1. What factors have to be taken into consideration when designing screening machines?
The role that the machine will play in the process is crucial for the selection of the right screening technology. Typical separation processes are protective screening, coarse or fine grain separation, grading and straining and de-agglomeration. Once the basic function of the screening machine has been clarified, the customer’s objective is discussed. What number of fractions and what grain distribution should the screening product be separated into? How high is the desired throughput rate? The specific properties of the bulk solid also play a significant role. Moisture content, flow properties, break sensitivity and even the shape of the product are among the key factors. In order to achieve optimal results even for challenging products, it is not unusual for additional equipment to be required: if the product tends to generate stuck particles, then a screen-cleaning system should be installed. Information about pressure tightness or whether the machine is to be positioned in an ATEX zone also has to be taken into account, of course. Just like various requirements for the cleanability of the machine, the materials or surface treatments.
2. In practice, a distinction is made between vibration, centrifugal and stroke or jigger screening machines. What applications/areas of application are vibration screening machines suitable for?
Vibration screening machines have a very broad scope and, despite the relatively low amplitudes, achieve high accelerations which reduce stuck particles and guarantee outstanding screening performance. The key parameters such as screen inclination, vibration motor tilt angle and vibration motor imbalance can be quickly and easily adjusted as appropriate for various screening tasks and can also be documented. Laterally arranged vibration motors allow for very compact screening machines with a low installation height which can be integrated into tight conditions and take up very little space.
3. To what extent have the requirements for screening technology changed in recent years and what changes do you expect in the next five years?
It is important for us to recognize trends early and incorporate them into our product development. In recent years, we have been able to optimize key components of our screening machines thanks to state‑of‑the‑art construction methods, meaning that the housing covers are lighter and the screening machines are more energy-efficient, for example. In the next five years, we expect that demand for hygienic machines will increase in particular. At the same time, the requirements for the technical documentation and the qualification of machines and systems will become ever more complex. The increased requirements for the cleanability of screening machines were also the reason for the further development of our JEL Konti vibration screening machine, which was designed in accordance with the principles of hygienic design.
JEL Konti – easy handling, thorough cleaning
Hygienic machine solutions are in higher demand than ever before. And not just in the food and pharmaceuticals industries – value is often placed on clean production in the chemicals or plastics industries too. This is not always a question of preventing bacterial growth inside the machine and thus contamination of the product. Prevention of cross-contamination with other products or protection of the operating personnel from dusts which are produced are other reasons which often justify the procurement of a hygienic machine solution.
With the further development of the JEL Konti vibration screening machine, J. Engelsmann reacts to the increased demand for high-quality and hygienic machines. Optimized according to the basic principles of hygienic design, the JEL Konti is easy to use and easy to clean – despite a rectangular design.
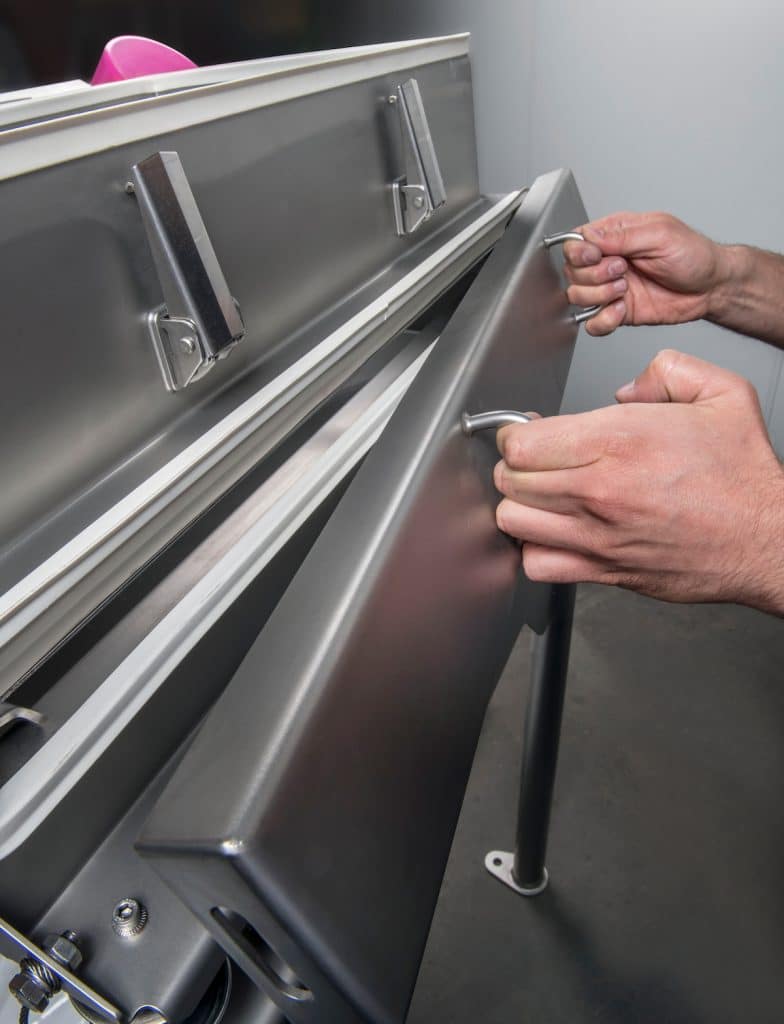
By their very nature, rectangular shapes have the downside that dirt and product residues can easily get stuck in the corners and edges. These dead spaces are hard to reach for cleaning purposes, meaning that deposits can easily spoil and contaminate the screening machine or the screening product. The JEL Konti’s rectangular screening trough was therefore the central focus of the redesign and is now constructed with larger radii. As a result, the whole of the interior through is easily accessible for cleaning purposes and has no dead space. Interior seals can be reached easily and can be removed, cleaned and then installed again quickly and without the use of tools. As a result, the Konti can be cleaned thoroughly without taking too much time.
Operators should also pay attention to a hygienic design in areas which are not in direct contact with the product because product residues can spoil here too, and these contaminations can get back into the interior of the machine. For this reason, the new JEL Konti also has hygienic design features outside the screening trough. The entire screen housing is kept minimalist and is easy to wipe down thanks to smooth surfaces. Instead of rubber hollow springs, the machine is supported, where necessary, on open stainless steel springs which can easily be cleaned. The machine is set up on a frame made from round pipes, which accumulate less product build-up that the traditional square design.
Screen change in just 30 seconds
It’s not just the cleaning of a screening machine which should be easy, handling should too. Inspection and changing the screen insert in particular are work steps which generally occur regularly and should thus be quick to carry out. Thanks to its special drawer system, changing of the screen insert on the JEL Konti can be done in a matter of seconds. Once the front cover has been removed, the insert can be pulled out of the front of the screen housing like a drawer. The screen doesn’t need to be disconnected from the product feed and discharge units, let alone dismantled. As a result, the whole process doesn’t take longer than 30 seconds. This not only saves valuable time when changing the screen, it also means inspection of the screen insert can be done in just a few steps. Comparable screening machines generally have to be disconnected from the product feed unit first so that the cover and the individual screen decks can be dismantled and removed from the machine. In order to make handling even easier, all covers have been weight-optimized and the closure mechanisms are designed as quick-release mechanisms or star grips so that the JEL Konti can be operated with no tools.
Every bulk solid has its own, specific properties. Moisture content, break sensitivity, grain size and flow properties are just a few of the factors which affect the design of a screening machine and the screening result. In order to achieve an optimum result even for products with more unfavorable properties and in order to be able to screen various products using one machine, many of the JEL Konti’s parameters can also be retroactively adjusted. The screen is quickly adjusted for the respective product through regulation of the screen inclination, oscillation amplitude or the vibration motor tilt angle. Very finely powdered bulk solids with a grain size of less than 100 µm often cause dust emissions, which in turn can cause cross-contamination or harm the operator. In these cases, the tightness of the production equipment is the top priority. Thanks to the JEL Konti’s new sealing mechanism, the screen achieves a dust and gas tightness level of 50 mbar and can thus be used for the finest powders.
Thanks to the implementation of hygienic design features, the new JEL Konti can now also be used for extremely sensitive production environments. And the new variant also demonstrates easy handling and rapid screen changing for applications in the chemical and plastics sectors. Available as a single and double-decker with screening surfaces ranging from 0.18 to 4 m², the vibration screening machine is suitable for small or large product volumes; it achieves throughput capacities of up to 20 t/m².