These materials must be dosed in such proportions as to ensure the quality of the container, prevent the passage of oxygen into the interior and be suitable for containing something as delicate as milk inside, as well as the production costs, depend on being able to deliver the precise amount of material at the right time of each component to the extruder.
So, dry material feeders for production processes, basically, refers to providing a constant and accurate flow for any grains, fibers and powders that will be used in other processes, such as plastic injection, extrusion, solid components in chemical reactors, food preparation, pharmaceuticals, among others. This operation is of vital importance in production processes, as it affects product quality, production capacity, and operating costs.
Therefore, material dosing must take into consideration three important variables:
- Metering, how we are going to measure the quantities to be dosed, by volume or by weight.
- Transport, how the material will be transported to the next process, such as screws, conveyor belts, discs, among others.
- Control, related to the way in which the dosing itself will be controlled, either by weight readings, either by gain or loss, the number of revolutions that a screw gives, among others.
Based on these 3 variables, there are 2 types of dosing: volumetric and gravimetric. In volumetric dosing, the delivery of the material is based on a calibrated correlation between the dosing flow or quantity, and the adjustment of the pitch or revolutions of the conveying medium, so it is not necessary to weigh constantly. In the case of gravimetric dosing, the dosed materials must be constantly weighed and delivered to the next process, which allows for greater accuracy, as the control is on the scale. Some characteristics of both systems are:
Volumetric
- No control scales.
- Environmental conditions as well as differences in density and particle size can affect the process.
- Simpler dosing.
- Adjustment by calibration (volume per unit time).
- Requires regular ambient conditions.
- Dosing records are not necessary.
- Non-critical accuracy.
- Usually inexpensive systems.
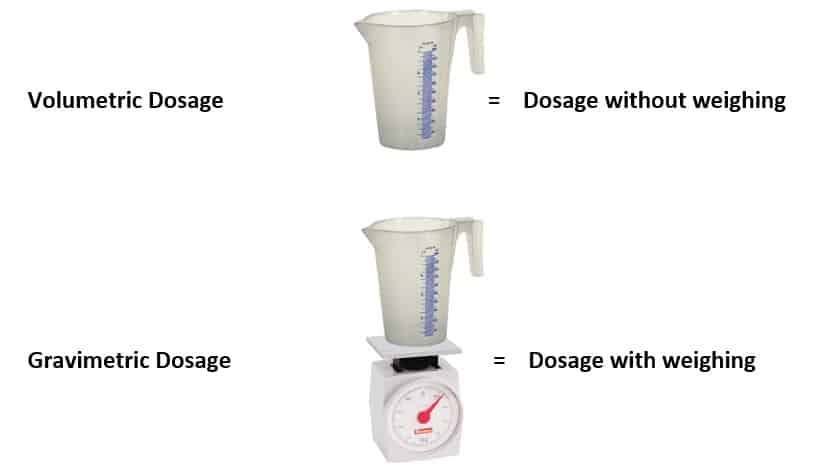
Gravimetric
- With scale control.
- Humidity or temperature conditions do not affect the process, nor do bulk density or particle size.
- Adjustments are based on the programming of the required weights or proportions.
- Possibility of working in weight gain or weight loss.
- Recording/traceability of dosing and errors.
- Accurate system.
- More expensive vs volumetric dosing system
The choice of one system or another will depend on the characteristics of the process, as well as the need for control. It is common to add minority products, such as catalysts or dyes, in a gravimetric way, where only a few kilos or grams are required in relation to majority components that can add up to hundreds of kilograms and that can be volumetrically dosed, but always depends on your accuracy needed on the of the recipe and process.
From COSCOLLOLA ENGINEERING we evaluate your needs and design solutions to solve feeding problems, improve operations and the quality of the processes, selecting the best systems and equipment.