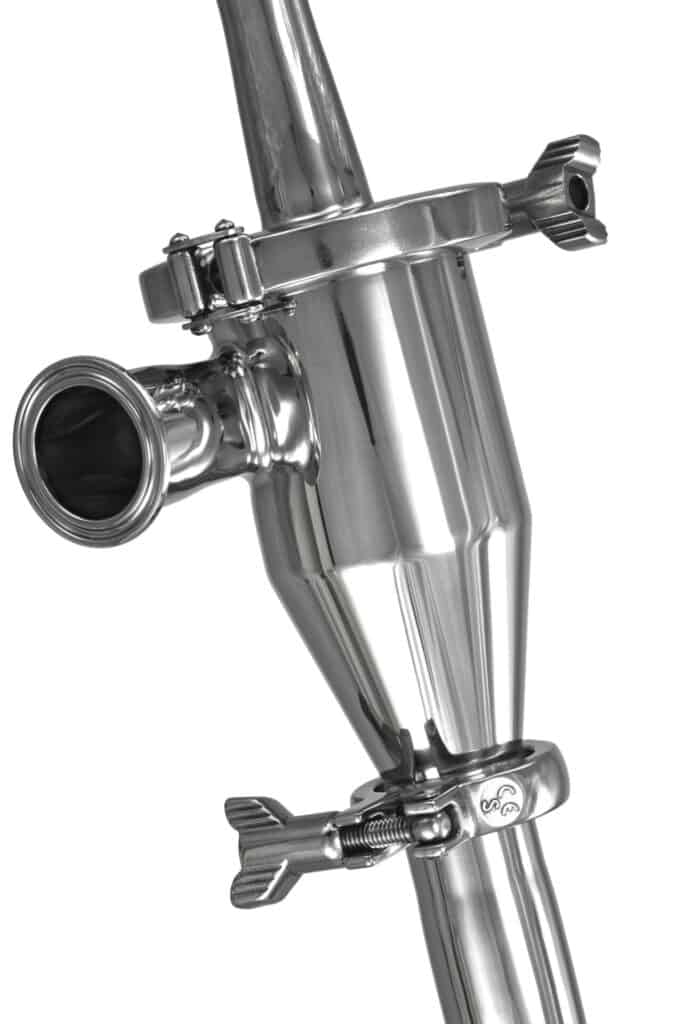
Hurricane SPECS | expected performance
Diameter (mm) [130]
Material [AISI 316L S.S.]
Internal surface finishing [Ra < 0.4 μm]
Internal welds [Ground Smooth to Ra < 0.4 μm]
External finishing [Ra < 0.4 μm]
External welds [Ground Smooth to Ra < 0.4 μm]
Expected collection efficiency (%) [78.3 – 83.1%]
Verified collection efficiency (%) [84%]
Conclusion
The separation efficiency predictions matched the experimental results in the clients’ facilities and a substantial increase in powder collection was verified. ACS’s global efficiency proved to exceed 80%, while the competitor cyclone never reached efficiencies above 60%. The success provided by this installation led to the supply of additional cyclones.